Separating Metals for Batteries via Gels
Separating Metals for Batteries via Gels
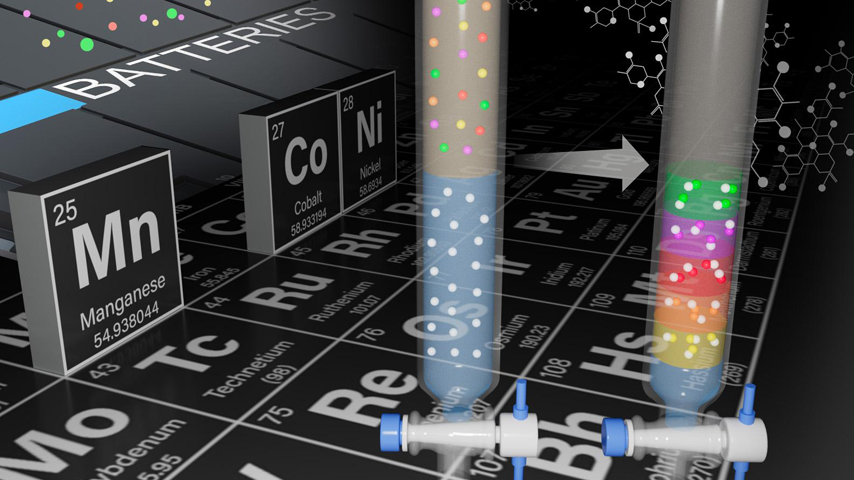
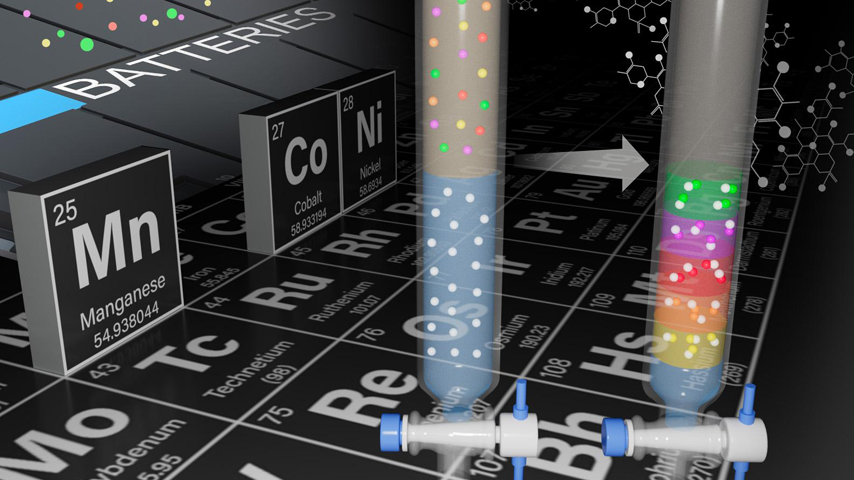
A new process uses a gel to enable different metals to precipitate out at different speeds.
The surge in demand for electric vehicles (EVs) and renewable energy storage solutions has thrown a spotlight on the importance of lithium-ion batteries, which rely on materials like lithium, cobalt, nickel, and manganese. The limited availability and geographical concentration of these critical materials pose significant supply chain risks and environmental concerns.
One way to avert this challenge is through recycling batteries to recover critical materials. Researchers at the Pacific Northwest National Laboratory (PNNL) in Richland, Wash., are working on innovative solutions to the challenges of battery recycling. Their work involves developing new materials and processes that can improve the efficiency and selectivity of critical material recovery—all without the need for expensive chemicals, membranes, or ligands.
This not only supports recycling efforts but also helps in the development of new battery chemistries that are less dependent on scarce resources.
“The hard reality is that transitioning to a green economy will be powered by critical materials—such as lithium, cobalt, and nickel—that are finite,” said Elias Nakouzi, a materials scientist with PNNL. “New technologies for recycling electronics are needed to mitigate geopolitical conflict, unethical mining practices, and environmental harm.”
Recycling batteries involves several challenges, notably the efficient separation and recovery of valuable materials. Traditional methods such as pyrometallurgy and hydrometallurgy have their drawbacks. For instance, pyrometallurgy is a high-temperature process that is energy-intensive and can lead to the loss of valuable materials. Hydrometallurgy, or chemical leaching, is more selective, but it often involves complex and costly chemical treatments to separate the materials from the leachate.
One promising approach of PNNL’s research is the use of advanced separation techniques that can selectively recover critical materials from the solution obtained after dissolving used batteries. These techniques may involve novel chemical processes, solvent extraction methods, or the use of specific absorbents designed to bind selectively to certain materials.
The subject of a provisional patent, an approach developed at PNNL focuses on the separation of small batches of materials in solution. These solutions contain mixtures of lithium, manganese, cobalt, and nickel placed on top of the gel and then allowed to move through the gel. The separation of materials is made possible because of the differences with which ions travel through a gel material and precipitate into solids at different rates.
Learn About the Benefits of ASME Membership
Consider an instance where a mixed solution moves through a gel-filled tube. As this occurs, metallic ions precipitate out at different times, with the fastest forming metals consuming the precipitating agent. The process then moves on to the next fastest, until all are precipitated out and separated.
This contrasts with traditional methods of just mixing a precipitating agent and the ions in a solution without gel. Mixing without gel produces solids where the metal ions separated are proportionately equal, with a formed metal that is not so pure.
By contrast, the gel-based separation produces an ion that is about 96 percent pure. When scaled up, this may lead to better ways to recover the metals for larger-scale applications.
“The most critical step for deploying this technology is improving the throughput to achieve a faster separations process,” Nakouzi said. “We are solving this problem in our next study, which focuses on rapid magnesium extraction from seawater. Another ongoing study involves recycling permanent magnets to recover rare earth critical elements such as neodymium and dysprosium.”
Improving the recovery of critical materials from dissolved batteries could have significant implications. It can reduce reliance on virgin materials, decrease environmental impact, and enhance the sustainability of the battery supply chain. Moreover, efficient recycling processes can contribute to the security of material supply, which is crucial given the expected growth in demand for batteries in the coming years.
Jim Romeo is a technology writer based in Chesapeake, Va.
One way to avert this challenge is through recycling batteries to recover critical materials. Researchers at the Pacific Northwest National Laboratory (PNNL) in Richland, Wash., are working on innovative solutions to the challenges of battery recycling. Their work involves developing new materials and processes that can improve the efficiency and selectivity of critical material recovery—all without the need for expensive chemicals, membranes, or ligands.
This not only supports recycling efforts but also helps in the development of new battery chemistries that are less dependent on scarce resources.
“The hard reality is that transitioning to a green economy will be powered by critical materials—such as lithium, cobalt, and nickel—that are finite,” said Elias Nakouzi, a materials scientist with PNNL. “New technologies for recycling electronics are needed to mitigate geopolitical conflict, unethical mining practices, and environmental harm.”
Recycling batteries involves several challenges, notably the efficient separation and recovery of valuable materials. Traditional methods such as pyrometallurgy and hydrometallurgy have their drawbacks. For instance, pyrometallurgy is a high-temperature process that is energy-intensive and can lead to the loss of valuable materials. Hydrometallurgy, or chemical leaching, is more selective, but it often involves complex and costly chemical treatments to separate the materials from the leachate.
One promising approach of PNNL’s research is the use of advanced separation techniques that can selectively recover critical materials from the solution obtained after dissolving used batteries. These techniques may involve novel chemical processes, solvent extraction methods, or the use of specific absorbents designed to bind selectively to certain materials.
The subject of a provisional patent, an approach developed at PNNL focuses on the separation of small batches of materials in solution. These solutions contain mixtures of lithium, manganese, cobalt, and nickel placed on top of the gel and then allowed to move through the gel. The separation of materials is made possible because of the differences with which ions travel through a gel material and precipitate into solids at different rates.
Learn About the Benefits of ASME Membership
Consider an instance where a mixed solution moves through a gel-filled tube. As this occurs, metallic ions precipitate out at different times, with the fastest forming metals consuming the precipitating agent. The process then moves on to the next fastest, until all are precipitated out and separated.
This contrasts with traditional methods of just mixing a precipitating agent and the ions in a solution without gel. Mixing without gel produces solids where the metal ions separated are proportionately equal, with a formed metal that is not so pure.
By contrast, the gel-based separation produces an ion that is about 96 percent pure. When scaled up, this may lead to better ways to recover the metals for larger-scale applications.
“The most critical step for deploying this technology is improving the throughput to achieve a faster separations process,” Nakouzi said. “We are solving this problem in our next study, which focuses on rapid magnesium extraction from seawater. Another ongoing study involves recycling permanent magnets to recover rare earth critical elements such as neodymium and dysprosium.”
Improving the recovery of critical materials from dissolved batteries could have significant implications. It can reduce reliance on virgin materials, decrease environmental impact, and enhance the sustainability of the battery supply chain. Moreover, efficient recycling processes can contribute to the security of material supply, which is crucial given the expected growth in demand for batteries in the coming years.
Jim Romeo is a technology writer based in Chesapeake, Va.
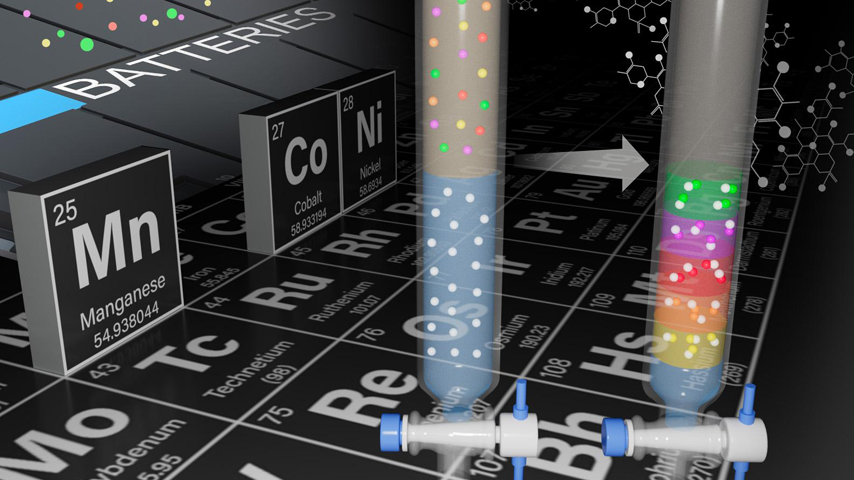
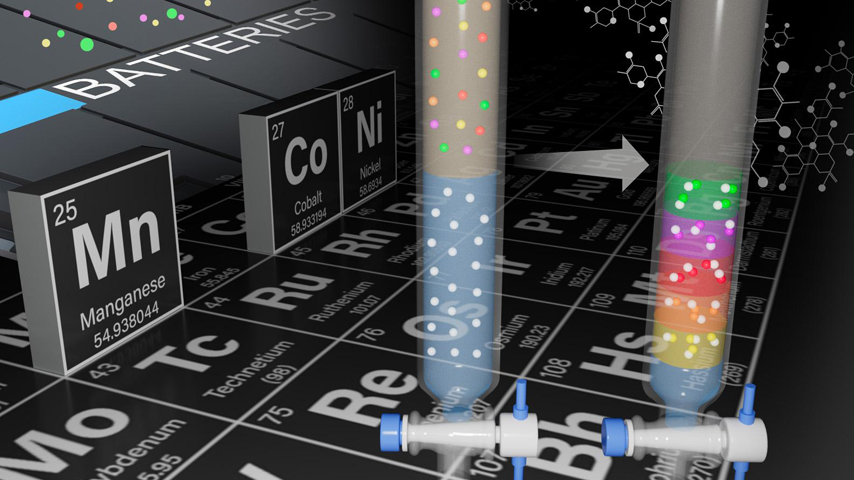