Problem-solving for Engineers: Root Cause Analysis Fundamentals
Course Type:
Course Number:
Credits:
Language:
Learn root cause analysis (RCA) fundamentals, explore RCA tools' purpose and application, and perform RCA on real-world problems to find solutions.
This Standard was last reviewed and reaffirmed in {{activeProduct.ReaffirmationYear}}. Therefore this version remains in effect.
{{activeProduct.Title}}
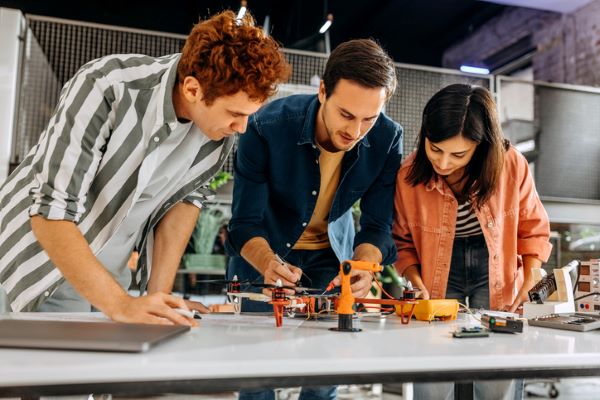
Digital products are restricted to one per purchase.
{{activeProduct.CurrencySymbol}}{{ formatPrice(activeProduct.ListPrice) }} was {{activeProduct.CurrencySymbol}}{{ formatPrice(originalPrice) }}
{{activeProduct.CurrencySymbol}}{{ formatPrice(activeProduct.ListPriceSale) }} was {{activeProduct.CurrencySymbol}}{{ formatPrice(activeProduct.ListPrice) }}
{{activeProduct.CurrencySymbol}}{{ formatPrice(activeProduct.ListPrice) }} was {{activeProduct.CurrencySymbol}}{{ formatPrice(originalPrice) }}
{{activeProduct.CurrencySymbol}}{{ formatPrice(activeProduct.ListPriceSale) }} was {{activeProduct.CurrencySymbol}}{{ formatPrice(originalPrice) }}
{{activeProduct.CurrencySymbol}}{{ formatPrice(activeProduct.MemberPrice) }} was {{activeProduct.CurrencySymbol}}{{ formatPrice(originalPrice) }}
{{activeProduct.CurrencySymbol}}{{ formatPrice(activeProduct.MemberPriceSale) }} was {{activeProduct.CurrencySymbol}}{{ formatPrice(originalPrice) }}
*Excluding Lite Members
Final invoices will include applicable sales and use tax.
Print or Share
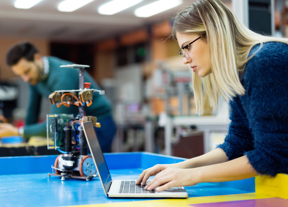
Get papers online in the ASME Digital Collection
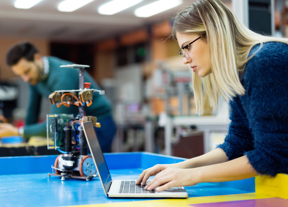
Sorry, we only have available spots for this course. Would you like to add those to your cart?