A Large-Format Solution for 3D Microscopes
A Large-Format Solution for 3D Microscopes
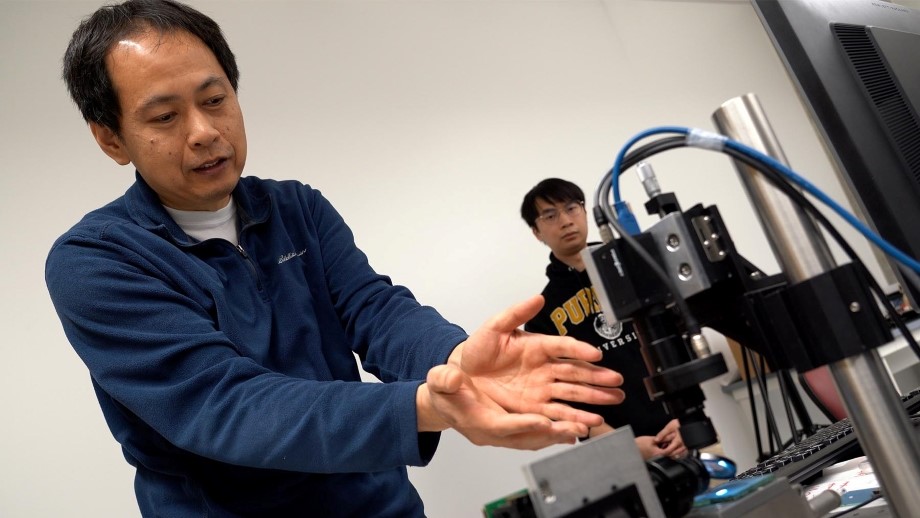
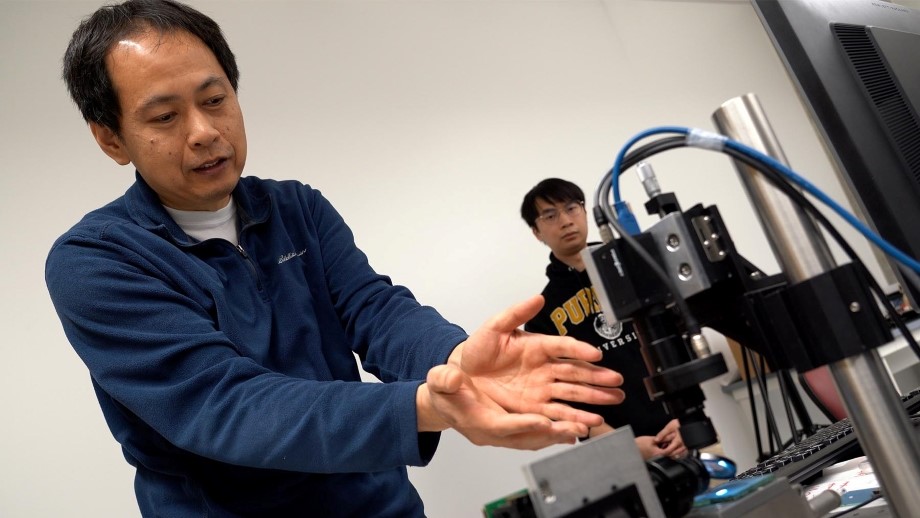
Electrical tunable lens technology may improve 3D microscopes by lowering their costs and making them faster and easier to use, without any required training.
Song Zhang was skeptical when a student asked him whether the electrical tunable lens technology used in large-format 3D imaging could be applied to 3D microscopes. After all, a microscope’s depth of field can be measured in the tens or hundreds of micrometers whereas large-format 3D imaging allows for a range of meters.
If anyone could make it work, however, it would be Zhang, who is a mechanical engineering professor at Purdue University in West Lafayette, Ind. He is an expert in large-format 3D imaging as well as 3D printing and has even collaborated on a 3D music video with the band Radiohead.
Now, Zhang and his team at Purdue have developed patented and patent-pending methods they believe could be a game changer in improving accessibility of 3D microscopes by lowering their costs and making them faster and easier to use, without any required training. The key, it turns out, was electrical tunable lens technology (ETL).
“The challenges we had [were], if you do any autofocusing, then you have a person who knows what they’re doing. You cannot recalibrate this kind of focus on the fly because the calibration takes a while,” Zhang said. Without ETL, microscopes are calibrated mechanically by humans. Depending on the geometry of the subject, Zhang said that could vary from 10 minutes to a few hours.
Demand for 3D microscopes remains strong as they can be used in a variety of applications for industries ranging from biomedicine and life sciences to semiconductor manufacturing, or, “any time people try to capture microscale 3D objects with a larger depth range,” according to Zhang.
“A mechanical system typically does not move at the pace of electronics,” Zhang said. Mechanical calibration requires precision to move the optical system up and down, significantly adding to product cost. ETL uses an optical technique called fringe projection to create a high-resolution 3D image of objects, changing the focal plane of the imaging system without mechanically moving parts.
ETL enables an automatic processing of three steps: the focus on an object, the determination of the optimal capture process and the creation of a high-quality 3D image.
More Like This: Uncovering Hot Spots in Electronics at Nanoscale
With funding from a grant from The National Science Foundation secured, Zhang and his team started research and testing, assembling prototypes and systems that used commercially available lenses. “We saw that we can use the same idea but just put it into a microscope,” Zhang said. Simple sounding, perhaps, but not without its challenges. Imaging objects with complex 3D geometry requires multiple focal planes to capture the entire object. The testing paid off as the team validated the ETL technology could respond to both forward and backward calibration, capturing each image slice of the 3D object for quick post-imaging assembly.
“We were able to adjust the focal plane through the electrical signal precisely,” Zhang said. “Everything still works regardless of the focal plane. That's very critical because without that, we will not be able to get a 3D image for the larger depths field,” Zhang said.
“Instead of letting a human manually adjust the focal plane, now can have a computer do the work,” Zhang said, making the user experience simpler and saving time throughout the imaging and post-production process.
Discover the Benefits of ASME Membership
“You do not need any skills to operate the microscope. Because everything is automated, you don't have to worry about it,” Zhang said.
Zhang and his team are now working to make 3D microscope ETL technology even faster, aiming to reduce calibration times further.
“The hardware limitation is something we try to ignore,” Zhang said. He believes additional opportunity to improve calibration time and accuracy lies in the tool’s operating software. “The software will tell you precisely how many focal planes to use and where you should set them,” he said.
More About Advanced Imaging: Image Capturing Device Mimics the Human Eye
Faster ETL response times would benefit applications requiring high speeds, such as in situ quality control, Zhang said. Health and life science applications may improve the measurement of tissue topology or help with adjustments to a medical device or robot.
Some of the team’s testing included using the technology to measure semiconductor chip flatness. “We are able to measure the chip very well with the depth range” Zhang said, noting how those measurements could apply to quality control during the manufacturing process.
The suite of patents assembled by the Purdue team to date includes methods on how to calibrate the ETL, how to create all-in-focus 3D images quickly and how to speed up the data acquisition process.
Nancy Kristof is a technology writer in Denver.
If anyone could make it work, however, it would be Zhang, who is a mechanical engineering professor at Purdue University in West Lafayette, Ind. He is an expert in large-format 3D imaging as well as 3D printing and has even collaborated on a 3D music video with the band Radiohead.
Now, Zhang and his team at Purdue have developed patented and patent-pending methods they believe could be a game changer in improving accessibility of 3D microscopes by lowering their costs and making them faster and easier to use, without any required training. The key, it turns out, was electrical tunable lens technology (ETL).
“The challenges we had [were], if you do any autofocusing, then you have a person who knows what they’re doing. You cannot recalibrate this kind of focus on the fly because the calibration takes a while,” Zhang said. Without ETL, microscopes are calibrated mechanically by humans. Depending on the geometry of the subject, Zhang said that could vary from 10 minutes to a few hours.
Demand for 3D microscopes remains strong as they can be used in a variety of applications for industries ranging from biomedicine and life sciences to semiconductor manufacturing, or, “any time people try to capture microscale 3D objects with a larger depth range,” according to Zhang.
“A mechanical system typically does not move at the pace of electronics,” Zhang said. Mechanical calibration requires precision to move the optical system up and down, significantly adding to product cost. ETL uses an optical technique called fringe projection to create a high-resolution 3D image of objects, changing the focal plane of the imaging system without mechanically moving parts.
ETL enables an automatic processing of three steps: the focus on an object, the determination of the optimal capture process and the creation of a high-quality 3D image.
More Like This: Uncovering Hot Spots in Electronics at Nanoscale
With funding from a grant from The National Science Foundation secured, Zhang and his team started research and testing, assembling prototypes and systems that used commercially available lenses. “We saw that we can use the same idea but just put it into a microscope,” Zhang said. Simple sounding, perhaps, but not without its challenges. Imaging objects with complex 3D geometry requires multiple focal planes to capture the entire object. The testing paid off as the team validated the ETL technology could respond to both forward and backward calibration, capturing each image slice of the 3D object for quick post-imaging assembly.
“We were able to adjust the focal plane through the electrical signal precisely,” Zhang said. “Everything still works regardless of the focal plane. That's very critical because without that, we will not be able to get a 3D image for the larger depths field,” Zhang said.
“Instead of letting a human manually adjust the focal plane, now can have a computer do the work,” Zhang said, making the user experience simpler and saving time throughout the imaging and post-production process.
Discover the Benefits of ASME Membership
“You do not need any skills to operate the microscope. Because everything is automated, you don't have to worry about it,” Zhang said.
Zhang and his team are now working to make 3D microscope ETL technology even faster, aiming to reduce calibration times further.
“The hardware limitation is something we try to ignore,” Zhang said. He believes additional opportunity to improve calibration time and accuracy lies in the tool’s operating software. “The software will tell you precisely how many focal planes to use and where you should set them,” he said.
More About Advanced Imaging: Image Capturing Device Mimics the Human Eye
Faster ETL response times would benefit applications requiring high speeds, such as in situ quality control, Zhang said. Health and life science applications may improve the measurement of tissue topology or help with adjustments to a medical device or robot.
Some of the team’s testing included using the technology to measure semiconductor chip flatness. “We are able to measure the chip very well with the depth range” Zhang said, noting how those measurements could apply to quality control during the manufacturing process.
The suite of patents assembled by the Purdue team to date includes methods on how to calibrate the ETL, how to create all-in-focus 3D images quickly and how to speed up the data acquisition process.
Nancy Kristof is a technology writer in Denver.