Induction Welding Can Bond Composite Metal Foam
Induction Welding Can Bond Composite Metal Foam
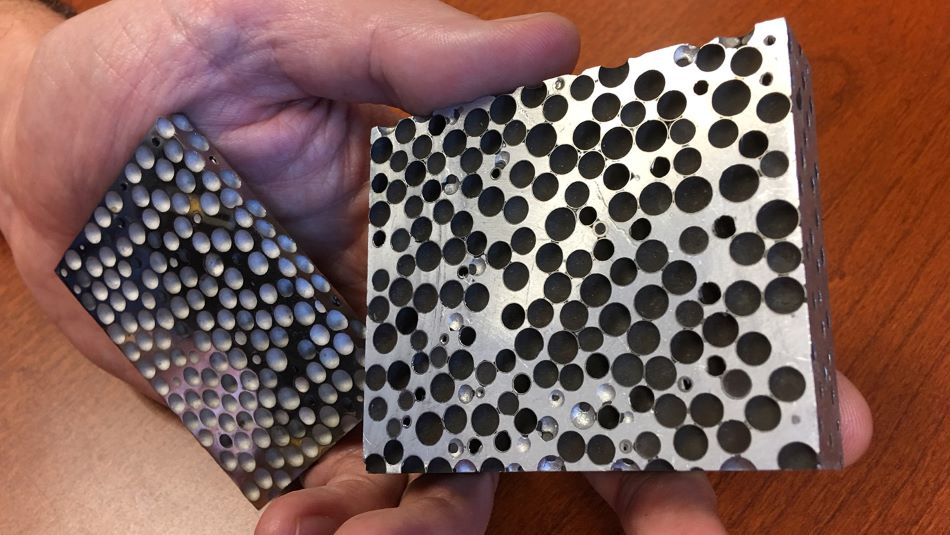
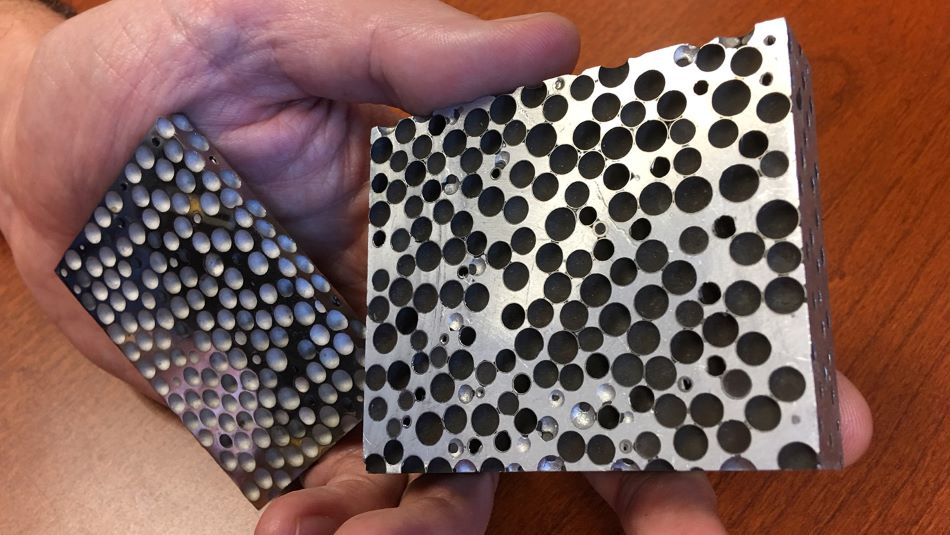
Researchers develop a technique for joining together sections of composite metal foam, a lightweight material that’s strong and tough.
A slab of metal that’s as strong as steel, as light as aluminum, can absorb impacts like plastic foam, and provides insulation against heat sounds like it has as much to do with magic as science. But the composite metal foam (CMF) developed by researchers at North Carolina State University in Raleigh has all these properties, making it an intriguing option for aerospace or military applications.
One drawback has been that those slabs couldn’t be welded together using standard methods to form larger components, such as aircraft wings or vehicle armor.
Recently, though, the research team that invented the material found a welding technique that can join pieces of CMF without sacrificing its properties.
Afsaneh Rabiei, mechanical and aerospace engineering professor at NC State, combined two advanced materials—metal matrix composites and metal foams—to invent CMFs in the mid-2000s. “The idea was to make a new material that is lightweight like a foam, but strong like steel,” Rabiei said.
The challenge was finding a way to produce a material that was mostly air—up to 70 percent by volume—embedded within a metal. The key breakthrough was realizing that the air could be enclosed by metal spheres; molten metal solidifies around the spheres to create a material with a much higher strength-to-weight ratio than a slab of solid metal.
Rabiei compares CMF to a “heavy-duty bubble wrap that can be created out of nearly any metal, alloy, or combination, and can be fine-tuned per application,” she said. “CMF has proven to absorb impact energy over two orders of magnitude higher than its bulk, solid parent material. It protects against high-speed impact, ballistics, blast and frags, nuclear radiation, extreme heat, fire, sound, and vibration, all at a third of the weight. A 100 percent steel CMF product weighs one-third that of solid steel, and equal weight to a solid piece of aluminum.”
In addition to high strength and impact resistance, the porous nature of the material limits the conduction of heat, since air is much less capable of conducting thermal energy than solid metal.
The light weight of CMF makes its potential for lightweighting components and products especially intriguing.
Discover the benefits of ASME membership
Up to now, however, applications have been limited due to challenges in forming larger pieces. Welding together samples of CMF degraded its properties. Tests with conventional welding methods that use direct heat to melt the metal resulted in some of the air-filled spheres in the CMF collapsing.
“Traditional fusion welding methods are ill-suited for metal foams due to their porous structure, which tends to be filled during welding, compromising performance,” Rabiei said.
The team looked at other welding methods to find a process that could heat the metal without softening the spheres. Eventually, it hit upon induction welding, which uses an induction coil to create an electromagnetic field to heat the metal for welding.
“Because CMF is only 30 to 35 percent metal, the electromagnetic field is able to penetrate deeply into the material, allowing for a good weld,” Rabiei said.
More about metal foams: Researchers Create Super Strong Porous Metal
Because the air pockets that make up most of the material are poor heat conductors, the energy transferred into the foam via induction builds up at the target rather than spreads. “This allows induction welding to heat up the targeted area for joining two pieces of CMF, but prevents the heat from spreading out from the site of the join,” she added. “This helps to preserve the CMF properties.”
During the testing, Rabiei observed that, although the weld line temperature climbed to over 2,000 °F, “We could still touch the material just a couple of inches away from the welding area, indicating the CMF’s ability to isolate the extreme heat and remaining touchable in such a short distance.”
With the successful results from induction welding, Rabiei now has a means of welding CMF components into groundbreaking products, without impairing their unique properties.
“Now, after decades of research and development on this novel technology, we can take it to the market and understand the needs from industry to be addressed by this novel platform technology, which has application across multiple industries,” she said.
According to Rabiei, CMF can play a major role in improving safety, fuel efficiency, performance, while lowering costs.
“The current materials in use in many of our current structures, such as automobiles, boats, tank cars carrying HAZMAT, canisters carrying nuclear waste material, and even airplanes, are too heavy and often made of many layers to tackle multiple issues using each layer,” Rabiei said. “There is a large margin for improvements.”
Mark Crawford is a technology writer in Corrales, N.M.
One drawback has been that those slabs couldn’t be welded together using standard methods to form larger components, such as aircraft wings or vehicle armor.
Recently, though, the research team that invented the material found a welding technique that can join pieces of CMF without sacrificing its properties.
Afsaneh Rabiei, mechanical and aerospace engineering professor at NC State, combined two advanced materials—metal matrix composites and metal foams—to invent CMFs in the mid-2000s. “The idea was to make a new material that is lightweight like a foam, but strong like steel,” Rabiei said.
The challenge was finding a way to produce a material that was mostly air—up to 70 percent by volume—embedded within a metal. The key breakthrough was realizing that the air could be enclosed by metal spheres; molten metal solidifies around the spheres to create a material with a much higher strength-to-weight ratio than a slab of solid metal.
Rabiei compares CMF to a “heavy-duty bubble wrap that can be created out of nearly any metal, alloy, or combination, and can be fine-tuned per application,” she said. “CMF has proven to absorb impact energy over two orders of magnitude higher than its bulk, solid parent material. It protects against high-speed impact, ballistics, blast and frags, nuclear radiation, extreme heat, fire, sound, and vibration, all at a third of the weight. A 100 percent steel CMF product weighs one-third that of solid steel, and equal weight to a solid piece of aluminum.”
In addition to high strength and impact resistance, the porous nature of the material limits the conduction of heat, since air is much less capable of conducting thermal energy than solid metal.
The light weight of CMF makes its potential for lightweighting components and products especially intriguing.
Discover the benefits of ASME membership
Up to now, however, applications have been limited due to challenges in forming larger pieces. Welding together samples of CMF degraded its properties. Tests with conventional welding methods that use direct heat to melt the metal resulted in some of the air-filled spheres in the CMF collapsing.
“Traditional fusion welding methods are ill-suited for metal foams due to their porous structure, which tends to be filled during welding, compromising performance,” Rabiei said.
The team looked at other welding methods to find a process that could heat the metal without softening the spheres. Eventually, it hit upon induction welding, which uses an induction coil to create an electromagnetic field to heat the metal for welding.
“Because CMF is only 30 to 35 percent metal, the electromagnetic field is able to penetrate deeply into the material, allowing for a good weld,” Rabiei said.
More about metal foams: Researchers Create Super Strong Porous Metal
Because the air pockets that make up most of the material are poor heat conductors, the energy transferred into the foam via induction builds up at the target rather than spreads. “This allows induction welding to heat up the targeted area for joining two pieces of CMF, but prevents the heat from spreading out from the site of the join,” she added. “This helps to preserve the CMF properties.”
During the testing, Rabiei observed that, although the weld line temperature climbed to over 2,000 °F, “We could still touch the material just a couple of inches away from the welding area, indicating the CMF’s ability to isolate the extreme heat and remaining touchable in such a short distance.”
With the successful results from induction welding, Rabiei now has a means of welding CMF components into groundbreaking products, without impairing their unique properties.
“Now, after decades of research and development on this novel technology, we can take it to the market and understand the needs from industry to be addressed by this novel platform technology, which has application across multiple industries,” she said.
According to Rabiei, CMF can play a major role in improving safety, fuel efficiency, performance, while lowering costs.
“The current materials in use in many of our current structures, such as automobiles, boats, tank cars carrying HAZMAT, canisters carrying nuclear waste material, and even airplanes, are too heavy and often made of many layers to tackle multiple issues using each layer,” Rabiei said. “There is a large margin for improvements.”
Mark Crawford is a technology writer in Corrales, N.M.