New Alloy Could Enable New Applications for Copper
New Alloy Could Enable New Applications for Copper
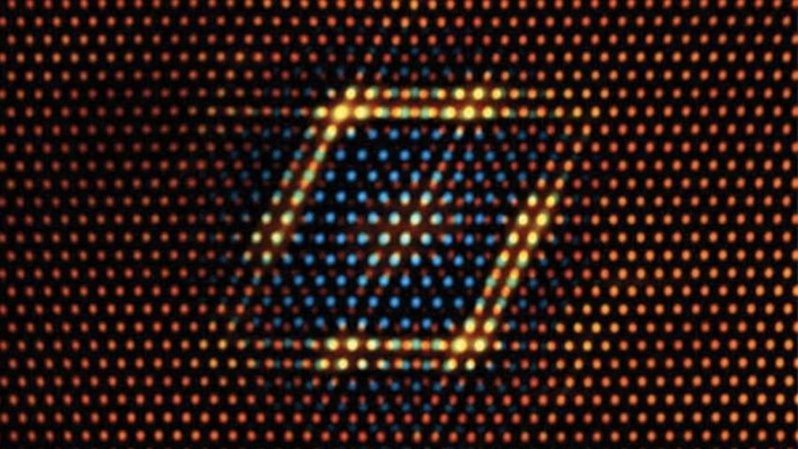
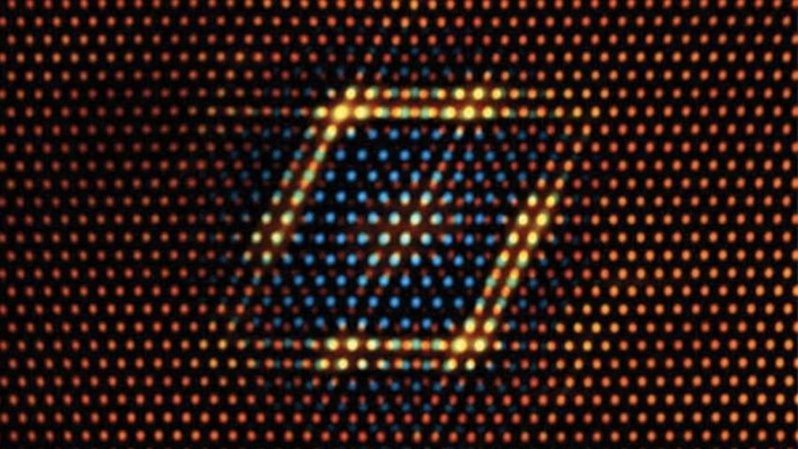
A multi-institution research group has developed a new copper nanocrystalline alloy with remarkable thermal and mechanical properties.
To effectively treat cancer, doctors must first provide a patient with the right diagnosis. This requires pathologists to use molecular testing to identify each cancer’s unique signature, such as changes in DNA, gene expression, microsatellite instability, or protein structure. Detecting such small but significant differences in the cells enables doctors to accurately classify a specific tumor type to target.
Kiran Solanki, a professor in the School for Engineering of Matter, Transport, and Energy at Arizona State University in Tempe, said that scientists can use a similar approach to optimize materials. By looking for the unique signatures of alloys, engineers can learn new things about the characteristics that may lead to failures in different applications. Once they detect those issues, they can then re-engineer them. Instead of targeting cancer, they can use imaging and modern techniques to enhance material properties.
“Today, we are very interested in making new materials, but we are forgetting that there is still quite a bit we can do with old materials—we can make important improvements,” he said. “Every material has a unique fingerprint; there’s always a pattern to detect. And if you can find that pattern, understand what limitations there may be in that pattern, you can go back and back-engineer the material in a way so you can make it better and more appropriate for different uses.”
Using this innovative fingerprint approach, Solanki, along with colleagues at the U.S. Army Research Laboratory, Lehigh University, and Louisiana State University, have created a nanocrystalline alloy of copper, tantalum, and lithium called Cu-3-Ta-0.5Li.
The team developed the alloy by looking carefully at copper, identifying patterns at the nanoscale that affect thermal and structural performance. They then used that data to design a new alloy that offers extraordinary thermal stability at 800 °C for over 10,000 hours with little loss of its 1,120-megapascal yield strength. In addition, the new alloy offers remarkable creep resistance compared to conventional copper-tantalum alloys, making it a good fit for high stress, high temperature applications in the aerospace and energy industries.
Solanki said the team started by looking at nickel-based super alloys. These materials are highly sought after in aerospace and defense because of their strength, temperature stability, and corrosion resistance.
Selected for You: Rethinking Classic Heat Transfer Theory
“We’ve been trying to develop nickel-based alloys for 40 years,” he said. “René 44 is a nickel-based super line that was developed after 44 iterations. And each iteration takes time. And to support high-impact technologies, we need to look beyond the materials of 2020. We need to think about new ways of doing things.”
By carefully examining the structure and property relationships across multiple length scales, Solanki and team were able to see how traditional copper-tantalum alloys could be enhanced. When the group added exactly 0.5 percent of lithium to copper lithium precipitates surrounded by a tantalum-rich atomic bilayer, they could see specific changes in the system. The material formed stable cuboidal structures at the nanoscale level which improved the new alloy’s strength and thermal stability.
“When we look at these different patterns, we can make existing alloys a lot better—or design new materials with the properties we want,” he said. “We can also translate this approach to other types of alloys. For example, people have been trying to replace nickel with cobalt in these super alloys. They are having difficulty because they don’t understand the fingerprint aspect of it.”
Frontiers of Advanced Materials: Optimized Recycling in Aluminum Production
“Copper by itself is very soft, the melting temperature is low, and the density is high. It hasn’t been an ideal choice for, say, an aircraft because of that and because it’s very heavy compared to nickel,” he said. “But nanostructuring allows us to open a new paradigm and apply these new materials for applications you wouldn’t normally think of. We can make it thinner, which reduces the mass, so it could be used in places it traditionally could not be.”
When asked what he hopes that other engineers and materials scientists take away from his work, Solanki said his message is simple: Let your curiosity drive you forward.
“We need more curiosity to help us with science,” he said. “We need to go back and figure out what we need to understand, what we need to know, about different materials. When we can identify the limitations of things, see why they fail, and look deeper at that, we can reverse-engineer based on those failures. That will help us develop the technology and tools of the future. That’s how we learn how we could use these old things in a manner that was not possible before.”
Kayt Sukel is a technology and business writer in Houston.
Kiran Solanki, a professor in the School for Engineering of Matter, Transport, and Energy at Arizona State University in Tempe, said that scientists can use a similar approach to optimize materials. By looking for the unique signatures of alloys, engineers can learn new things about the characteristics that may lead to failures in different applications. Once they detect those issues, they can then re-engineer them. Instead of targeting cancer, they can use imaging and modern techniques to enhance material properties.
“Today, we are very interested in making new materials, but we are forgetting that there is still quite a bit we can do with old materials—we can make important improvements,” he said. “Every material has a unique fingerprint; there’s always a pattern to detect. And if you can find that pattern, understand what limitations there may be in that pattern, you can go back and back-engineer the material in a way so you can make it better and more appropriate for different uses.”
Using this innovative fingerprint approach, Solanki, along with colleagues at the U.S. Army Research Laboratory, Lehigh University, and Louisiana State University, have created a nanocrystalline alloy of copper, tantalum, and lithium called Cu-3-Ta-0.5Li.
The team developed the alloy by looking carefully at copper, identifying patterns at the nanoscale that affect thermal and structural performance. They then used that data to design a new alloy that offers extraordinary thermal stability at 800 °C for over 10,000 hours with little loss of its 1,120-megapascal yield strength. In addition, the new alloy offers remarkable creep resistance compared to conventional copper-tantalum alloys, making it a good fit for high stress, high temperature applications in the aerospace and energy industries.
Solanki said the team started by looking at nickel-based super alloys. These materials are highly sought after in aerospace and defense because of their strength, temperature stability, and corrosion resistance.
Selected for You: Rethinking Classic Heat Transfer Theory
“We’ve been trying to develop nickel-based alloys for 40 years,” he said. “René 44 is a nickel-based super line that was developed after 44 iterations. And each iteration takes time. And to support high-impact technologies, we need to look beyond the materials of 2020. We need to think about new ways of doing things.”
By carefully examining the structure and property relationships across multiple length scales, Solanki and team were able to see how traditional copper-tantalum alloys could be enhanced. When the group added exactly 0.5 percent of lithium to copper lithium precipitates surrounded by a tantalum-rich atomic bilayer, they could see specific changes in the system. The material formed stable cuboidal structures at the nanoscale level which improved the new alloy’s strength and thermal stability.
“When we look at these different patterns, we can make existing alloys a lot better—or design new materials with the properties we want,” he said. “We can also translate this approach to other types of alloys. For example, people have been trying to replace nickel with cobalt in these super alloys. They are having difficulty because they don’t understand the fingerprint aspect of it.”
New applications
Solanki added that the new properties of Cu-3-Ta-0.5Li could be used for a variety of different applications—from new coatings to components for systems that require both high strength and heat conduction. For example, Solanki said he could even foresee its use as a thin blade in the lower section of a gas turbine, given its enhanced material properties.Frontiers of Advanced Materials: Optimized Recycling in Aluminum Production
“Copper by itself is very soft, the melting temperature is low, and the density is high. It hasn’t been an ideal choice for, say, an aircraft because of that and because it’s very heavy compared to nickel,” he said. “But nanostructuring allows us to open a new paradigm and apply these new materials for applications you wouldn’t normally think of. We can make it thinner, which reduces the mass, so it could be used in places it traditionally could not be.”
When asked what he hopes that other engineers and materials scientists take away from his work, Solanki said his message is simple: Let your curiosity drive you forward.
“We need more curiosity to help us with science,” he said. “We need to go back and figure out what we need to understand, what we need to know, about different materials. When we can identify the limitations of things, see why they fail, and look deeper at that, we can reverse-engineer based on those failures. That will help us develop the technology and tools of the future. That’s how we learn how we could use these old things in a manner that was not possible before.”
Kayt Sukel is a technology and business writer in Houston.