NASA Joins ‘Astro Anchors’ to Improve Space Flag
NASA Joins ‘Astro Anchors’ to Improve Space Flag
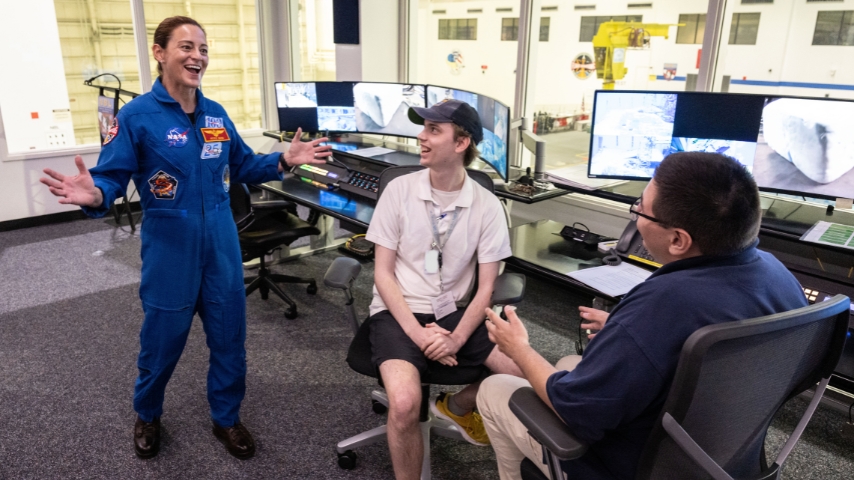
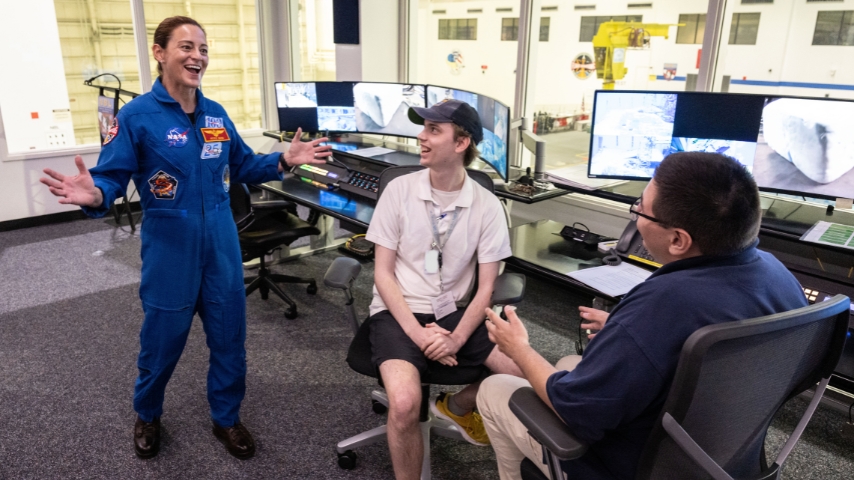
The work and dedication of a student team of engineers has brought them to NASA’s Johnson Space Center to compete for a chance to have their design travel with future astronauts to the Moon.
The ASME student section of Grand Valley State University (GVSU) recently traveled from their school in Allendale, Mich., to Houston for four days of learning, testing, and networking. Sure to inspire the next generation of space explorers, the student team was one of 17 from 13 U.S. colleges and universities that were guests of NASA Johnson Space Center’s Neutral Buoyancy Laboratory (NBL) which houses a massive pool that simulates the weightlessness of space.
This year NASA celebrated the 10th year of its Micro-g Neutral Buoyancy Experiment Design Team (Micro-g NExT) Challenge, one of NASA’s Artemis student competitions. The annual June event tests students’ designs and protypes in a microgravity environment to come up with mission-ready hardware to help NASA explore deep space. The GVSU team were finalists for their flag, flagpole and anchoring system that now has a chance to travel with astronauts to the moon. Out of the four Lunar Flagpoles tested at the lab this year, the GVSU device was the sole protype to pass each and every NASA requirement.
The team calls itself the “Astro Anchors” based on its choice to design a lunar flagpole from four design challenge options. It submitted technical proposals for review in October 2023. The GVSU students learned they were selected in November. Even before traveling to Houston they were introduced to a mentor who was there to support and guide the team as it worked to manufacture prototypes, submit preliminary designs, and complete initial tests. Mentors came from Johnson organizations such as the Flight Operations Directorate, Extravehicular Activity and Human Surface Mobility Program, Engineering, and the Safety and Mission Assurance Directorate.
One major challenge that the team encountered during the prototyping and testing phase included the stability of the entire flagpole system. “While our initial design allowed for easy insertion into the ground, it was not able to withstand the 10 lbs. lateral force required by NASA,” explained section leader Scott Strayer. The engineering students went through numerous iterations until the final design included four spade-shaped structures at the bottom that increased the surface area in contact with the ground.
Another challenge involved the “logistical procedure of deploying the flag,” he said. “Our initial design required the astronaut assemble the horizontal pole that supported the flag at shoulder height.” Think of an inverted L-shape, where the horizontal pole supports the flag and the vertical pole is attached to the anchoring system. “The design would have been an issue since the astronaut’s suit would make it uncomfortable at this height because of the limited mobility they would have,” Strayer said.
Learn More About Student Sections
To resolve the issue, the team decided to come up with a design that allowed the astronaut to unfurl the flag at mid-section height, but given the vertical section had a telescopic mechanism, “the astronaut could easily raise the flag to the required height,” he said. All the poles were assembled using a twist-and-lock coupling mechanism—which Strayer described as “the highlight of the entire assembly.”
“Given that this is a very selective competition, there have been some years where the team has either not been selected or not been able to submit the proposal in time,” Strayer said. He explained that what makes this particular proposal successful is the flagpole’s “simple yet effective design” that is lightweight, modular, and easy to assemble. The entire mechanism was successfully deployed within NASA’s allotted time and also was able to withstand the applied forces. “Additionally, we designed our flagpole to not need any external tools for assembly,” which is a very important feature, he added.
Besides Strayer the team included Caleb Capps, Andrew Latunski, Tasmiya Shaikh, Isabelle Moore, Dayna Straub, Owen Kirkpatrick, Aiden Latchaw, Abigail Way, Cebrina Kader, Simon Morgan, and Rock Phelps. Every year the team tries to enter the challenge and, according to Strayer the team has been selected as finalist multiple times. “It feels amazing to have made it so far with our project this year. Everyone on the team gave it their all, and we are excited to see what next year has in store for us,” he said.
According to the ASME section leader, usually the team tends to be mostly made up of seniors, “but this time, we decided to include several freshmen and sophomore students to give them exposure as well,” Strayer said. The core team consisted of seven students with a total of 12 students who contributed in some capacity throughout the project.
Additionally, the Astro Anchors perform community outreach. The student engineers work collaboratively on the project with Allendale High School (AHS) to promote space research among high school students. For its work with Allendale, the NASA awarded the team its “Pay it Forward” award. This award recognizes their work “conducting meaningful education engagement events in the community and beyond.” Sanjivan Manoharan, an assistant professor of mechanical engineering in the Padnos College Of Engineering at GVSU, was the project’s faculty mentor throughout the process. And major sponsors supporting the project include AavneoTechnologies LLC, GVSU Center for Scholarly Excellence and the GVSU School of Engineering.
Join ASME Student Community Discord
“Our work with the students from Allendale High School is vital to encouraging new engineers and inspiring them to get creative in their work. It allows them to get a first-hand look at what they can accomplish if they work hard and get involved. We hope to convey the unique projects and hands-on work that makes engineering so great,” Strayer explained. “It is amazing as to how we had the opportunity to work on a project and solve a real-world problem for NASA, and we want future students to know that this is possible even at the freshman level.”
Additionally, the ASME section is striving to create a pipeline for those students who may be interested in engineering. “This helps with providing them with the required resources in a timely manner while also creating an opportunity for them to learn more about Grand Valley State University and its engineering program,” he said.
Having been through the process, Strayer’s best advice to develop prototypes, whether it is for personal projects, classes, or extracurriculars, is to start building as soon as possible. “Looking at a CAD model can only reveal so much. During the prototyping of our flagpole, we made much more progress while building and failing than we ever did by staring at 3D models. Even the lowest fidelity prototype can reveal a great deal about the design, both its perks and its flaws,” he said. Another critical component, according to Strayer, is communication. “Throughout, our team had excellent communication. This helped effective delegation of tasks, tracking of action items, and purchasing of materials,” he said.
Strayer admitted that while the project, the NASA visit, and the potential to have their design be part of a future space journey was very rewarding, it did require a great deal of time and effort from the core team. Because of this, Strayer suggests to those who may be interested in such a project, to not join such a team simply to receive recognition or add a covenanted line in a resume. “Treat it as a passion,” he suggested.
This year NASA celebrated the 10th year of its Micro-g Neutral Buoyancy Experiment Design Team (Micro-g NExT) Challenge, one of NASA’s Artemis student competitions. The annual June event tests students’ designs and protypes in a microgravity environment to come up with mission-ready hardware to help NASA explore deep space. The GVSU team were finalists for their flag, flagpole and anchoring system that now has a chance to travel with astronauts to the moon. Out of the four Lunar Flagpoles tested at the lab this year, the GVSU device was the sole protype to pass each and every NASA requirement.
Astro Anchors
The team calls itself the “Astro Anchors” based on its choice to design a lunar flagpole from four design challenge options. It submitted technical proposals for review in October 2023. The GVSU students learned they were selected in November. Even before traveling to Houston they were introduced to a mentor who was there to support and guide the team as it worked to manufacture prototypes, submit preliminary designs, and complete initial tests. Mentors came from Johnson organizations such as the Flight Operations Directorate, Extravehicular Activity and Human Surface Mobility Program, Engineering, and the Safety and Mission Assurance Directorate.One major challenge that the team encountered during the prototyping and testing phase included the stability of the entire flagpole system. “While our initial design allowed for easy insertion into the ground, it was not able to withstand the 10 lbs. lateral force required by NASA,” explained section leader Scott Strayer. The engineering students went through numerous iterations until the final design included four spade-shaped structures at the bottom that increased the surface area in contact with the ground.
Another challenge involved the “logistical procedure of deploying the flag,” he said. “Our initial design required the astronaut assemble the horizontal pole that supported the flag at shoulder height.” Think of an inverted L-shape, where the horizontal pole supports the flag and the vertical pole is attached to the anchoring system. “The design would have been an issue since the astronaut’s suit would make it uncomfortable at this height because of the limited mobility they would have,” Strayer said.
Learn More About Student Sections
To resolve the issue, the team decided to come up with a design that allowed the astronaut to unfurl the flag at mid-section height, but given the vertical section had a telescopic mechanism, “the astronaut could easily raise the flag to the required height,” he said. All the poles were assembled using a twist-and-lock coupling mechanism—which Strayer described as “the highlight of the entire assembly.”
The team
“Given that this is a very selective competition, there have been some years where the team has either not been selected or not been able to submit the proposal in time,” Strayer said. He explained that what makes this particular proposal successful is the flagpole’s “simple yet effective design” that is lightweight, modular, and easy to assemble. The entire mechanism was successfully deployed within NASA’s allotted time and also was able to withstand the applied forces. “Additionally, we designed our flagpole to not need any external tools for assembly,” which is a very important feature, he added.Besides Strayer the team included Caleb Capps, Andrew Latunski, Tasmiya Shaikh, Isabelle Moore, Dayna Straub, Owen Kirkpatrick, Aiden Latchaw, Abigail Way, Cebrina Kader, Simon Morgan, and Rock Phelps. Every year the team tries to enter the challenge and, according to Strayer the team has been selected as finalist multiple times. “It feels amazing to have made it so far with our project this year. Everyone on the team gave it their all, and we are excited to see what next year has in store for us,” he said.
According to the ASME section leader, usually the team tends to be mostly made up of seniors, “but this time, we decided to include several freshmen and sophomore students to give them exposure as well,” Strayer said. The core team consisted of seven students with a total of 12 students who contributed in some capacity throughout the project.
Paying forward
Additionally, the Astro Anchors perform community outreach. The student engineers work collaboratively on the project with Allendale High School (AHS) to promote space research among high school students. For its work with Allendale, the NASA awarded the team its “Pay it Forward” award. This award recognizes their work “conducting meaningful education engagement events in the community and beyond.” Sanjivan Manoharan, an assistant professor of mechanical engineering in the Padnos College Of Engineering at GVSU, was the project’s faculty mentor throughout the process. And major sponsors supporting the project include AavneoTechnologies LLC, GVSU Center for Scholarly Excellence and the GVSU School of Engineering.Join ASME Student Community Discord
“Our work with the students from Allendale High School is vital to encouraging new engineers and inspiring them to get creative in their work. It allows them to get a first-hand look at what they can accomplish if they work hard and get involved. We hope to convey the unique projects and hands-on work that makes engineering so great,” Strayer explained. “It is amazing as to how we had the opportunity to work on a project and solve a real-world problem for NASA, and we want future students to know that this is possible even at the freshman level.”
Additionally, the ASME section is striving to create a pipeline for those students who may be interested in engineering. “This helps with providing them with the required resources in a timely manner while also creating an opportunity for them to learn more about Grand Valley State University and its engineering program,” he said.
Best advice
Having been through the process, Strayer’s best advice to develop prototypes, whether it is for personal projects, classes, or extracurriculars, is to start building as soon as possible. “Looking at a CAD model can only reveal so much. During the prototyping of our flagpole, we made much more progress while building and failing than we ever did by staring at 3D models. Even the lowest fidelity prototype can reveal a great deal about the design, both its perks and its flaws,” he said. Another critical component, according to Strayer, is communication. “Throughout, our team had excellent communication. This helped effective delegation of tasks, tracking of action items, and purchasing of materials,” he said. Strayer admitted that while the project, the NASA visit, and the potential to have their design be part of a future space journey was very rewarding, it did require a great deal of time and effort from the core team. Because of this, Strayer suggests to those who may be interested in such a project, to not join such a team simply to receive recognition or add a covenanted line in a resume. “Treat it as a passion,” he suggested.
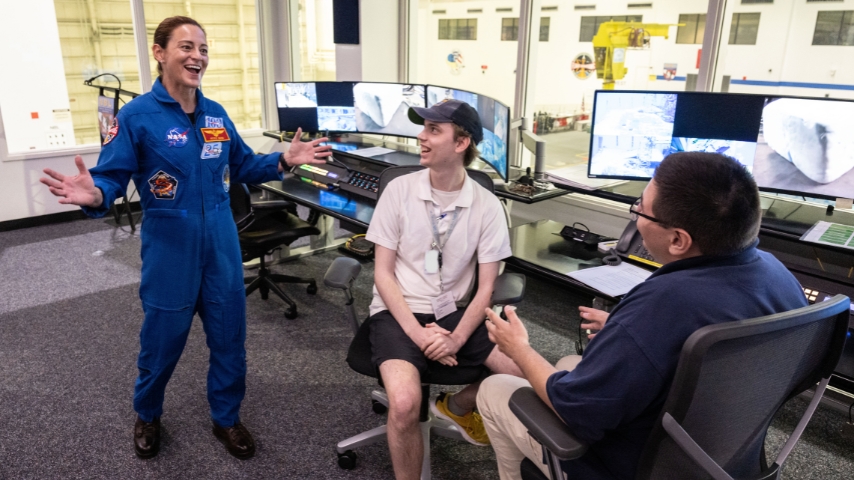
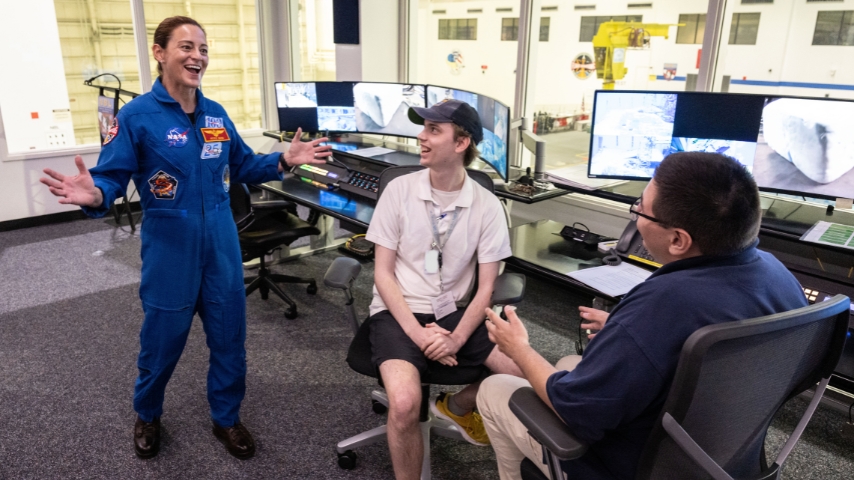