Bricks Make for a Better Heating Element
Bricks Make for a Better Heating Element
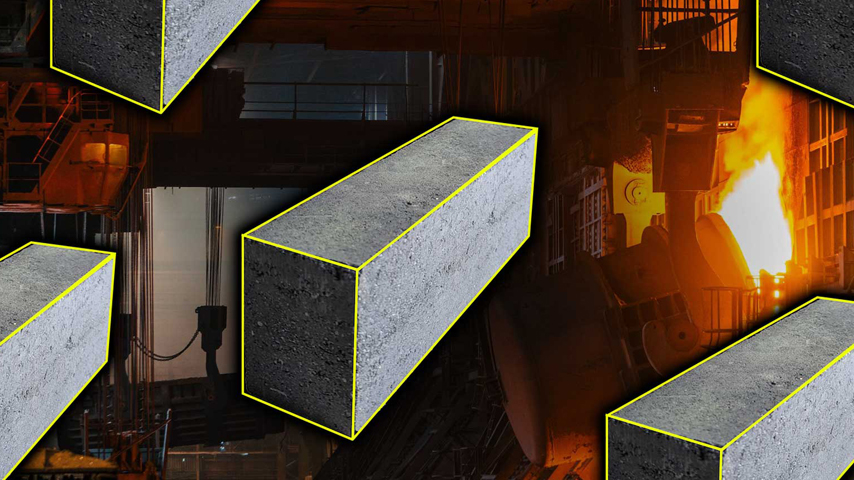
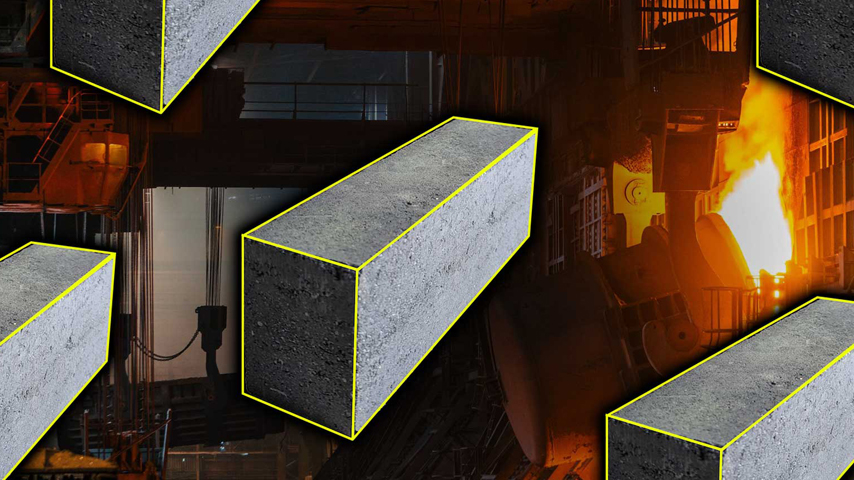
Electrically conductive ceramics can stand up to extremely high temperatures without destructive oxidation. That makes them a viable alternative to tungsten heating elements.
Decarbonization is still on the agenda—if not in the United States, then around the world. While wind and solar power produces electricity cleanly, many industries that require process heat still burn carbon fuels to provide high temperatures. That’s not because electric heaters can reach the several thousand degrees needed by cement kilns or steelmakers, but due to metal heating elements burning out quickly from destructive oxidation.
One promising material for heating elements is firebrick. These inexpensive clay bricks have been used in fireplaces and ovens for thousands of years, and in recent decades, researchers have studied them for energy storage purposes since they can hold thermal energy at very high temperatures for hours or even days at a time. Now, a team of engineers and materials scientists at a company spun out of the Massachusetts Institute of Technology (MIT) have developed a firebrick that is electrically conductive. Not only does that make for more efficient energy storage, but these so-called e-bricks can be used directly as a heating element—without fear of oxidation.
The e-brick emerged as a breakthrough after research revealed that existing electric heating technologies—which rely on materials like Ni-Cr, SiC, and tungsten—were inadequate for large-scale industrial applications. Developed from MIT research dating back to 2014, the e-bricks produced by Electrified Thermal Solutions of Medford, Mass., can reach temperatures up to 1,800 °C (3,275 °F) and retain heat for multiple days, making them a viable alternative to fossil-fuel-based industrial heating.
Daniel Stack, CEO and co-founder of Electrified Thermal Solutions, and MIT nuclear engineering professor Charles Forsberg co-authored a 2017 paper showing firebricks’ potential to store heat from renewable resources. The system they outlined required electric resistance heaters, much like the metal coils in a toaster, to heat the brick. Those metal coils provided an upper limit on the temperatures produced and on the lifetime of the system.
Additional research by Stack and others at Electrified Thermal Solutions led to the development of a modification to the chemical composition of standard firebricks while preserving 98 percent of their original properties. In fact, the formula is similar enough that e-bricks can be manufactured using the existing industrial infrastructure for conventional firebricks.
More thermal storage: Storing Heat from Nuclear Power Plants Could Improve Output
“E-bricks offer several advantages over traditional resistance heaters: they enable higher temperatures, resulting in higher energy density, smaller footprint, and lower cost,” Stack said. In addition to operating at temperatures high enough for use in cement-, glass-, or steelmaking, the chemically inert e-bricks won’t fail when exposed to those high temperatures for long periods.
“Additionally, their higher electrical resistance requires higher operating voltages,” Stack said, “reducing balance-of-plant costs by minimizing the need for electrical transformers, making them more cost-effective compared to other heating approaches.”
The company said its e-bricks not only offer decades-long durability, but also can be cost-effectively mass produced using established manufacturing methods. Their chrome-alumina composition allows seamless integration into industrial furnaces, whether as a thermal battery or a high-efficiency heating wall.
Stack said the high-temperature technology creates a couple disruptive shifts. In the industrial sector, electrifying industrial heating using clean grid power or onsite renewables becomes less expensive than burning fossil fuels. For the power grid, industrial heat demand can now flexibly align with intermittent renewable generation, reducing the need for expensive peaking power plants while increasing the grid’s capacity to absorb renewable energy. Instead of storing over-produced electricity in batteries for later delivery to the grid—and accepting the sometimes-high conversion losses—industrial users could capitalize on e-brick systems by heating their furnaces with low- or zero-cost electricity with almost perfect efficiency.
“The high-temperature capability of e-bricks bridges a critical gap in industrial decarbonization by enabling electrification of processes that previously had no economically viable alternative to fossil fuels,” Stack said. “This makes the system suitable for even the most demanding high-temperature industries, including cement, steel, and chemical manufacturing.”
Jim Romeo is a technology writer in Chesapeake, Va.
One promising material for heating elements is firebrick. These inexpensive clay bricks have been used in fireplaces and ovens for thousands of years, and in recent decades, researchers have studied them for energy storage purposes since they can hold thermal energy at very high temperatures for hours or even days at a time. Now, a team of engineers and materials scientists at a company spun out of the Massachusetts Institute of Technology (MIT) have developed a firebrick that is electrically conductive. Not only does that make for more efficient energy storage, but these so-called e-bricks can be used directly as a heating element—without fear of oxidation.
The e-brick emerged as a breakthrough after research revealed that existing electric heating technologies—which rely on materials like Ni-Cr, SiC, and tungsten—were inadequate for large-scale industrial applications. Developed from MIT research dating back to 2014, the e-bricks produced by Electrified Thermal Solutions of Medford, Mass., can reach temperatures up to 1,800 °C (3,275 °F) and retain heat for multiple days, making them a viable alternative to fossil-fuel-based industrial heating.
Daniel Stack, CEO and co-founder of Electrified Thermal Solutions, and MIT nuclear engineering professor Charles Forsberg co-authored a 2017 paper showing firebricks’ potential to store heat from renewable resources. The system they outlined required electric resistance heaters, much like the metal coils in a toaster, to heat the brick. Those metal coils provided an upper limit on the temperatures produced and on the lifetime of the system.
Additional research by Stack and others at Electrified Thermal Solutions led to the development of a modification to the chemical composition of standard firebricks while preserving 98 percent of their original properties. In fact, the formula is similar enough that e-bricks can be manufactured using the existing industrial infrastructure for conventional firebricks.
More thermal storage: Storing Heat from Nuclear Power Plants Could Improve Output
“E-bricks offer several advantages over traditional resistance heaters: they enable higher temperatures, resulting in higher energy density, smaller footprint, and lower cost,” Stack said. In addition to operating at temperatures high enough for use in cement-, glass-, or steelmaking, the chemically inert e-bricks won’t fail when exposed to those high temperatures for long periods.
“Additionally, their higher electrical resistance requires higher operating voltages,” Stack said, “reducing balance-of-plant costs by minimizing the need for electrical transformers, making them more cost-effective compared to other heating approaches.”
The company said its e-bricks not only offer decades-long durability, but also can be cost-effectively mass produced using established manufacturing methods. Their chrome-alumina composition allows seamless integration into industrial furnaces, whether as a thermal battery or a high-efficiency heating wall.
Stack said the high-temperature technology creates a couple disruptive shifts. In the industrial sector, electrifying industrial heating using clean grid power or onsite renewables becomes less expensive than burning fossil fuels. For the power grid, industrial heat demand can now flexibly align with intermittent renewable generation, reducing the need for expensive peaking power plants while increasing the grid’s capacity to absorb renewable energy. Instead of storing over-produced electricity in batteries for later delivery to the grid—and accepting the sometimes-high conversion losses—industrial users could capitalize on e-brick systems by heating their furnaces with low- or zero-cost electricity with almost perfect efficiency.
“The high-temperature capability of e-bricks bridges a critical gap in industrial decarbonization by enabling electrification of processes that previously had no economically viable alternative to fossil fuels,” Stack said. “This makes the system suitable for even the most demanding high-temperature industries, including cement, steel, and chemical manufacturing.”
Jim Romeo is a technology writer in Chesapeake, Va.