Reverse Electrolysis Controls Underwater Robot’s Buoyancy
Reverse Electrolysis Controls Underwater Robot’s Buoyancy
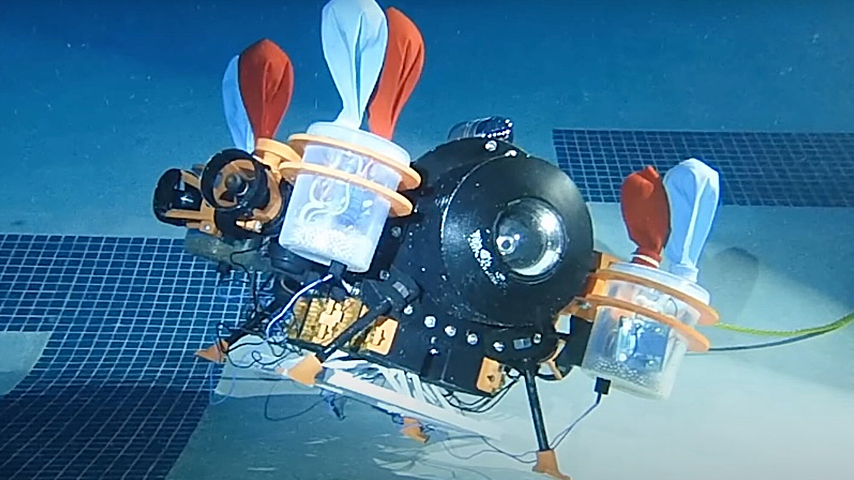
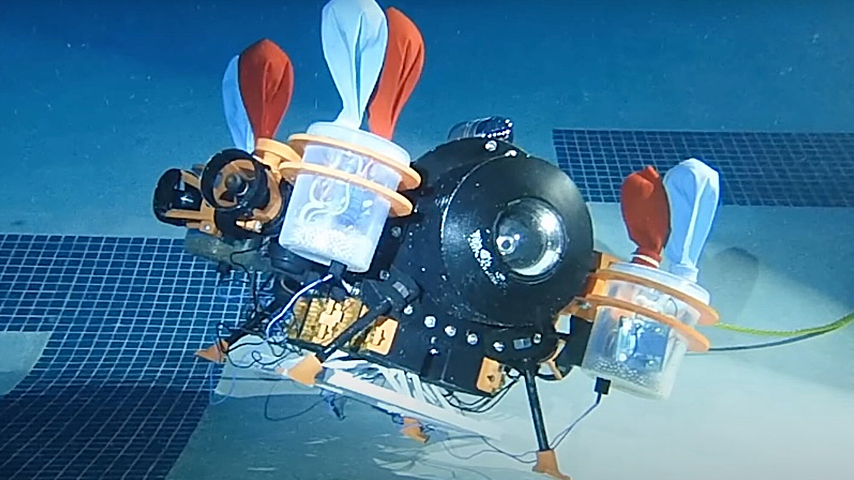
To optimize autonomous underwater vehicles, researchers have developed a buoyancy control device that uses reverse electrolysis to alter a vehicle's overall volume.
Autonomous underwater vehicles (AUVs) are ideal for unmanned missions to the deep sea, military operations, and marine research. However, these vehicles face a number of challenges when it comes to their weight, energy efficiency, locomotion, and communications. Researchers are working to optimize AUVs so they can do more, and a group of students at Rice University is helping to solve a couple of critical components.
As part of their senior capstone project, the Bay-Max team developed a buoyancy control device (BCD) using reversible fuel cells that create oxygen and hydrogen gas from water—a process called reverse electrolysis—which generates energy that the device uses to inflate a series of balloons that change the AUV’s overall volume.
The team’s findings are detailed in “Energy Efficient Depth Control for Underwater Devices Using Soft and Hard Actuators,” published recently by the Institute of Electrical and Electronics Engineers.
“With this new technology, we are creating buoyancy forces,” said Fathi Ghorbel, a professor of mechanical engineering and bioengineering at Rice, sponsor for the student team, and co-author on the study. “So, in the same way we create thrust forces with a regular thruster, we are creating buoyancy forces by changing the density and the volume.”
Reverse electrolysis has gained considerable appeal in the electric vehicle industry, but this is the first time it has been utilized in an AUV. To kickstart this chemical process within the device, voltage is applied, which ionizes the water into gas that inflates the balloons, increasing the buoyancy. The voltage is reversed to deflate the balloons and plunge the device to lower depths. This device works in tandem with traditional thrusters to save energy, which allows the AUV to stay neutrally buoyant—unlike conventional vehicles.
Discover the Benefits of ASME Membership
Ghorbel explains that by using this method, the thrust component becomes almost entirely energy-free, reducing energy consumption by 85 percent compared to traditional vehicles. As such, it is also quieter, making it ideal for military operations or environmental monitoring, where noise can disturb the mission.
The students faced a few challenges along the way, particularly with sealing the robot properly. Any leak would pose a risk to the internal electronics, but also shift the mass properties and make it much harder to achieve the points of control that they wanted to.
The team—Andrew Bare, Spencer Darwall, Noah Elzner, Rafe Neathery, Ethan Peck, and Dan Zislis—relied on each other to navigate these challenges, and they had an advantage from the start. Before entering this project, the team worked together in Rice’s rocketry club. So, they already knew how to break down bigger challenges.
“We divided up the work so that everyone owned one aspect of it,” explained Bare. “One member worked on the control hardware, another on the interface, and it helped us work better because we all knew what areas our contributions were in. It took persistence to work through issues, but we chipped away at it and reached our goal.”
This project is one of the many examples of how today’s undergraduate engineering students are learning valuable skills about technology and teamwork and implementing those skills in real-life projects.
More for You: Autonomous Sub for Icy Great Lakes
“We developed the first working prototype of a practical application that uses BCD technologies,” Zislis said. “It was astonishing to get the device inside an Olympic-sized pool, run tests, and get footage of it. It was an opportunity to show our school that this is possible, and there's more to develop from here.”
As with many senior projects, the work does not end at this stage. In the fall, Ghorbel hopes to work with his students to further advance the technology. He says they intend to make an amphibious robot inspired by a mudskipper that can jump and walk on land. Every year is about getting one step closer to a completed design.
As for this year’s seniors, they are off to the next stage in their careers. Zislis will be continuing on at Rice as a teaching assistant while he completes his master's degree. He hopes to work with the next group of seniors on their capstone projects. Bare will be entering the field to focus his efforts on hardware design.
“It was really nice for me to be able to learn these skills,” Bare said. “Skills that I can use in the real world.”
Cassandra Kelly is a technology writer in Columbus, Ohio.
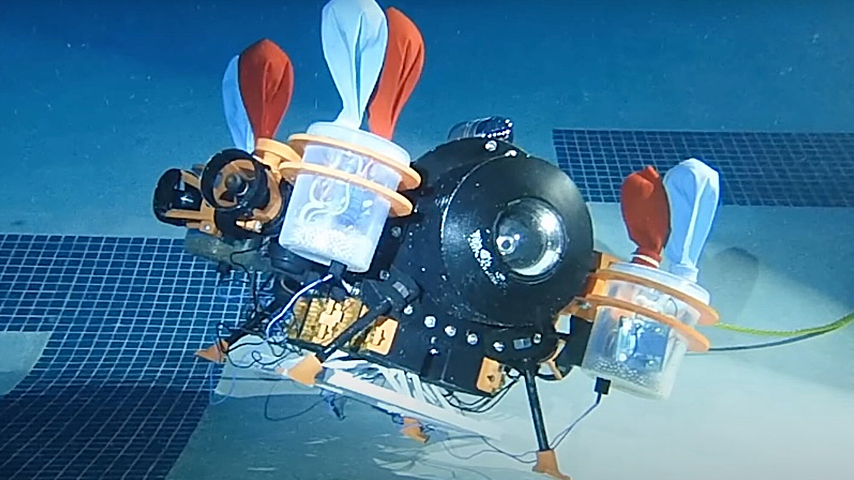
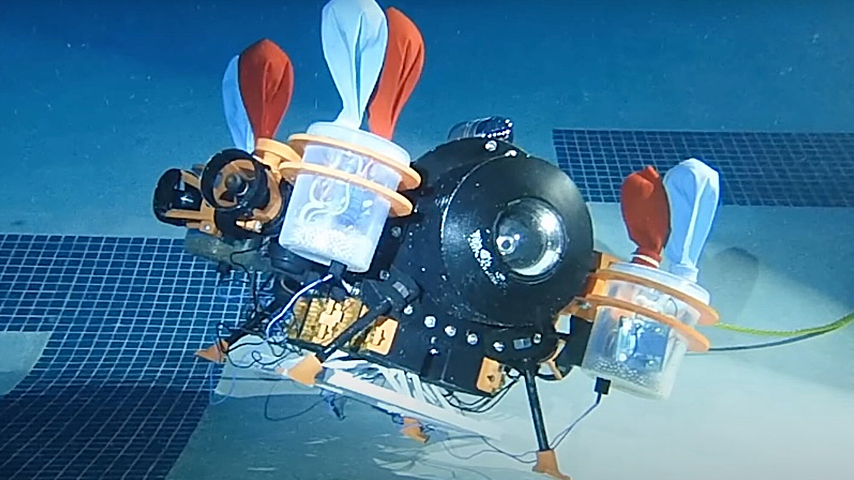