There’s a Twist to Improving Soft Robots
There’s a Twist to Improving Soft Robots
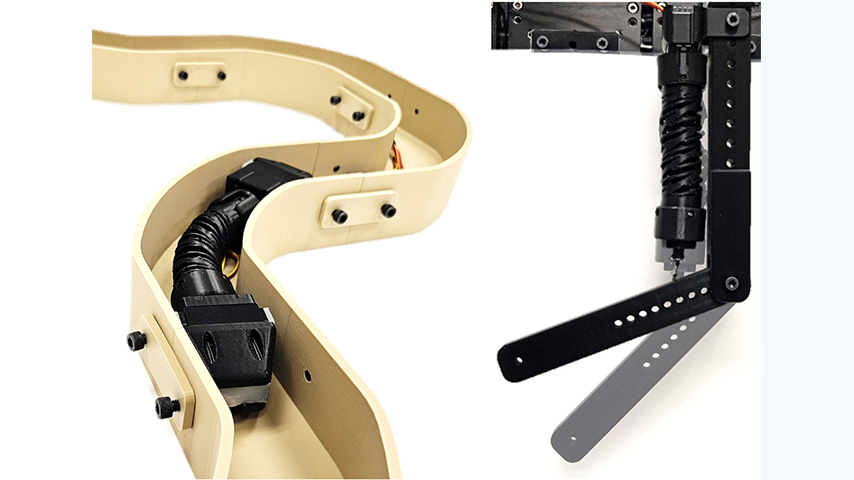
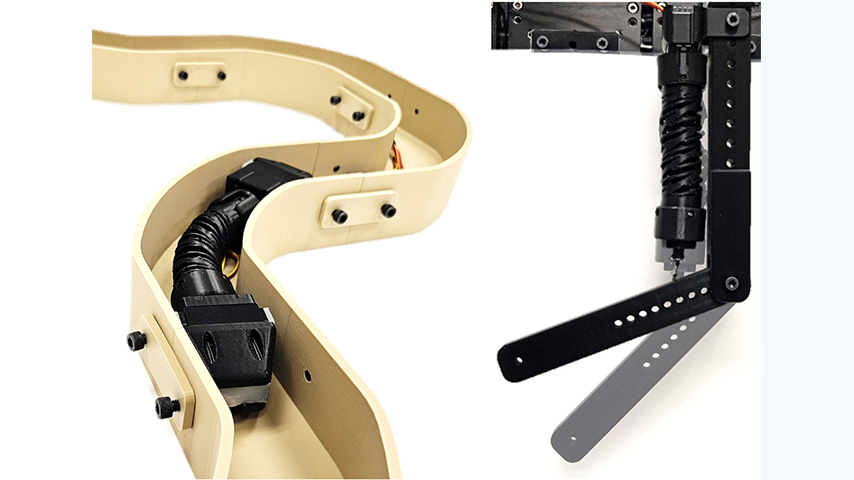
Attach an auxetic structure—that expands when pulled on—to a servo motor and you’ve got a more useful hardy soft robot.
Soft robots are safer, more robust, and can go places that no Roombas or Terminators could wind themselves into. In an effort to create cushier deformable bots inspired by living creatures, roboticists have created many potential materials that can be activated to move in various ways. But soft robotics continues to have one big problem: the very “softness” of these materials makes them hard to control.
“One of the biggest challenges in soft robotics is actuation,” said Ryan Truby, an assistant professor of materials science and mechanical engineering at the Northwestern University’s McCormick School of Engineering. “Typically, you’re relying on pressures or vacuums, you’re relying on heat or light, you’re relying on unwieldy stimuli to drive shape change in soft robotic materials.”
To make a soft robot more controllable—and more useful—Truby, with postdoctoral scholar Taekyoung Kim, turned to a class of soft kirigami-ish mechanical metamaterial structures called handed shearing auxetics, or HSAs.
The word “auxetic” is key to what makes them special. Unlike almost everything else in nature, when pulled at the ends auxetic materials widen rather than get thinner. It’s the pattern of cuts or spaces in HSAs that give them this seemingly paradoxical property. In essence, they open up when pulled on, and Truby and Kim used this auxetic behavior to drive better soft robotic actuation the old-fashioned way: with servo motors.
“If we apply torque to one end of the HSA structure while constraining the other end, it can make an extension motion,” Kim said. But just how to effectively transmit torque and constrain one end with a compact structure was crucial—the “transmitter” had to be both resistant to twisting and extendable. The solution, he found, was a bellows-like shaft that would deliver the torque from one end to the other, allowing the HSA to extend and contract.
Discover the Benefits of ASME Membership
But this ingenious architecture was only one of the goals of the project. “The only limitation keeping us from using HSAs more universally is the materials we construct them from—previously it was very brittle,” Kim said. He set out to find a way to print the HSAs with common 3D printers. He managed to do that with thermoplastic polyurethane, a typical rubbery filament used with 3D printers. As a result, the HSAs that make this new soft robotic actuator possible cost just dollars to produce.
The low cost is just a side benefit. “What this has done is change how we can think about building practical soft robots,” Truby said. “It used to take me 80 hours to build some of our robots, and they would only last for about four, if we were lucky. Now we’ve been running hours and hours of experiments and the motor fails before the printed HSAs do. To have that robustness and durability is a game changer for bringing high-performance, autonomous capabilities to soft robotics.”
More on This Topic: A Leap Forward in Soft Robotics
Kim built several robots with their new actuators. One looks something like a short snake with a head at each end. And it can handedly snake its way through a mock-up tunnel, bending along as its center expands and contracts like a convoluted slinky. It has arguably already proven its worth for all kinds of applications—search-and rescue-bot and pipe inspector among them. They also demonstrated the actuator as an artificial muscle in a simple manipulator.
But Truby and Kim have some advancements in mind.
“Trying to make new locomotion capabilities for walking is one of our biggest things right now,” Truby said. “The fundamentals of getting locomoting robots with soft appendages is now within reach.” They are also looking at other materials and thinking of ways to include sensors within them.
Then finally all the applications that require a tool that is squishable, pliable, and easily movable, will have their robot.
Michael Abrams is a technology writer in Westfield, N.J.
“One of the biggest challenges in soft robotics is actuation,” said Ryan Truby, an assistant professor of materials science and mechanical engineering at the Northwestern University’s McCormick School of Engineering. “Typically, you’re relying on pressures or vacuums, you’re relying on heat or light, you’re relying on unwieldy stimuli to drive shape change in soft robotic materials.”
To make a soft robot more controllable—and more useful—Truby, with postdoctoral scholar Taekyoung Kim, turned to a class of soft kirigami-ish mechanical metamaterial structures called handed shearing auxetics, or HSAs.
The word “auxetic” is key to what makes them special. Unlike almost everything else in nature, when pulled at the ends auxetic materials widen rather than get thinner. It’s the pattern of cuts or spaces in HSAs that give them this seemingly paradoxical property. In essence, they open up when pulled on, and Truby and Kim used this auxetic behavior to drive better soft robotic actuation the old-fashioned way: with servo motors.
“If we apply torque to one end of the HSA structure while constraining the other end, it can make an extension motion,” Kim said. But just how to effectively transmit torque and constrain one end with a compact structure was crucial—the “transmitter” had to be both resistant to twisting and extendable. The solution, he found, was a bellows-like shaft that would deliver the torque from one end to the other, allowing the HSA to extend and contract.
Discover the Benefits of ASME Membership
But this ingenious architecture was only one of the goals of the project. “The only limitation keeping us from using HSAs more universally is the materials we construct them from—previously it was very brittle,” Kim said. He set out to find a way to print the HSAs with common 3D printers. He managed to do that with thermoplastic polyurethane, a typical rubbery filament used with 3D printers. As a result, the HSAs that make this new soft robotic actuator possible cost just dollars to produce.
The low cost is just a side benefit. “What this has done is change how we can think about building practical soft robots,” Truby said. “It used to take me 80 hours to build some of our robots, and they would only last for about four, if we were lucky. Now we’ve been running hours and hours of experiments and the motor fails before the printed HSAs do. To have that robustness and durability is a game changer for bringing high-performance, autonomous capabilities to soft robotics.”
More on This Topic: A Leap Forward in Soft Robotics
Kim built several robots with their new actuators. One looks something like a short snake with a head at each end. And it can handedly snake its way through a mock-up tunnel, bending along as its center expands and contracts like a convoluted slinky. It has arguably already proven its worth for all kinds of applications—search-and rescue-bot and pipe inspector among them. They also demonstrated the actuator as an artificial muscle in a simple manipulator.
But Truby and Kim have some advancements in mind.
“Trying to make new locomotion capabilities for walking is one of our biggest things right now,” Truby said. “The fundamentals of getting locomoting robots with soft appendages is now within reach.” They are also looking at other materials and thinking of ways to include sensors within them.
Then finally all the applications that require a tool that is squishable, pliable, and easily movable, will have their robot.
Michael Abrams is a technology writer in Westfield, N.J.
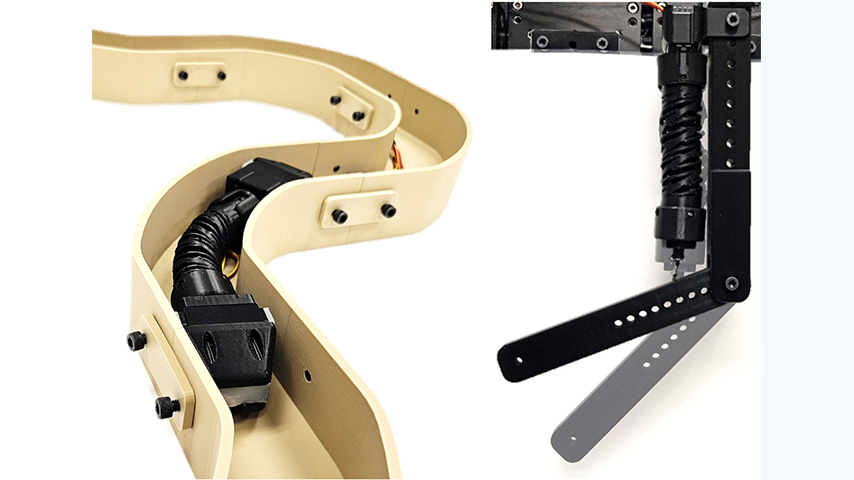
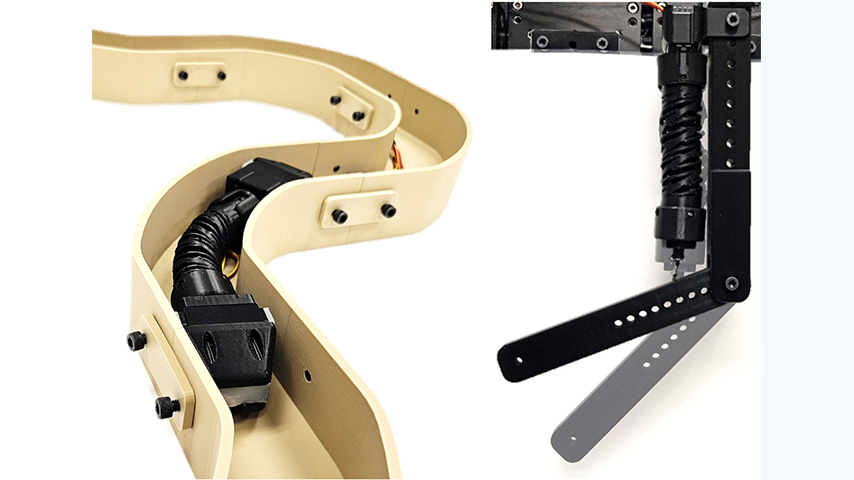