A Stage for the Ages at Radio City
A Stage for the Ages at Radio City
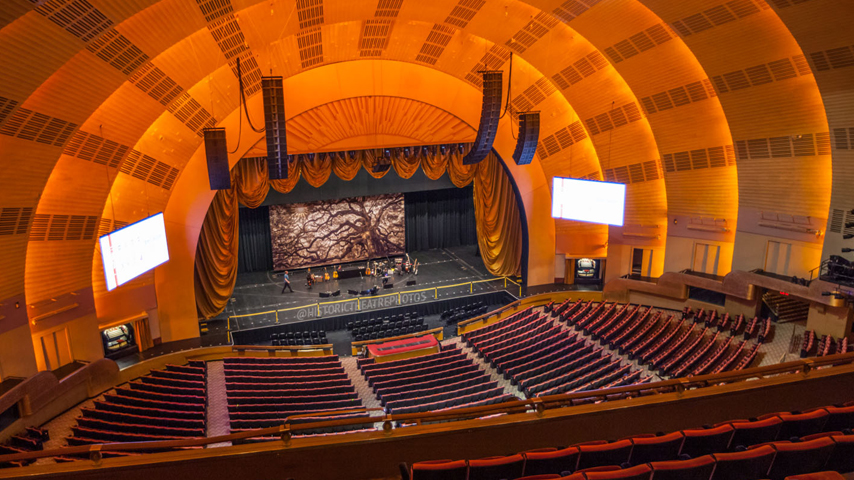
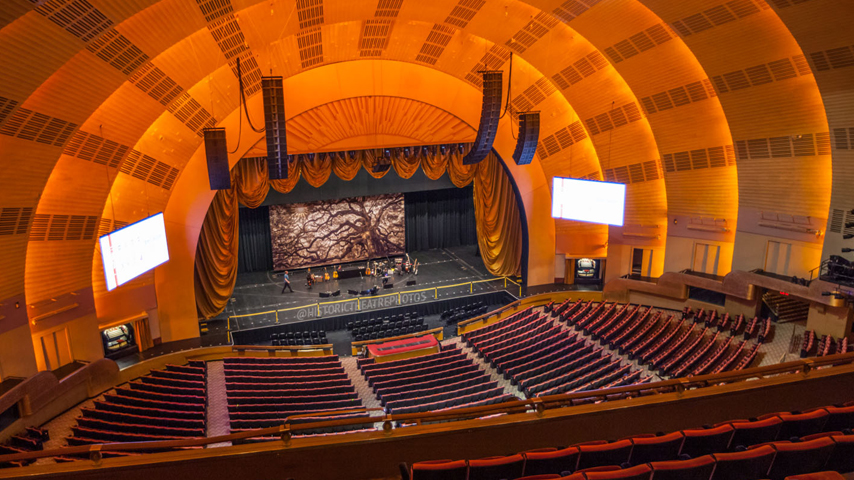
First built in 1932, Radio City Music Hall's hydraulically actuated stage remains an engineering marvel.
Every year in early November, The Christmas Spectacular at Radio City Music Hall officially kicks off the holiday season. Although the Rockettes, creatures, and Santa are of course draws, the show is made even more spectacular by the venue’s unique moving stage that has withstood both time and wear despite heavy use year after year.
When Radio City first opened in 1932, the venue itself outshined the shows, or so contemporary reports recall. Nearly 100 years later, it remains the largest indoor theater in the world, with an auditorium seating nearly 6,000 stretching back 160 feet from the stage and an 84-foot-tall ceiling.
Central to the hall’s wonder is the hydraulically actuated stage, which ASME recognized in 2001 as a mechanical engineering landmark for its historic and societal significance. Seated below a 60-foot-tall proscenium arch, the 100-foot-wide stage features four hydraulic elevators.
"They were engineered and installed by a rigging company called Peter Clark,” said Joe Mobilia, principal, Stage Rigging & Technology Design at Fisher Dachs Associates (FDA). “For pretty much any theater in New York City and around the country during that period—chances are Peter Clark was the rigging contractor.”
The orchestra pit lift is closest to the audience, while there are three lifts on the stage itself. A 43-foot-diameter turntable that rotates on motor-driven rollers in both directions is incorporated into the stage lifts as well. Combined, these four elevators weigh about 380,000 pounds.
You Might Also Enjoy: Mount Wilson’s Telescopes Expanded Understanding of the Universe
“The system is unique in the theater industry in that Peter Clark designed it to provide both the ability to select a variable position—in other words, rather than having hard stops like a regular elevator, you had the ability to select a position using these switches and push buttons—and also it had direct readout from selsyns,” explained R. Duncan MacKenzie, an industrial designer who recently retired after 50 years in the industry, most recently serving as a principal with Proskenion Design, LLC. “There had been no variable speed elevators for the stage at this point. And this was done with some very interesting valves that were built by the Crane Company for Peter Clark. The cylinders and those assemblies were built by the Otis Company out in Long Island.”
The first and third lifts are 70 feet by 16 feet, while the center lift is 70 feet by 12 feet and contains machinery that drives the turntable. Operator controls for the system are located off stage right. As for the orchestra lift, it can move horizontally or vertically along an elevator shaft, allowing it to move from the sub-basement level or to the back of the stage.
Underneath the stage is a sea of pipes and valves. Equalizer tubes span the stage and the pressure piping from the valve system runs across to the lift bases. Each lift features two pistons and cylinders that move the stage segments from -27 feet beneath the stage up to 13 feet above.
“They have a speed of—now, I limited it to about 45 feet a minute—but when you're standing on it and it takes off, it's a bit of a rush,” added MacKenzie, who designed the stage’s updated controls system.
Each elevator is equipped with automatic pre-set stops or manually operated push-button stations, originally set from a bronze control panel with multiple dials and sliders, which is somewhat reminiscent of steampunk technology at first glance.
“They do around 220 performances of the Christmas show over the course of a couple of months. At peak holiday season on the weekend, they'll do six shows over the course of the day. That machinery absolutely had to work every time, and if they had any kind of a major mechanical failure, it would either cancel the show or drastically change it,” Mobilia said. “It worked in 1932 and it still works in 2024.”
It's Time to Renew Your ASME Membership
The hydraulic system uses synchronizing gears to automatically equalize the plungers, while specially treated water (not oil, as many often assume) moves through the piping at a pressure of 400 pounds per square inch. A 20,000-gallon pressure tank allows the system to lift or lower the 190 tons of stage, plus another 96,000 pounds, with the help of two 275-horsepower pumps.
“Off stage right is where the pump room is. There's air pressure on top of the water that gives the initial thrust to the system,” MacKenzie explained. “A torque tube for each of the lifts runs across the stage and off stage is a gear rack that engages a spur gear where there are clutches that couple these so that they remain synchronized if they’re working together or can run independently.”
There have been two major renovations at Radio City, one in the 1970s that was mostly cosmetic, then in 1999, an eight-month effort overhauled parts of the hydraulic system and its controls.
The lift system’s original control valves were made of cast iron, but they were starting to leak, as water was causing the valves to deteriorate from the inside. These valves were replaced with air-actuated and positioned ball valves—commonly used in process controls—to better control water flowing through the pump system into the lifts.
But other than that, the rest of the system remains largely intact. “Except for the controls and the pneumatically operated positioning valves, it’s all the original pipe work. It’s all the original torque tubes. It’s all the original cylinders,” MacKenzie said.
If it wasn’t for the need to replace the valves, the system probably could have remained operating in the same way as 1932, said Mobilia, whose firm FDA was a consultant on the 1999 renovation.
MacKenzie had prepared a design proposal for Radio City management back in 1994 for this very task, so using that as a starting point, his company Proskenion Design, working for J.R. Clancy, Inc., “prepared a new programmable controller-based control system design to be coupled with the older control system,” he said. “In fall 1999, I did the on-site commissioning and programming of the system.”
Another ASME Landmark: Ingenuity Turned the Geysers into a Powerhouse
As part of the update, the solenoid operated valves were replaced with a speed selsyn that could change the cavity of the valve to pneumatically operated with positioning devices, which receive a 4-20 milliamp signal from the control system and then open or close the deep port ball valve to control the speed, he explained.
Along with these two control systems, the update added the “ability for not only upstairs to control the system, but downstairs as a backup control,” MacKenzie said. “We also put in a manual back up and then a manual, manual backup, so that they wouldn't lose a show.”
In 2018, Radio City management returned to MacKenzie, asking him to do another update to the system for both operational needs and because the manufacturer was discontinuing support for the programmable controller system installed in 1999. This update was completed in January 2019 and included the addition of a system that notifies building management if there are any faults.
Radio City’s stage elevators were truly state-of-the-art when they were developed. After the venue’s opening in 1932, The New York Times called it the “greatest achievement of the theatrical world.” The system also inspired the U.S. Navy, which integrated an identical hydraulic system in its World War II-era aircraft carriers. In fact, the U.S. government considered the system so important that agents were stationed around the area to ensure no one could steal the technology during that time.
Today, the stage continues to see regular use, with the original systems still performing as intended.
“We didn't functionally really change much of anything. We just made it much simpler for the operators to use the system,” MacKenzie said. “In the Christmas show now, they've got over 80 or 85 cues in the space of an hour or so, and it is a lot of moves.”
Louise Poirier is senior editor.
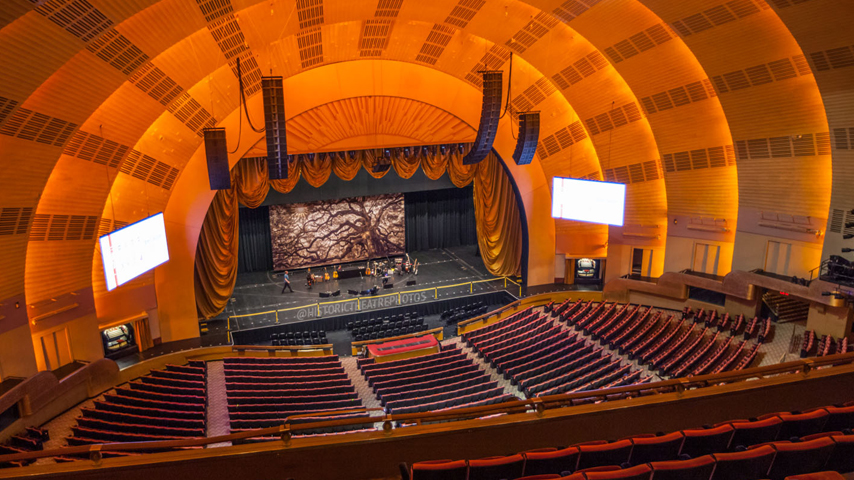
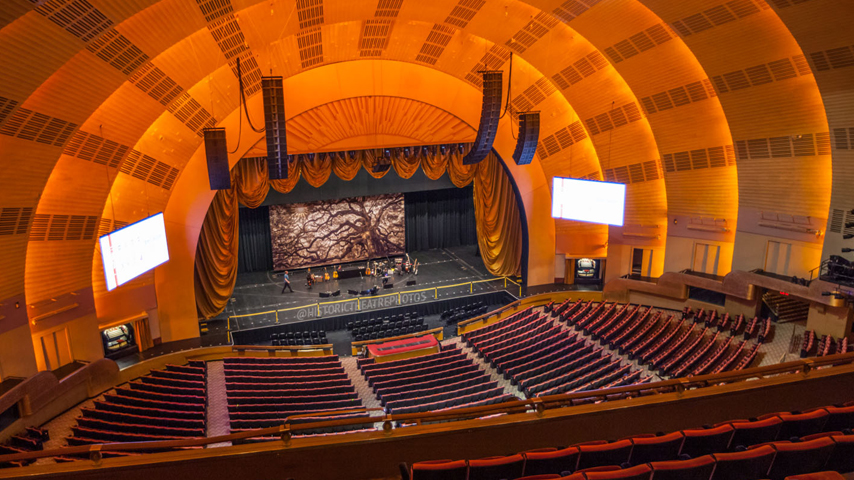