New Process Embeds Coded Data on 3D-Printed Parts
New Process Embeds Coded Data on 3D-Printed Parts
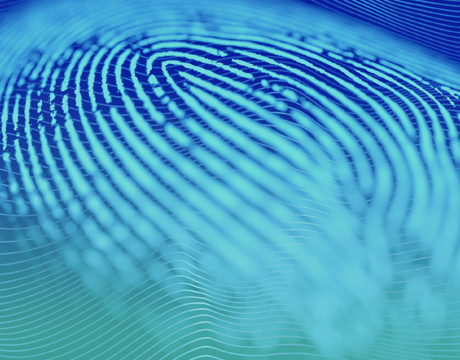
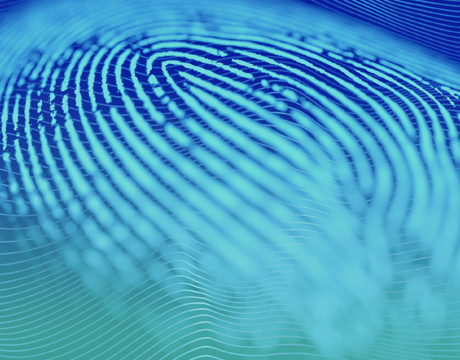
Manufacturers are always looking for ways to reduce costs and stay compliant. This includes securing the chain of custody of parts and products they make and reducing counterfeit products. This is especially true for 3D-printed parts, for which realistic “knock-offs” are easily made. For medical devices, this is where unique device identification (UDI) is particularly important.
Printing UDI codes or QR codes on a part or product typically requires an extra step, after the part or product has been manufactured. This slows down the production process and adds extra time and cost.
Now, Rize, a Boston, U.S.-based, next-generation additive manufacturing company, has developed a method that embeds identifying information on a product during the 3D-manufacturing process. What’s more, it goes beyond simple identification for tracking to include codes that are loaded with all the relevant design and engineering data for that part.
“We have now created a digital thread that connects the design/model with the final physical part,” says Julie Reece, vice president of marketing for Rize. “This capability will accelerate Industry 4.0 technologies like blockchain and augmented reality/virtual reality applications, improving compliance, authenticity, and traceability.”
For You: 4D Printing Advances Additive Manufacturing
Rize utilizes its augmented polymer deposition (APD) technology—a combination of fused deposition modeling (FDM) and piezo jetting into a single printer—to print end-use parts. A proprietary medical-and-engineering-grade thermoplastic compound is simultaneously extruded with the jetting of functional inks, at the voxel (3D pixel) scale, to vary material properties of the thermoplastic during deposition, creating new design possibilities for engineers. Voxel-level control provides the resolution needed to embed complex QR codes on products, including transferring design, assembly, and performance specification data into the part, creating what Rize calls “digitally augmented parts.” This re-establishes the link between the finished product and the XML-based 3MF file. “A common smartphone app can scan the QR code on the part and instantly display the corresponding digital information online,” Reece says. “For example, an engineer can store all of a part’s information digitally and maintain digital augmentation of the part throughout its lifecycle.” This will provide all the data an assembly technician or machinist needs to properly install or troubleshoot the part.
The QR or bar code is imported into the slicer, sized, and placed on the part. The part is then sent to the printer where it is constructed, layer by layer. As the part is being built, the marking ink needed for the QR code is distributed at the voxel level to produce the QR code. As soon as the part is complete, the QR code can be scanned with a smartphone to instantly bring up the digital information.
“This process builds trust into the part,” Reece says. “The ink cannot be rubbed or worn off. It is secure, so this capability creates an immutable digital connection between the physical part and its digital twin for traceability and compliance. If a very minor change has been made to the design that cannot be discerned visually, you just scan the part with your smartphone and see all the data related to design changes.” "Our process for the development of new products generally requires numerous iterations to get the part features just right," says David Perron, group manager at CONMED, a medical device manufacturer, in a recent article on Newequipment.com. "The changes are not always obvious, particularly when we're looking at dozens of iterations. The QR code will help us easily identify iterations and show the flow of the design thought process." For the first time, 3D printing can support blockchain technologies and ensure that intellectual property capture is completely secure and tamper-proof. Embedded QR codes will also streamline and speed up product design.
“When two engineers are working on different components, for example, such as a front and back end, they might not be working at the same pace,” Reece says. “Because the digital thread remains in the QR code, the engineer ready to print can do so, put on smart glasses that read the QR code that will overlay the side that only exits digitally to render the complete assembly. This lets the team know if the designs match and will fit together, and any errors can be caught early.”
The digitally augmented parts also allow a design team to quickly switch from physical to virtual reality. The QR code can directly link to the CAD file so the designer can virtually manipulate the digital twin, if needed. This streamlines the process and ensures the 3D model being changed is the right version, since each new version is assigned its own unique code. The Rize process is also an effective way to remove any products from the market that are non-compliant due to design changes, piracy, counterfeiting, or obsolescence—all of which damage the customer experience and result in rework, recalls, and loss of brand value.
Mark Crawford is an independent writer.
Read More:
Print’s Indelible Mark
Ultrasound Patch Monitors Critical Components
3D Printing a Future of New Metal Actuators
This process builds trust into the part. The ink cannot be rubbed or worn off.Julie Reece, VP of Marketing, Rize
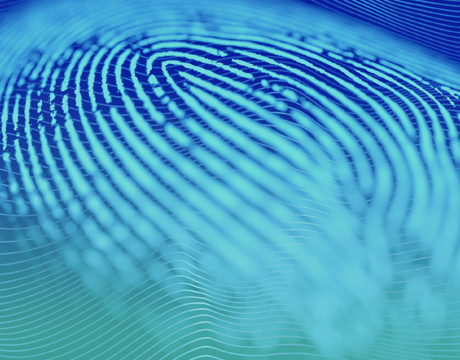
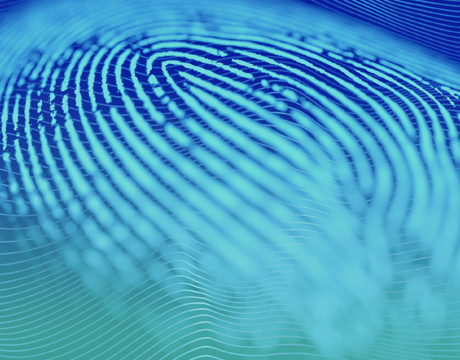