Researchers Spin Up an Invisible, Unbreakable Mechanical Cloak
Researchers Spin Up an Invisible, Unbreakable Mechanical Cloak
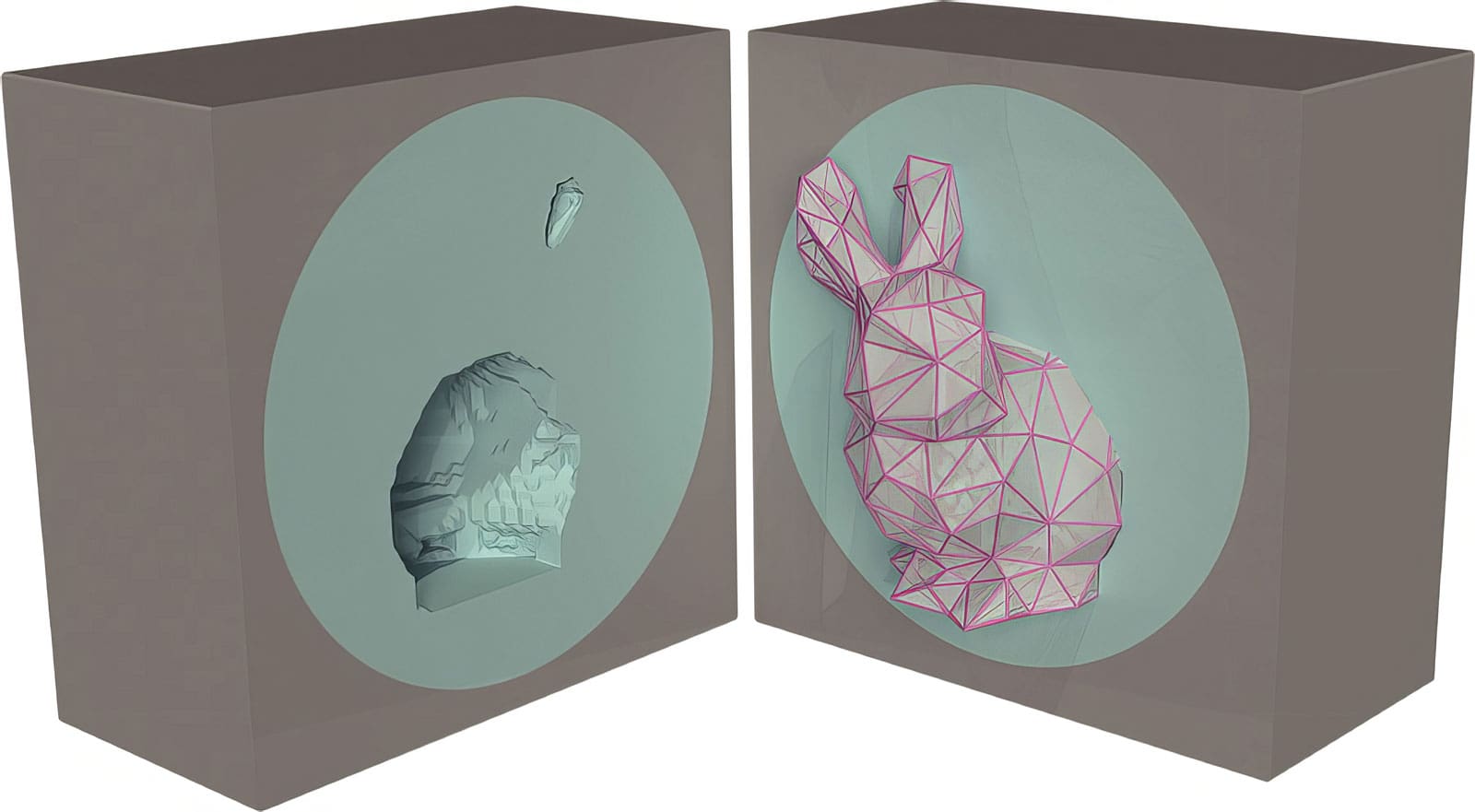
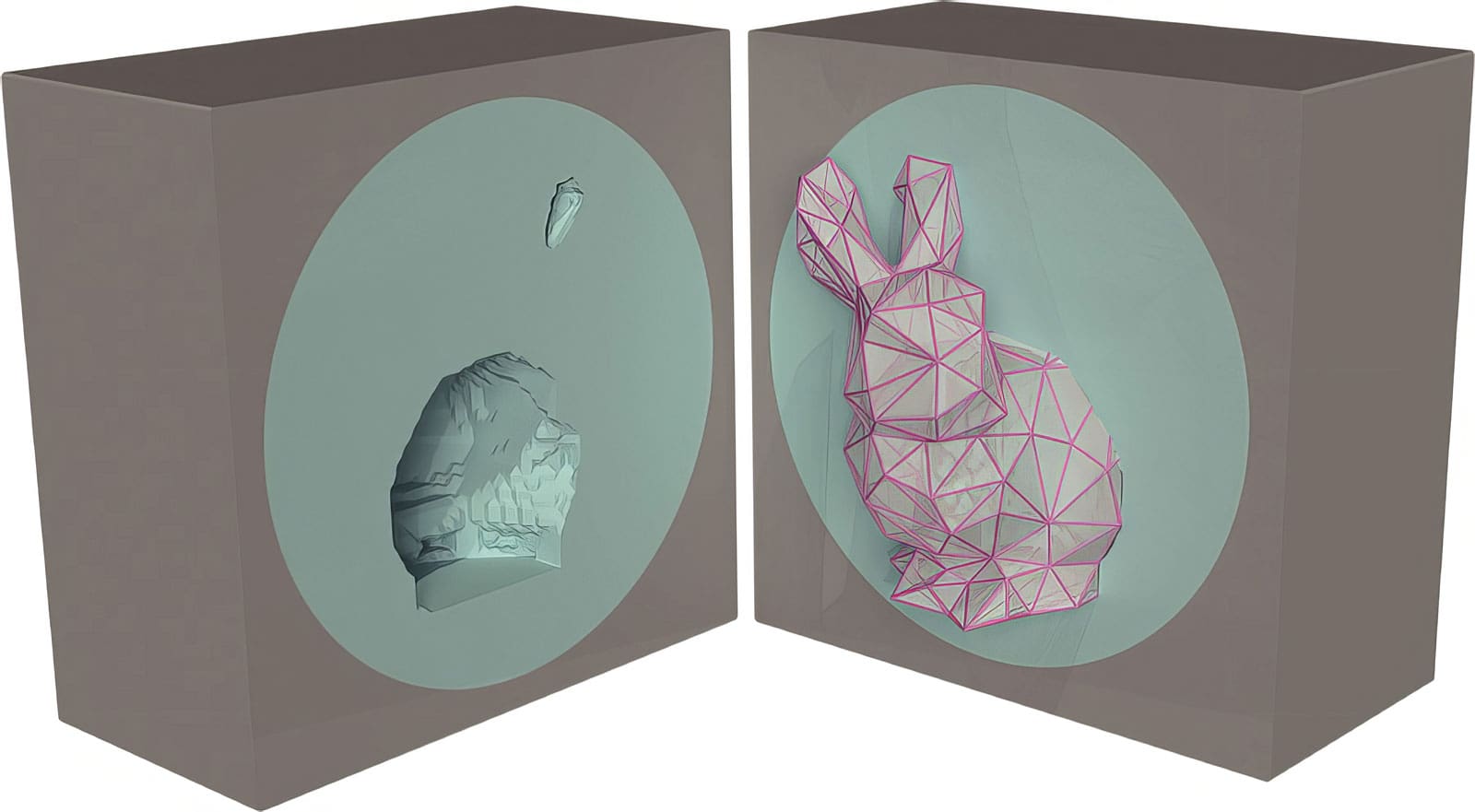
Engineers at Princeton University and the Georgia Institute of Technology created microstructures to shield a defect shaped like a rabbit.
Things with defects are easier to break, especially under twisting or bending. But researchers want to make that difficult, with the help of an invisible cloak.
Researchers from Georgia Tech and Princeton University are investigating a type of physical cloak—which is invisible to the eye—that can patch up mechanical defects.
Defects can often creep into manufacturing, but the invisible cloak is like a band-aid that fixes the defect as if it never existed.
The researchers specifically focused on “universal” cloaks, which can help products or structures respond normally to pressure applied via bending, twisting, or compression. The research was published in the May edition of Proceedings of the National Academy of Sciences.
The researchers classified the elastostatic cloaking band-aid as “unbiased,” meaning it doesn't distinguish between types of mechanical force. Typically, reinforcements on defects are focused on protecting structures of products against specific problems.
“Cloaking is universal; it should work for any possible elastic disturbance,” said Emily Sanders, assistant professor at Georgia Tech and co-author of the paper.
Sanders made a fairy tale analogy, comparing the cloak to the book The Princess and the Pea, in which a single pea in the mattress disturbed the sleep of a princess.
“The idea of a cloak around this pea to make the mattress seem like there's no defect at all, and it doesn't bother her while she's sleeping,” Sanders said.
The mechanical cloak could be relevant to submarines, airplanes, or tunnels, she added.
“You design something around it so that it doesn't affect the mechanical response in the system,” Sanders said.
There is typically a design focus on reinforcing defects, and the patch can only handle specific pressures. The research paper details a cloak that is “unbiased” and effective under any kind of elastic disturbance, according to Sanders.
The researchers created a defect like a cylindrical hole, then designed a cloak around the hole using spinodal material, which created the cloaking effect.
Spinodal materials can be programmed to have different mechanical properties by adjusting their structures. Spinodal material structures can also have various shapes and sizes, densities, and stiffness levels.
“We realized that these materials have a huge amount of flexibility, you can control their anisotropy, you can control their density,” Sanders said.
The researchers found a resemblance between their computer-generated cloak pattern and natural wood fiber patterns around knots in trees. Sanders said this kind of cloaking may have been happening naturally in trees, though it hasn't been proven.
Discover the Benefits of ASME Membership
The researchers optimized their cloak for challenging scenarios, then tested it by simulating 1,000 different mechanical pressures to verify it worked universally.
The cloaks performed better than traditional cloaking techniques, the researchers found.
Sanders shared that the research has many applications, “but there's a lot that needs to happen between what we put out in a research paper and getting it to market.”
It's also not clear if this is relevant before or after manufacturing.
“We haven't addressed whether we know the defect is there during design, or if we manufacture something that ends up having a defect. We haven't addressed how to go back and introduce this cloak,” Sanders said.
It took roughly six years to complete the research and publish the paper. The researchers wanted to understand the true meaning of cloaking, and they had to pivot from their original hypothesis, which didn't pan out, but led to a better discovery.
“Being able to be okay with that was like something new... how to reframe your thinking and still realize that you have something interesting was something that I learned,” Sanders said.
Professor Glaucio Paulino of Princeton introduced the research idea, while Sanders focused on the topology optimization, and Fernando Vasconcelos Senhora, who was then at Princeton and is now in industry, found the worst-case loads and handled the algorithms and optimization code.
Agam Shah is a business and technology writer in Phoenix.
Researchers from Georgia Tech and Princeton University are investigating a type of physical cloak—which is invisible to the eye—that can patch up mechanical defects.
Defects can often creep into manufacturing, but the invisible cloak is like a band-aid that fixes the defect as if it never existed.
The researchers specifically focused on “universal” cloaks, which can help products or structures respond normally to pressure applied via bending, twisting, or compression. The research was published in the May edition of Proceedings of the National Academy of Sciences.
The researchers classified the elastostatic cloaking band-aid as “unbiased,” meaning it doesn't distinguish between types of mechanical force. Typically, reinforcements on defects are focused on protecting structures of products against specific problems.
“Cloaking is universal; it should work for any possible elastic disturbance,” said Emily Sanders, assistant professor at Georgia Tech and co-author of the paper.
Sanders made a fairy tale analogy, comparing the cloak to the book The Princess and the Pea, in which a single pea in the mattress disturbed the sleep of a princess.
“The idea of a cloak around this pea to make the mattress seem like there's no defect at all, and it doesn't bother her while she's sleeping,” Sanders said.
The mechanical cloak could be relevant to submarines, airplanes, or tunnels, she added.
“You design something around it so that it doesn't affect the mechanical response in the system,” Sanders said.
There is typically a design focus on reinforcing defects, and the patch can only handle specific pressures. The research paper details a cloak that is “unbiased” and effective under any kind of elastic disturbance, according to Sanders.
The researchers created a defect like a cylindrical hole, then designed a cloak around the hole using spinodal material, which created the cloaking effect.
Spinodal materials can be programmed to have different mechanical properties by adjusting their structures. Spinodal material structures can also have various shapes and sizes, densities, and stiffness levels.
“We realized that these materials have a huge amount of flexibility, you can control their anisotropy, you can control their density,” Sanders said.
The researchers found a resemblance between their computer-generated cloak pattern and natural wood fiber patterns around knots in trees. Sanders said this kind of cloaking may have been happening naturally in trees, though it hasn't been proven.
Discover the Benefits of ASME Membership
The researchers optimized their cloak for challenging scenarios, then tested it by simulating 1,000 different mechanical pressures to verify it worked universally.
The cloaks performed better than traditional cloaking techniques, the researchers found.
Sanders shared that the research has many applications, “but there's a lot that needs to happen between what we put out in a research paper and getting it to market.”
It's also not clear if this is relevant before or after manufacturing.
“We haven't addressed whether we know the defect is there during design, or if we manufacture something that ends up having a defect. We haven't addressed how to go back and introduce this cloak,” Sanders said.
It took roughly six years to complete the research and publish the paper. The researchers wanted to understand the true meaning of cloaking, and they had to pivot from their original hypothesis, which didn't pan out, but led to a better discovery.
“Being able to be okay with that was like something new... how to reframe your thinking and still realize that you have something interesting was something that I learned,” Sanders said.
Professor Glaucio Paulino of Princeton introduced the research idea, while Sanders focused on the topology optimization, and Fernando Vasconcelos Senhora, who was then at Princeton and is now in industry, found the worst-case loads and handled the algorithms and optimization code.
Agam Shah is a business and technology writer in Phoenix.
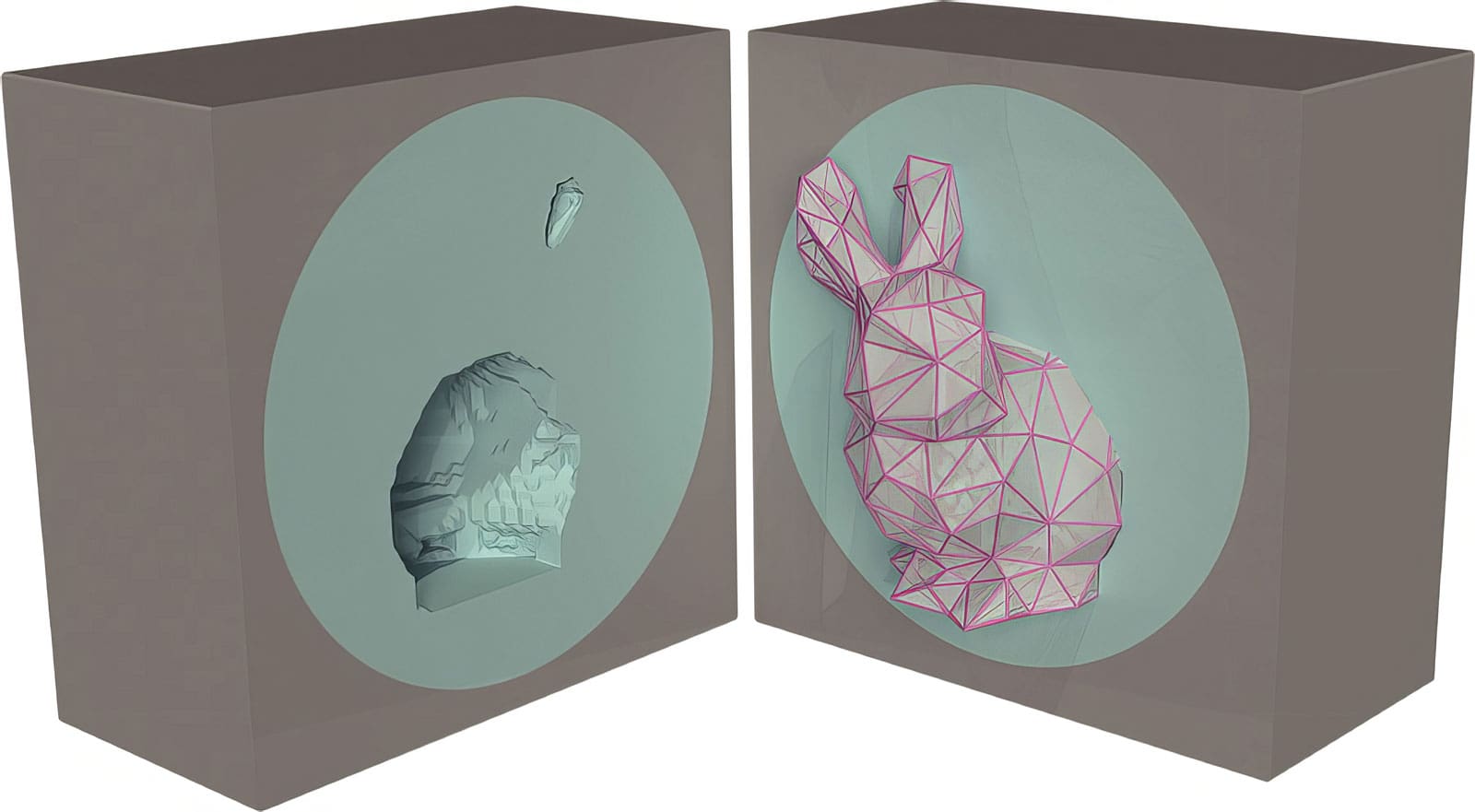
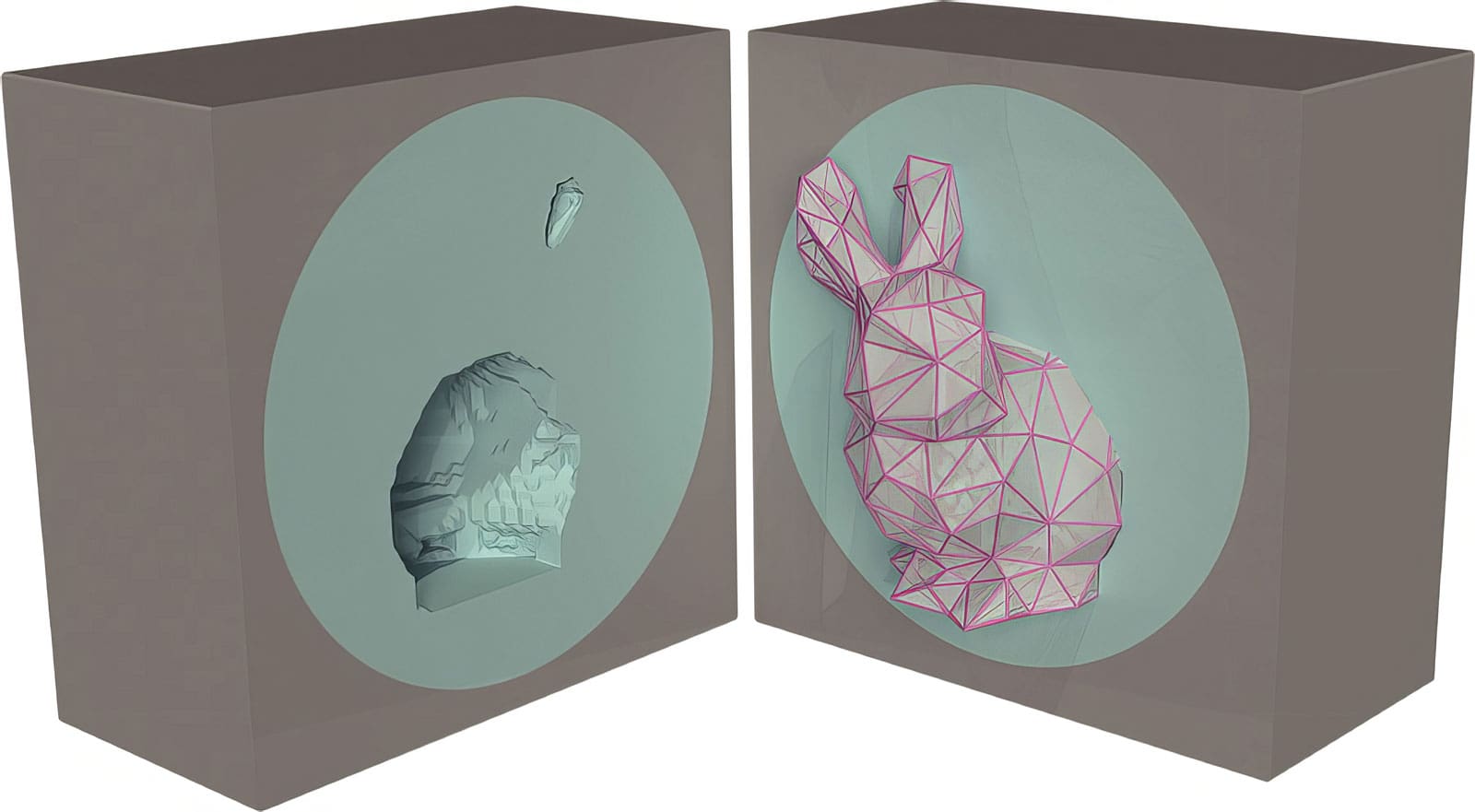