Soft Magnetized Powders for 3D Printing Offer Boost for Electric Motors
Soft Magnetized Powders for 3D Printing Offer Boost for Electric Motors
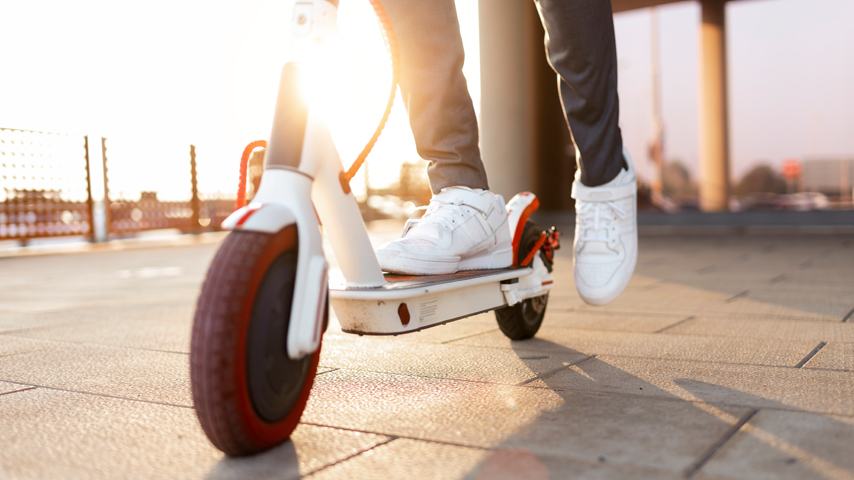
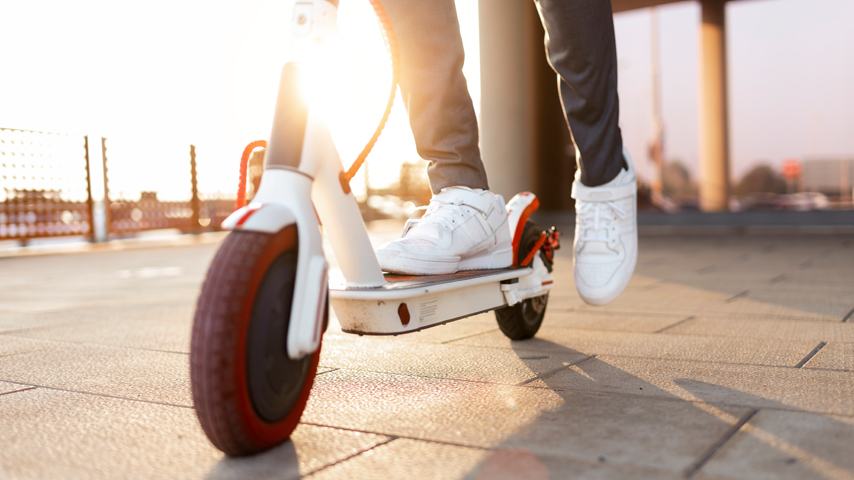
Higher silicon content in steel alloys used for electric motors offers numerous benefits, and is now proving possible to produce thanks to 3D printing and iron-silicon powder.
Silicon, a naturally occurring nonmetallic, chemical element from the carbon family, commonly serves as an additive in steel used for electric motors. A European initiative, called the SOMA Project, is working to enhance the performance characteristics of silicon alloys in an e-scooter motor, which has the potential to scale development to larger electric motors.
Elkem, an R&D-focused silicon producer in Norway, has partnered with VTT, Siemens, Stellantis, and Gemmate Technologies on the effort.
Silicon alloys exhibit higher electrical resistivity than steel alone, reducing hysteresis and eddy current losses, minimizing delays, heat gain, and energy losses due to changing magnetic fields.
In an electric motor, current flows through a wire within the motor and creates a magnetic field, which interacts with a permanent magnet or electromagnet inside the motor. The interaction between the two magnetic fields, known as Lorentz force, turns the motor, converting electrical energy into mechanical energy. The type of electric motor, whether DC, single-phase, or three-phase, impacts whether the permanent magnetic field inside the motor remains stationary or rotated, thus affecting the motor’s operation and application.
The research team found that silicon improved the magnetic properties of a motor, allowing the material to magnetize and demagnetize more easily, thereby enhancing efficiency. Additionally, silicon additives increased strength, durability, and temperature resistance, enabling a wider variety of motor applications and environments.
Traditional electric motor manufacturing uses a process called cold rolled motor lamination (CRML). Cold rolled sheets of steel combined with a minimal amount of carbon and silicon are stacked and fused together. Then, a die cuts these sheet stacks into the shape of a part. However, the CRML process does create significant waste with the leftover material after the die cutting process.
The silicon content during CRML is limited to 3 percent due to increased brittleness caused by changes in the material’s microstructure and mechanical properties. Higher silicon content is linked to increased corrosion resistance, oxidation resistance, hardness, and strength. Maintaining a balance between constructability and operation poses challenges, but 3D printing offers a solution.
Discover the Benefits of ASME Membership
“You can’t cold roll [steel] when the silicon content is higher than a certain level. But in 3D printing, you could increase the silicon content, without brittleness, and influence resistivity losses,” explained Jan Ove Odden, project manager in Elkem’s Silicon Production Development department.
In laser powder bed fusion (LPBF), the part geometry is divided into a series of 2D layers. A laser melts and fuses each layer to the build plate to construct the part. This process rapidly cools the part as each layer is melted, improving layer adhesion, surface finish, and overall strength of the print.
But fast cooling from 3D printing does cause some issues in the microstructure, Odden explained. “This created an opportunity to add more silicon than conventional manufacturing,” he said.
For the most part, 3D printing uses powdered versions of traditional manufacturing materials. As 3D printing has evolved and the industry has grown, manufacturers and researchers have tested enhancements to the powder composition to improve printability and strength.
“We’ve done some digital modeling and experiments on the composition to determine how much silicon and other elements can be added,” Odden said. “The silicon content in the powder for 3D printing is elevated to 5 percent to 6.5 percent, compared to the conventional 3 percent.”
To make iron silicon powder, Elkem built a small batch atomizer capable of manufacturing up to 10 kilograms of powder per batch. Typical powder manufacturing produces up to 200 kilograms of powder but incurs high costs when testing new recipes. Workers loaded iron, silicon, and other additives into a hopper and melted them using an induction furnace capable of reaching 3,000 °F. The molten material meets atomization gas—in this case, argon at 1,000 PSI and up to 840 °F—as it flows through a die, creating a spray pattern.
If the spray pattern, referred to as a plume, spreads too wide, material hits the walls of the hopper, causing splatter and loss. If the plume moves too fast, it creates coarser particles, whereas if it’s too slow, it produces finer particles. Additionally, clogging the die could halt the entire production run of powder. The researchers used trial and error to dial in the atomizer parameters, maximizing the number of particles created in the size range suitable for 3D printing.
You Might Also Enjoy: Better Flaw Detection During Powder Bed Fusion
Even with the atomizer parameters set correctly, roughly 50 percent of the particles ranged from 20-60 microns, another 25 percent from 60-120 microns, and the final 25 percent below 20 microns. While particles between 20-60 microns are ideal for 3D printing, industry has found uses for other particles such as in protective coatings.
“We tried a different iron-silicon composition at first, based on digital modeling of how it would behave during printing and cooling without cracking. The model was successful, but when we built the part, it ended up cracking,” Odden said. “Due to limited time to remodel, we tried printing another composition, which was successful, and this is the one that you see the result of here.”
Elkem is continuing its research from the SOMA project into the Multi Mag project, which is aimed at developing high performance, market-ready materials to create lightweight and energy efficient components for electric motors. By harnessing the potential of 3D printing and innovative alloy compositions, the project aims to deliver lightweight and energy-efficient components, further advancing the evolution of electric motor technology.
Nicole Imeson is an engineer and writer in Calgary, Alberta.
Elkem, an R&D-focused silicon producer in Norway, has partnered with VTT, Siemens, Stellantis, and Gemmate Technologies on the effort.
Silicon alloys exhibit higher electrical resistivity than steel alone, reducing hysteresis and eddy current losses, minimizing delays, heat gain, and energy losses due to changing magnetic fields.
In an electric motor, current flows through a wire within the motor and creates a magnetic field, which interacts with a permanent magnet or electromagnet inside the motor. The interaction between the two magnetic fields, known as Lorentz force, turns the motor, converting electrical energy into mechanical energy. The type of electric motor, whether DC, single-phase, or three-phase, impacts whether the permanent magnetic field inside the motor remains stationary or rotated, thus affecting the motor’s operation and application.
The research team found that silicon improved the magnetic properties of a motor, allowing the material to magnetize and demagnetize more easily, thereby enhancing efficiency. Additionally, silicon additives increased strength, durability, and temperature resistance, enabling a wider variety of motor applications and environments.
Traditional manufacturing vs. 3D printing
Traditional electric motor manufacturing uses a process called cold rolled motor lamination (CRML). Cold rolled sheets of steel combined with a minimal amount of carbon and silicon are stacked and fused together. Then, a die cuts these sheet stacks into the shape of a part. However, the CRML process does create significant waste with the leftover material after the die cutting process.
The silicon content during CRML is limited to 3 percent due to increased brittleness caused by changes in the material’s microstructure and mechanical properties. Higher silicon content is linked to increased corrosion resistance, oxidation resistance, hardness, and strength. Maintaining a balance between constructability and operation poses challenges, but 3D printing offers a solution.
Discover the Benefits of ASME Membership
“You can’t cold roll [steel] when the silicon content is higher than a certain level. But in 3D printing, you could increase the silicon content, without brittleness, and influence resistivity losses,” explained Jan Ove Odden, project manager in Elkem’s Silicon Production Development department.
In laser powder bed fusion (LPBF), the part geometry is divided into a series of 2D layers. A laser melts and fuses each layer to the build plate to construct the part. This process rapidly cools the part as each layer is melted, improving layer adhesion, surface finish, and overall strength of the print.
But fast cooling from 3D printing does cause some issues in the microstructure, Odden explained. “This created an opportunity to add more silicon than conventional manufacturing,” he said.
Making powder
For the most part, 3D printing uses powdered versions of traditional manufacturing materials. As 3D printing has evolved and the industry has grown, manufacturers and researchers have tested enhancements to the powder composition to improve printability and strength.
“We’ve done some digital modeling and experiments on the composition to determine how much silicon and other elements can be added,” Odden said. “The silicon content in the powder for 3D printing is elevated to 5 percent to 6.5 percent, compared to the conventional 3 percent.”
To make iron silicon powder, Elkem built a small batch atomizer capable of manufacturing up to 10 kilograms of powder per batch. Typical powder manufacturing produces up to 200 kilograms of powder but incurs high costs when testing new recipes. Workers loaded iron, silicon, and other additives into a hopper and melted them using an induction furnace capable of reaching 3,000 °F. The molten material meets atomization gas—in this case, argon at 1,000 PSI and up to 840 °F—as it flows through a die, creating a spray pattern.
If the spray pattern, referred to as a plume, spreads too wide, material hits the walls of the hopper, causing splatter and loss. If the plume moves too fast, it creates coarser particles, whereas if it’s too slow, it produces finer particles. Additionally, clogging the die could halt the entire production run of powder. The researchers used trial and error to dial in the atomizer parameters, maximizing the number of particles created in the size range suitable for 3D printing.
You Might Also Enjoy: Better Flaw Detection During Powder Bed Fusion
Even with the atomizer parameters set correctly, roughly 50 percent of the particles ranged from 20-60 microns, another 25 percent from 60-120 microns, and the final 25 percent below 20 microns. While particles between 20-60 microns are ideal for 3D printing, industry has found uses for other particles such as in protective coatings.
“We tried a different iron-silicon composition at first, based on digital modeling of how it would behave during printing and cooling without cracking. The model was successful, but when we built the part, it ended up cracking,” Odden said. “Due to limited time to remodel, we tried printing another composition, which was successful, and this is the one that you see the result of here.”
Elkem is continuing its research from the SOMA project into the Multi Mag project, which is aimed at developing high performance, market-ready materials to create lightweight and energy efficient components for electric motors. By harnessing the potential of 3D printing and innovative alloy compositions, the project aims to deliver lightweight and energy-efficient components, further advancing the evolution of electric motor technology.
Nicole Imeson is an engineer and writer in Calgary, Alberta.
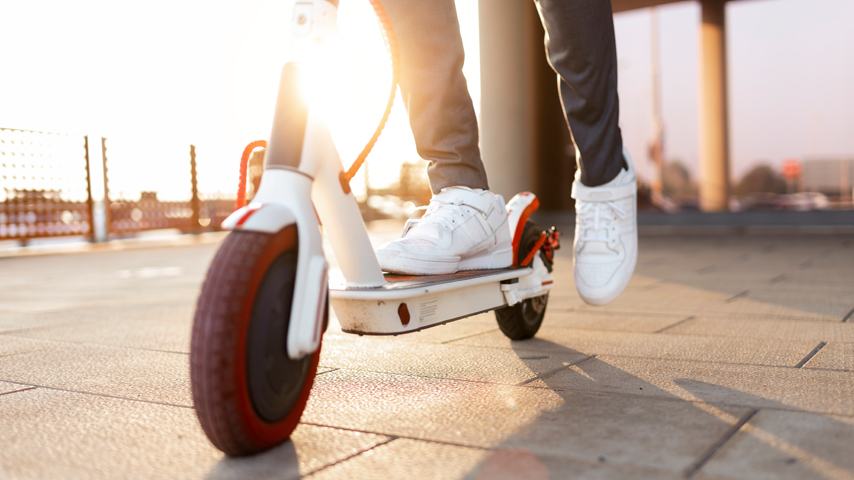
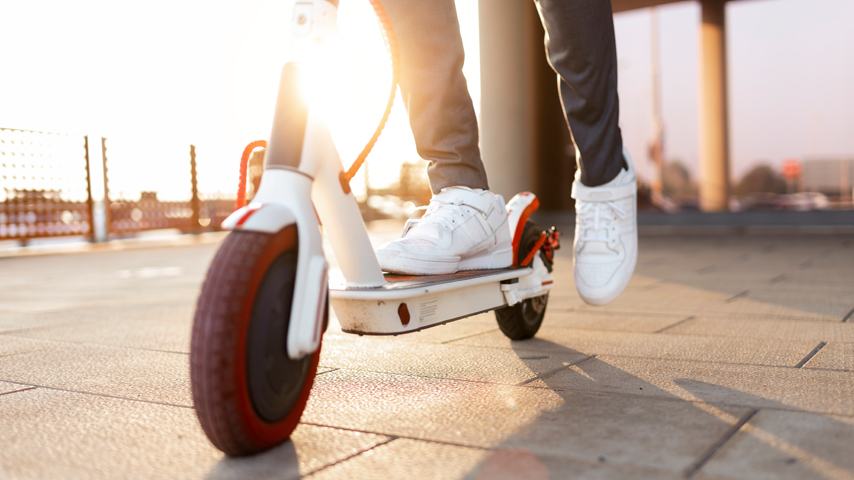