Beyond Graphite with Tin Foam Battery Electrodes
Beyond Graphite with Tin Foam Battery Electrodes
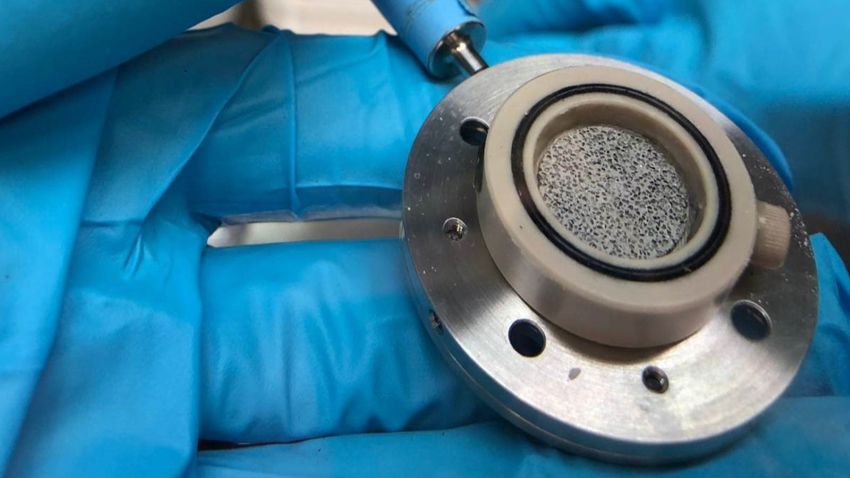
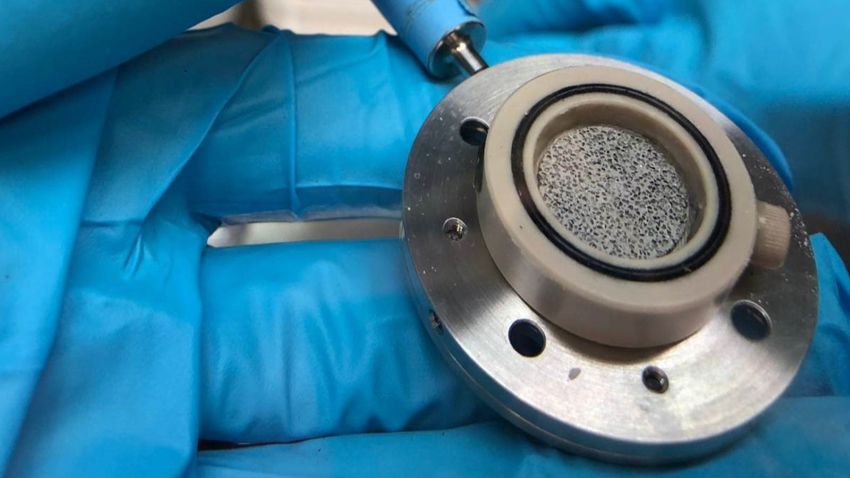
One of lithium-ion battery technology’s biggest challenges is metal electrode degradation, which researchers are looking to solve with an unlikely material: tin foam.
An innovative use of tin foam could soon transform energy storage.
Engineers have long favored graphite for battery electrodes, drawn to its conductivity and reliability. But as demand has grown for higher-capacity materials, scientists shifted toward metal-based electrodes. Unlike graphite, which stores lithium ions between its layers through intercalation, metals form new compounds with lithium, enabling much higher capacities. Tin emerged as a promising candidate, offering nearly triple the capacity of graphite, a smaller environmental footprint, and compatibility with existing manufacturing systems.
Still, tin comes with a flaw. Solid tin electrodes can’t withstand the intense expansion and contraction triggered by charging and discharging. Lithium-ion batteries generate power by moving ions between electrodes through an electrolyte. When lithium ions enter a tin electrode, they form new compounds with the metal, causing a sharp increase in volume, forcing the material to expand. When the ions withdraw, the compounds break down, and the electrode shrinks.
“The metal expands and contracts during lithiation [charging] and de-lithiation [discharging], creating cracks and breaking down the material over multiple cycles,” explained Francisco Garcia-Moreno, a physicist in the Department Microstructure and Residual Stress Analysis at Helmholtz Zentrum Berlin in Germany. “Our original idea was to design internal cavities—spaces that would let the metal expand inward without deteriorating during cycling. Although expansion still occurs, we found that the foam structure withstands it much better than solid material.”
Editor's Choice: Induction Welding Can Bond Composite Metal Foam
Tin foam’s porous, 3D structure expands surface area while creating internal space to absorb volume changes. The foam flexes without breaking, maintains conductivity through its network of pores, and holds up under stress—preserving battery life and stability.
“The interconnected structure of tin foam preserved electrical contact. Even if cracks formed or small particles detached, the network of connections ensured continuous electrical pathways. This robustness improves battery performance and reliability,” Garcia-Moreno said.
Making foam
Researchers created tin foam using a powder metallurgical placeholder method. They first sieved tin powder to a precise grain size—20 to 50 micrometers—to ensure uniform distribution. Next, they mixed the powder with ammonium hydrogen carbonate crystals, which acted as pore-forming placeholders, in a 50:50 volume ratio. After combining, they pressed the mixture into tablets at room temperature.
A two-stage vacuum heating process called sintering followed. As temperatures climbed, the place holder (ammonium hydrogen carbonate) decomposed into gas and escaped, carving out a network of pores. Simultaneously, the tin particles fused, forming a solid, porous structure with roughly 54 percent porosity. By adapting standardized metal foam production techniques, the researchers created a method suitable for large-scale production.
“The sintering led to two things. First, the metallic powders bonded together. Second, the ammonium hydrogen carbonate powder evaporated, creating pores,” Garcia-Moreno explained.
X-ray imaging
Using operando X-ray techniques, researchers studied real-time changes in tin foam electrodes during battery operation—without dismantling the battery. These non-destructive methods allowed them to track expansion, shrinking, cracking, and lithium movement as the battery charged and discharged.
Two types of operando X-ray imaging were used: 2D radiography and 3D tomography. Radiography captured flat images that revealed shifts in density, structure, and chemical state. Tomography built 3D models from multiple angles, showing how materials distributed and deformed inside the electrode. Together, these techniques uncovered how different tin structures—flat sheets versus porous foams—responded to stress. The foam’s pores absorbed expansion better, reducing damage and preserving performance.
Discover the Benefits of ASME Membership
“With radiography or tomography, we watched the electrodes expand and contract in real time. We saw exactly when cracks formed—whether during the first cycle, gradually over time, or during specific phase changes,” Garcia-Moreno said.
Other foam electrodes
In the late 1980s, manufacturers introduced nickel foam as a low-cost, high-conductivity alternative for nickel-metal hydride and nickel-cadmium battery electrodes. The foam’s high surface area and ability to support electrochemical reactions quickly made it a standard electrode material in batteries for portable electronics and early electric vehicles.
Nickel foam improved battery capacity, performance, and cycle life by distributing ions efficiently and reducing mechanical stress during charge-discharge cycles. It remains useful in high-power applications like supercapacitors and specialized lithium-ion setups. More recently, researchers tested nickel foam in lithium-ion and lithium-sulfur batteries. However, tin foam is showing more promise as an electrode material alternative due to its superior stress absorption and higher potential capacity.
Tin foam could serve as an alternative electrode material for sodium-ion batteries, which trade energy density for cost and safety.
Nicole Imeson is an engineer and writer in Calgary, Alta.
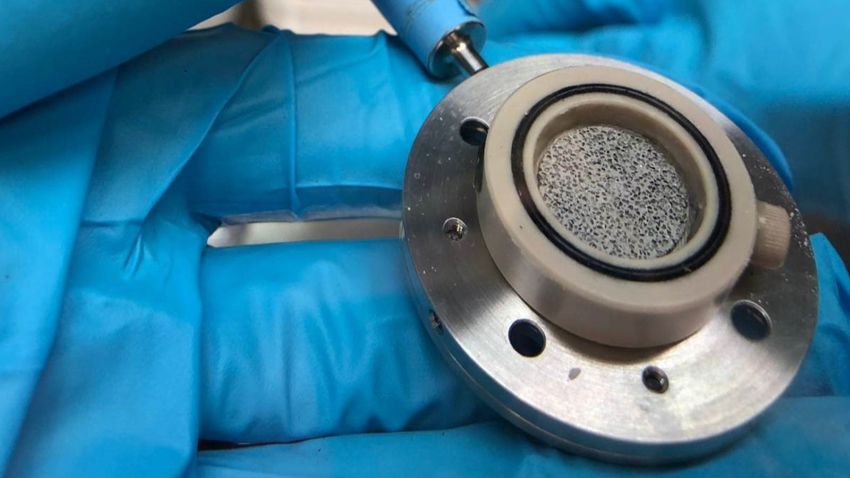
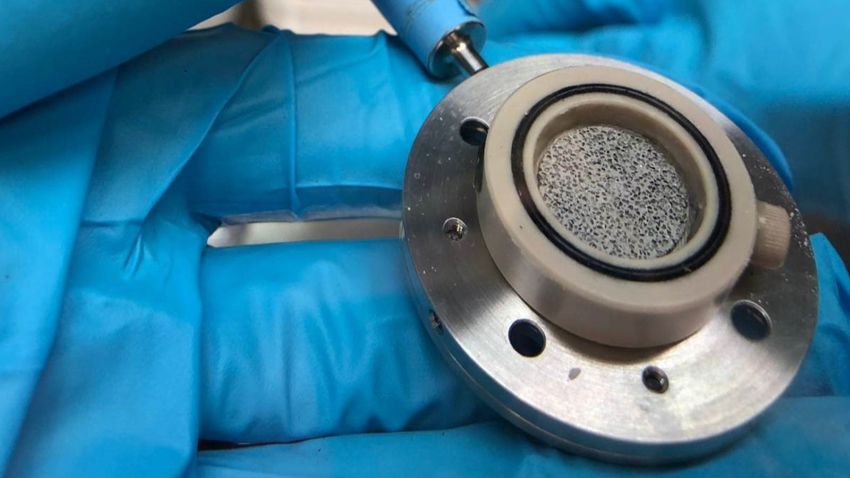