Construction Materials Made from ‘Shrooms'
Construction Materials Made from ‘Shrooms'
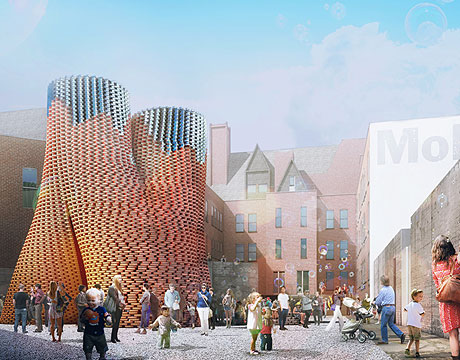
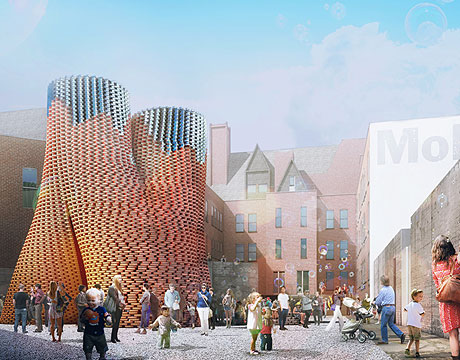
Architect David Benjamin’s winning entry for MoMA PS1’s Young Architects Program competition. Image: The Living
Architect David Benjamin walked into the offices of Arup, a structural engineering firm, with a brick in hand. It wasn’t your typical rust red, burnt clay brick. Instead, it was made largely of mushroom mycelium, grown on agricultural waste, produced by a company call Ecovative. Benjamin wanted to discuss what might be done with such a brick.
“Structural engineers work with architects a lot; quite often we see completely crazy ideas,” says Matthew Clark, who, with Shaina Saporta, was one of the two structural engineers Benjamin was visiting at Arup, NY. “But this was probably one of the most crazy.” Benjamin was hoping to create something for the Museum of Modern Art’s Young Architects Program, a contest whose guidelines placed an emphasis on sustainability and recyclability.
Exploring New Materials
Usually structural engineers build things of tried and true materials, largely concrete and steel, whose properties are well known. Now they had two projects in one. “One was normal: What do we build and how do we build it,” says Clark. “The other was find about this material, how strong is it, and how stiff it is. That’s a lot of fun. It’s not that often in structural engineering that you get to explore a completely new material.”
To begin the exploration, the engineers performed a rough stress test: They stood on the brick. It survived the ordeal, allowing them to perform some rough calculations about capabilities. “In a competition, you want the entry to be exciting, but there’s no time to do the science, to know for sure if it will work,” says Clark. “So you stand on a brick. If you win the competition, you have a good start to go ahead and explore.”
As the brick had limited stiffness, Clark, Saporta, and Benjamin began to explore curved structures, cones, and cylinders, for the added stability they offered. The double curve they came up with, named Hy-Fi, offered maximum strength with a stiff, wide base resistant to wind loads, and a soaring statement that could be viewed from within and afar.
When MoMA announced that the team had won the contest, the real exploration began. Clark and Saporta started working with Ecovative to make the stiffest mushroom brick possible.
Making Mushroom Bricks
Making the bricks is simple enough. Mix some mushroom spores with farm waste, pot it, and let it grow. Then take the bricks out of the molds and bake to kill the mushrooms. The process gave the Arup team essentially two variables: the type of agricultural waste used and the time that the mushrooms were allowed to grow. They tested six iterations with load tests at Columbia University, wind tests at BMT Fluid Mechanics, and aging tests at Advanced Metal Coatings. For maximum stiffness they settled on corn stalks for waste material and a 10-day growth period. “By letting them grow longer we get more of the mycelium, and the bricks have less void value,” says Saporta.
The final result is a mushroom brick that’s 200,000 times softer than steel, 10,000 times less stiff than a typical housing brick, but capable of holding the equivalent of 50 cars.
The idea of a durable but biodegradable brick is something of an oxymoron. Weather-proofing them without destroying their essential compostability was a conflict from the start. Sealing each brick in polyurethane would have solved the problem completely but would have flown in the face of the concept as well as the rules. Instead, they used natural oil penetrated into the bricks. They tested the coated bricks in a “domestic shower,” says Clark, and found they only gained a few percentage points of mass. “They don’t go really soggy and flexible,” he says.
Those few percentage points would mean the structure would degrade over time, part of Benjamin ’s initial conception. In its first few weeks of existence the tower was hit with heavy rainstorms. “You can see the difference, but it’s held up pretty well,” says Clark. It can also withstand 65-mph wind gusts (the museum will just shut the courtyard if they get that high) as well as the weight of a few extra bodies. “We’ve seen people climb it—not advisable—but it’s a very robust structure.”
Though the mushroom brick may have its applications—as insulation, or as the wall of a pavilion—the goal of the Hy-Fi project was to show the world that alternatives to the traditional are available with the application of a little imagination. “As structural engineers we tend to be asked to design things that have to last for 50 years and at large scales,” says Clark. “While the mushroom brick is not directly applicable to that, it’s changed the way we think about materials in general. It’s also remarkable from an engineering front: You can still build with a material 200 times less stiff than masonry. You don’t have to immediately dismiss it because it’s soft and floppy.”
Michael Abrams is an independent writer.
As structural engineers we tend to be asked to design things that have to last for 50 years and at large scales.Matthew Clark, structural engineer, Arup
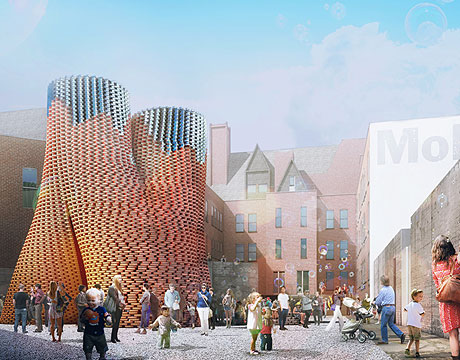
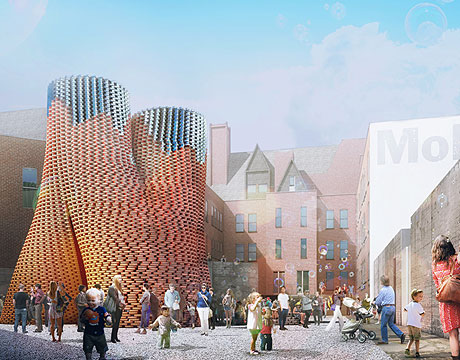