Lakshmi Vendra Reviews AM’s Use in Oil and Gas
Lakshmi Vendra Reviews AM’s Use in Oil and Gas
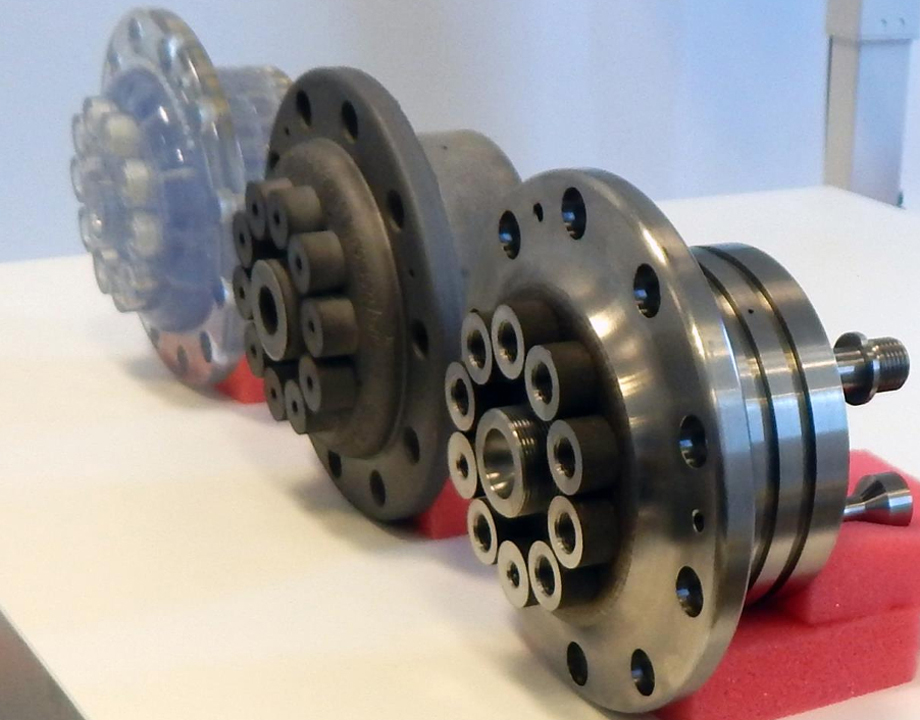
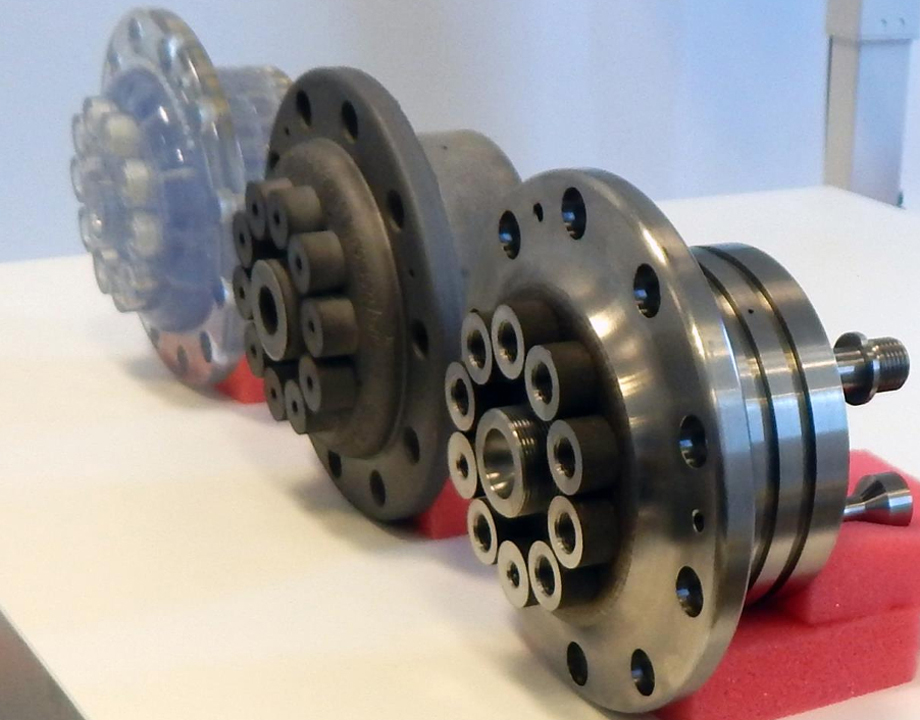
Additive manufacturing is quickly penetrating the oil and gas industry. Image: Lloyd's Register
Lakshmi Vendra is team leader of additive manufacturing technology at Baker Hughes and is responsible for overcoming key challenges in the adoption of additive manufacturing as a viable industry technology. She is a recognized expert in applied research and transforming technology into commercial products. Vendra will be speaking at the ASME Industry Summit about additive manufacturing application opportunities for energy. She spoke with ASME.org on AM’s growth in the oil and gas industry.
Q1: Much of AM’s development has been done in manufacturing and industrial applications. Has AM lagged in the oil and gas sector?
Lakshmi Vendra: Industrialization of AM is at an advanced stage in other industries such as aerospace, automotive and healthcare where AM is being used to produce certified end-use parts such as vehicle spare parts, biomedical implants, and rocket engine components. In the oil and gas industry, the industrial applications are widespread and we have transitioned from using AM for functional prototypes to test form, fit and function to production of end-use parts. Final part manufacturing, using metal AM is definitely the most interesting application within oil and gas, providing solutions to improve performance while cutting down costs and lead time or offering new features such as light weight or better efficiency.
Q2: What are the biggest needs where AM can make an impact?
LV: As with other industry sectors, benefits of AM in oil and gas are also around reducing lead times, elimination of tooling and overcoming disruptions to supply chain. The ability to produce more complex geometries, designing for functionality, part consolidation, reduction in weight are all key advantages that we can leverage with AM. Turbomachinery components, pumps, impellers, drill bits and other drilling equipment are some of the end-use metal parts that are being produced with AM today, with enhanced life and performance as advantages when compared to conventional counterparts.
Editor's Pick: Additive Manufacturing Poised to Remake Renewable Energy
Q3: Will AM increase the ability for stocking of legacy components that may be difficult to source?
LV: With AM, conventional inventory or maintaining a safety stock are no longer needed. All we need is to stock the 3D CAD model of the component in our digital warehouse and when a customer places an order, the part would be printed and delivered in a matter of days. Legacy components that are difficult to source due to obsolete designs could also be produced through reverse engineering; scanning the part, creating a digital model and subsequently 3D printing it.
Q4: What legal concerns remain in areas of licensing, certification, intellectual property?
LV: A significant number of patent applications related to AM are submitted every year, a great indicator of innovation and technology advancement potential within AM. Even if patents have expired, it’s always a good idea to check IP rights on follow-on filings when kicking off new product innovation projects. Licensing of the technology or finding a way around the patent claims are some of the strategies to create intellectual property, a strong asset to technology companies. Lack of certification guidelines and standardization processes continue to limit the growth and adoption of AM. However, we have several standards development organizations such as API, ASTM, and ASME working toward standardization.
Reader's Choice: Energy Blog: Hydrogen Straight From the Earth
Q5: What has the biggest advancement been in AM affecting oil & gas?
LV: Repeatability and reproducibility have always been the key challenges to scaling up AM production. Therefore, AM technologies such as laser powder bed fusion that are mature in terms of achieving process capability are being utilized to produce metal parts. Advancements in improving design for AM for optimal print orientation and support structures, thermal distortion analysis to predict build outcomes and reduce iterative builds, in-situ monitoring technologies to detect anomalies as they occur have all helped in enhancing quality assurance of the AM process and accelerated its adoption within oil & gas.
Q6: Where will AM be in the industry in five years?
LV: Growth in AM has already outpaced the forecast models, being driven by enhanced productivity and reduced system costs. A confluence of technology advancements in model-based design, build simulations, in-process quality control and volumetric inspections are paving the way for digital transformation and widespread acceptance of AM within the industry. AM technologies are evolving at a rapid pace adding advanced materials to the AM portfolio that enable new applications in environments never thought of before. As we have seen with the COVID-19 experience, AM has potential to create a flexible and sustainable supply chain facilitating production of parts on-site or near-site to reduce downtime.
John Kosowatz is senior editor.
Register Today for ASME AM Industry Summit: Convergence of Aerospace & Energy
Q1: Much of AM’s development has been done in manufacturing and industrial applications. Has AM lagged in the oil and gas sector?
Lakshmi Vendra: Industrialization of AM is at an advanced stage in other industries such as aerospace, automotive and healthcare where AM is being used to produce certified end-use parts such as vehicle spare parts, biomedical implants, and rocket engine components. In the oil and gas industry, the industrial applications are widespread and we have transitioned from using AM for functional prototypes to test form, fit and function to production of end-use parts. Final part manufacturing, using metal AM is definitely the most interesting application within oil and gas, providing solutions to improve performance while cutting down costs and lead time or offering new features such as light weight or better efficiency.
Q2: What are the biggest needs where AM can make an impact?
LV: As with other industry sectors, benefits of AM in oil and gas are also around reducing lead times, elimination of tooling and overcoming disruptions to supply chain. The ability to produce more complex geometries, designing for functionality, part consolidation, reduction in weight are all key advantages that we can leverage with AM. Turbomachinery components, pumps, impellers, drill bits and other drilling equipment are some of the end-use metal parts that are being produced with AM today, with enhanced life and performance as advantages when compared to conventional counterparts.
Editor's Pick: Additive Manufacturing Poised to Remake Renewable Energy
Q3: Will AM increase the ability for stocking of legacy components that may be difficult to source?
LV: With AM, conventional inventory or maintaining a safety stock are no longer needed. All we need is to stock the 3D CAD model of the component in our digital warehouse and when a customer places an order, the part would be printed and delivered in a matter of days. Legacy components that are difficult to source due to obsolete designs could also be produced through reverse engineering; scanning the part, creating a digital model and subsequently 3D printing it.
Q4: What legal concerns remain in areas of licensing, certification, intellectual property?
LV: A significant number of patent applications related to AM are submitted every year, a great indicator of innovation and technology advancement potential within AM. Even if patents have expired, it’s always a good idea to check IP rights on follow-on filings when kicking off new product innovation projects. Licensing of the technology or finding a way around the patent claims are some of the strategies to create intellectual property, a strong asset to technology companies. Lack of certification guidelines and standardization processes continue to limit the growth and adoption of AM. However, we have several standards development organizations such as API, ASTM, and ASME working toward standardization.
Reader's Choice: Energy Blog: Hydrogen Straight From the Earth
Q5: What has the biggest advancement been in AM affecting oil & gas?
LV: Repeatability and reproducibility have always been the key challenges to scaling up AM production. Therefore, AM technologies such as laser powder bed fusion that are mature in terms of achieving process capability are being utilized to produce metal parts. Advancements in improving design for AM for optimal print orientation and support structures, thermal distortion analysis to predict build outcomes and reduce iterative builds, in-situ monitoring technologies to detect anomalies as they occur have all helped in enhancing quality assurance of the AM process and accelerated its adoption within oil & gas.
Q6: Where will AM be in the industry in five years?
LV: Growth in AM has already outpaced the forecast models, being driven by enhanced productivity and reduced system costs. A confluence of technology advancements in model-based design, build simulations, in-process quality control and volumetric inspections are paving the way for digital transformation and widespread acceptance of AM within the industry. AM technologies are evolving at a rapid pace adding advanced materials to the AM portfolio that enable new applications in environments never thought of before. As we have seen with the COVID-19 experience, AM has potential to create a flexible and sustainable supply chain facilitating production of parts on-site or near-site to reduce downtime.
John Kosowatz is senior editor.
Register Today for ASME AM Industry Summit: Convergence of Aerospace & Energy
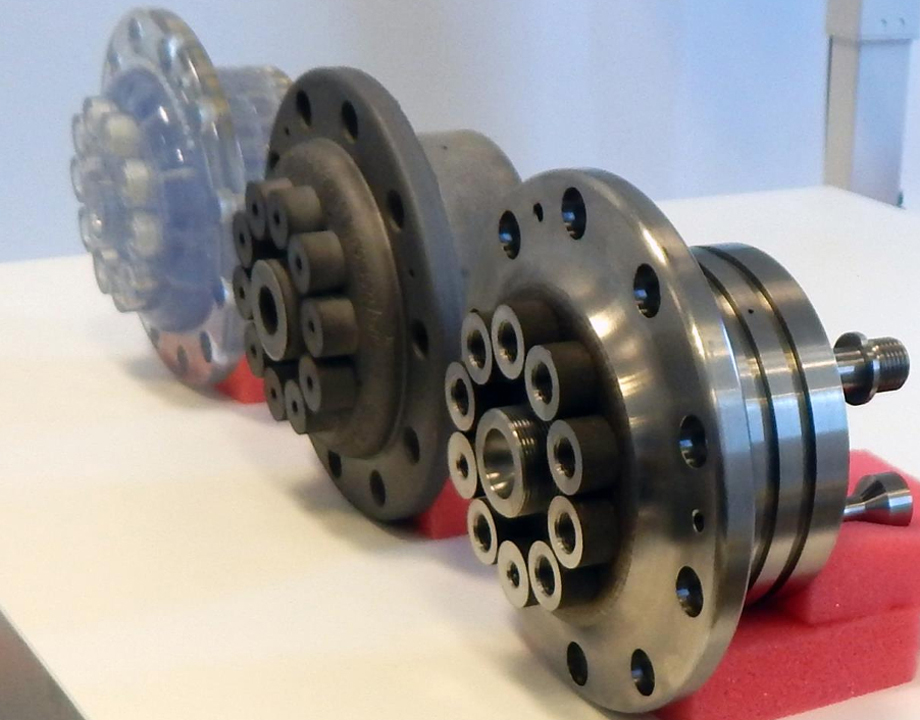
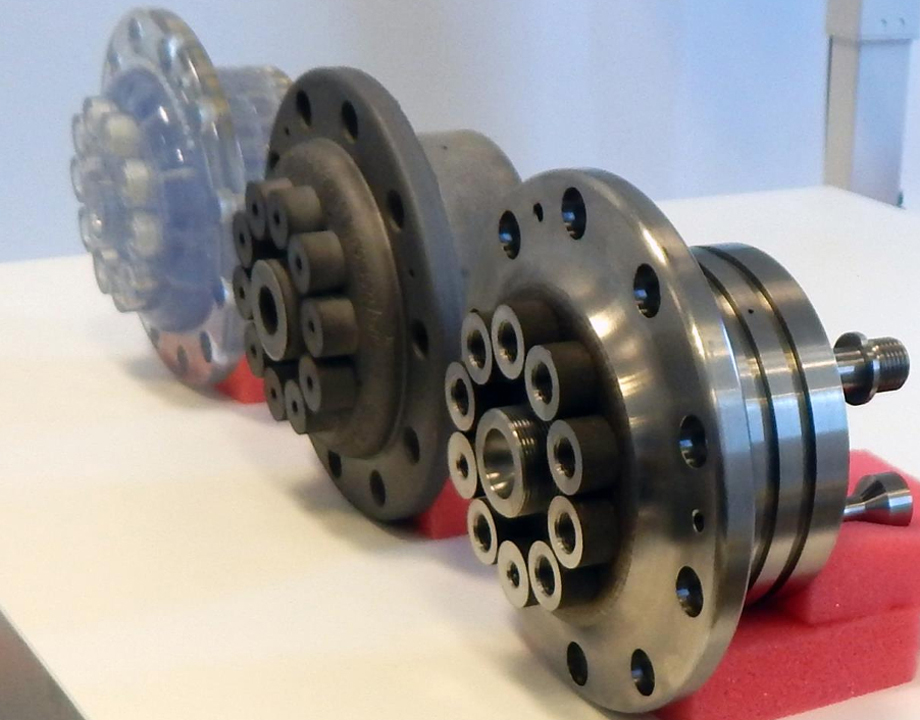