Laser Printer Evolves to 3D Printing
Laser Printer Evolves to 3D Printing
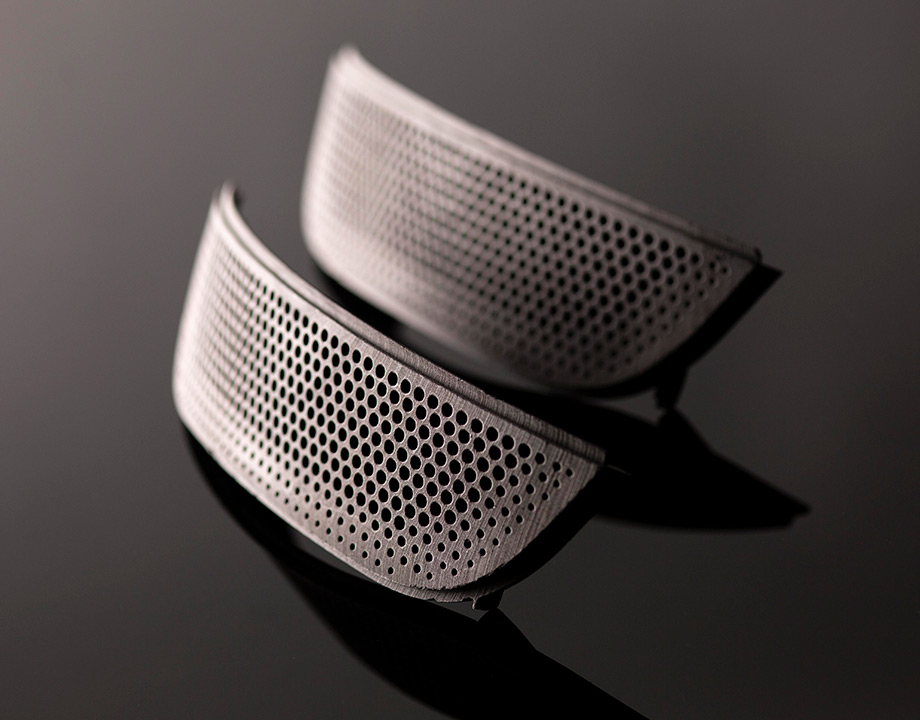
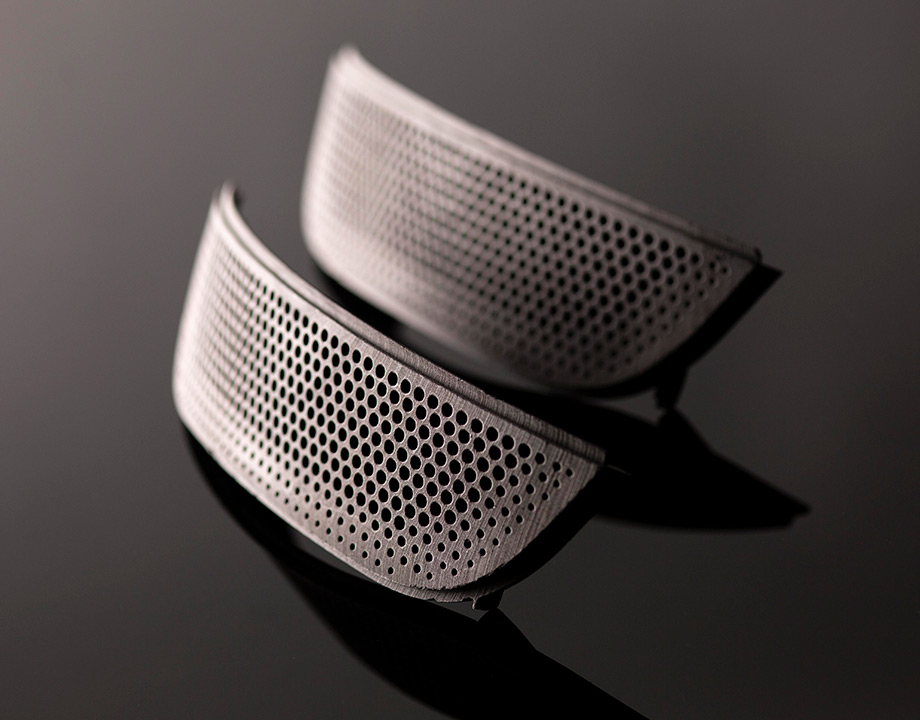
Plastic parts are 3D printed using time-tested 2D printing technology. Photo: Evolve Additive
Evolve Additive Solutions has developed an entirely new approach to 3D printing plastic parts. Called STEP, for selective thermoplastic electrophotographic process, it is based on the same technology as laser printing.
Like laser printing, STEP is fast and potentially inexpensive enough to go head to head with injection molding for tens of thousands of units.
Unlike conventional 3D printers which deposit or solidify (depending on technology) one line at a time, the STEP alpha system prints an entire layer every 2 to 4 seconds. According to Evolve CEO Steven Chillscyzn, the finished 3D parts can compete with injection molding on such quality metrics as anisotropic strength, feature detail, and finish.
Further Reading: Markforged’s Greg Mark on 3D Metal Printing, Additive Manufacturing
STEP works with toner-like particles of ABS, polyimide (nylon), and thermoplastic polyurethanes, Chillscyzn expects to add many more high-end engineering plastics in the future. He also claims his “toner” costs less to manufacture than other 3D feedstocks.
STEP’s combination of speed and low-cost feedstock enables it to compete on cost and quality with injection molding.
Background in Printing
Evolve was previously part of 3D giant Stratasys, where Chillscyzn had risen over ten years to become vice president of corporate technology development. Before that, he had worked on laser and inkjet 2D printers.
Chillscyzn reasoned that using a laser printer’s revolving drum to deposit an entire layer of plastic in a single pass would be faster than rastering a laser or 3D print head over a flat surface. One of his goals at Stratasys was to make that vision a reality.
Two years ago, he convinced Stratasys to spin off the technology so he could raise outside capital to fund it. His investors include Lego, Black & Decker, and Stratasys, which owns a minority share of the business.
The system’s concept is simple: transfer plastic powders to a rotating drum, print the entire layer, heat to solidify and repeat until the part is done. Getting it to work, however, takes some engineering.
This starts with STEP’s materials. They start as pellets of standard injection molding polymers. The company uses a chemical process to reduce the pellets to micron-sized powders. It then compounds them with 1 percent of an organic additive that picks up electrostatic charges. Chillscyzn calls this process “tonerization.”
Evolve also tonerizes a separate material to support its 3D structures. It is soluble and dissolves within 12 hours, leaving a free-standing part.
Further Reading: Chain Reaction
The printing process is built around a modified Kodak Nextpress, a commercial color laser system that can print millions of pages per year.
The STEP process starts like a laser printer. A laser traces the shape of the layer to be printed on a drum of organic material. This imparts a positive charge to the image on the drum.
As polymer and support powders slide out of their hoppers, the friction imparts them with a negative charge (like rubbing a balloon). Each powder goes to a separate drum, where it sticks to the positively charged image.
The first layer of the object is transferred to an oppositely charged carrier sheet on a reciprocating belt. The deposition takes only seconds. Then the belt transports the layer to a heater, which uses pressure and heat to fuse the powders. Once cooled, the carrier goes back to the drum for another layer, then repeats the heat treatment. The process continues until the part is done, producing a 100 percent dense part, Chillsyczn said.
“The tricky part is the registration,” Chillsyczn said. “We use a combination of closed-loop control, vision systems, and pressure and temperature sensors to make sure the top of incoming layer matches the top of part we’re building. We have a lot of patents around this.”
The system has up to five different drums, Chillsyczn said. This enables it to use multiple colors and clear plastics.
Advantages Over Traditional 3D Printers
STEP has several advantages over other 3D printers, Chillsyczn claims. Speed is one of them. He said that STEP is five times faster than selective laser sintering (which does not need supports) and 50 times faster than 3D processes that use supports.
The system produces very uniform properties throughout the entire build plate, rather than just in the center. It can print crystalline and amorphous polymers on the same carrier. The machine can also inspect each layer and compensate for defects, add inserts, or build cavities to embed reinforcements or electronics.
It also scales quickly. “We can put multiple carriers on a track system and increase throughput by four times,” Chillsyczn said. “One of the issues we have today is cooling parts after fusing them. Running them on tracks would give the parts more time to cool.”
Further Reading: 6 Innovative Ways to Use 3D Printing
The company plans to charge about $1 million for a base system with a single carrier. While STEP is “serious capital equipment,” the parts are inexpensive to manufacture because of the low cost of materials, Chillsyczn said.
He also thinks the parts can compete directly with injection molding, depending on how users pack their parts for production.
“You save money by not building a mold and in some cases get competitive cycle times,” he said.
The company sees near-term potential in consumer products and automotive (especially in parts consolidation and custom fasteners), and, further out, in aerospace and medical. Evolve is locking down the second round of financing now and plans to have beta test models within a year.
Alan S. Brown is senior editor.
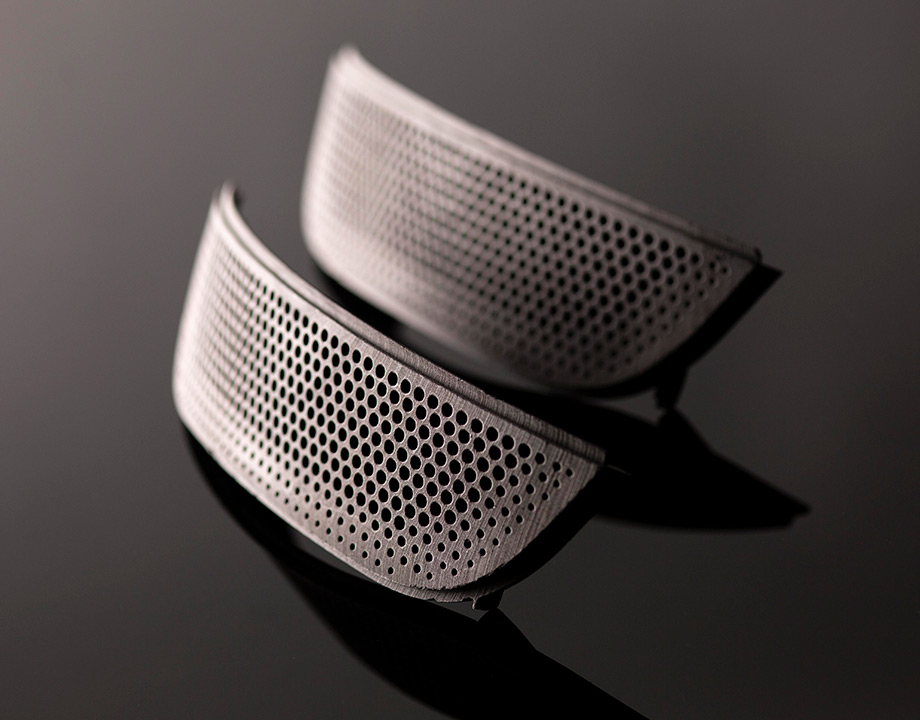
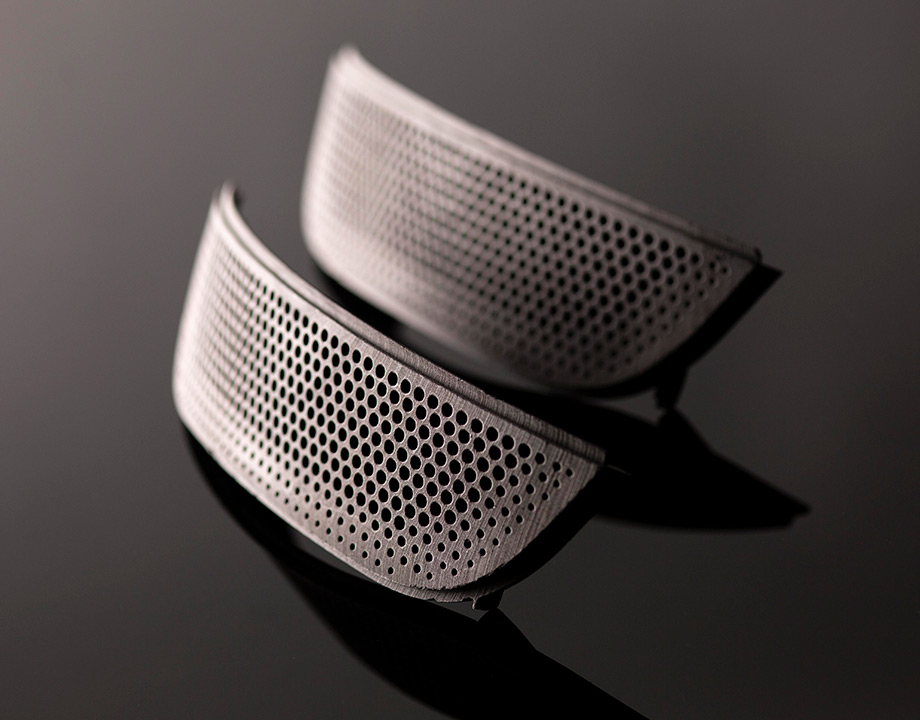