Q&A: Andreas Wendel on Self-Driving Trucks
Q&A: Andreas Wendel on Self-Driving Trucks
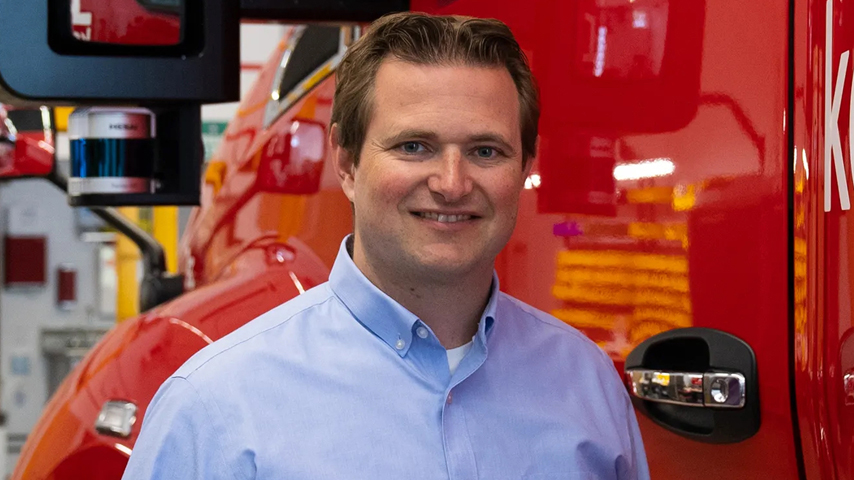
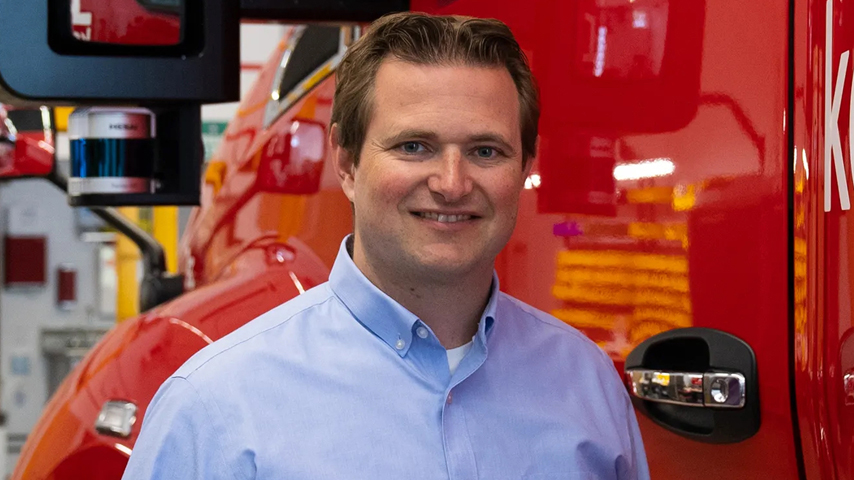
Kodiak Robotics is one startup developing autonomous driving systems for long-haul trucking. Chief Technology Officer Andreas Wendel talks about developing the system.
Autonomously operated trucks are already on the road in some parts of the U.S., although they most likely have a person in the driver’s seat as developers prove the technology and regulators become comfortable with it. Daimler, Peterbilt, and other manufacturers are working to introduce the concept, but with differing business models. Kodiak Robotics is one of the startups in the field, now operating about 30 rigs driving a Dallas-to-Atlanta route. CTO Andreas Wendel, who came to the firm from Waymo, talked with ME Magazine about their work.
ME: Why did Kodiak choose trucks to apply this technology?
AW: Our founder, Dan Burnett, also was with Waymo before it was called Waymo. It was called Google self-driving cars, and there we worked on passenger vehicles. But it was hard to make this a great product because customers want to get exactly to a [defined] place. In the city, that is really hard to do. We thought about where the technology can be applied much sooner, and trucking is where that can happen. We can drive safely on the highways, and we can deliver goods. We can really push the technology in terms of safety. But we don’t need that comfort for how we bring someone to a certain location.
Become a Member: How to Join ASME
ME: How much of the system was developed inhouse?
AW: We started from scratch. We built up the software, and the hardware first on a small box truck because none of us had a Class 8 driver's license. We developed the perception system from the beginning. We focused a lot on safety. When our first semi-truck arrived, we had everything preplanned. We actually put in the actuation, the sensing, cameras, Lidar, radar, and the computer.
ME: The company is called Kodiak Robotics, not Kodiak Trucking. Why?
AW: The Kodiak Driver is our autonomy software. Say you’re a trucking company. You hire a driver. In our case, you would actually hire the Kodiak Driver and the code. The driver happens to be a package of technology, the software and the hardware that put into your truck, and we do all the driving for you. The business model right at the moment is that we do this in our own trucks. In the future, we can actually equip [another company’s] trucks with our technology and drive for you. This is why it is called Kodiak Robotics.
ME: What are the differences between autonomous highway operations and driving on city streets?
AW: In a highway environment it is just much more structured. We still have to deal with, of course, vehicles, but also pedestrians. We actually see pedestrians on the highway pretty regularly, but there are fewer cases where a pedestrian would just carelessly cross the highway. We see those as well, and when we do, we can react in a stronger fashion. We can actually break quite hard, or lane change, but the environment is quite a bit different.
More for You: Giving Autonomous Vehicles 3D Vision
ME: What does the autonomous system consist of; how does it work?
AW: What is unique about Kodiak is that we have our sensor packs mounted on the mirrors. That allows us to quickly swap them out. Whenever a truck is sitting somewhere to be repaired it is not making any money. The assets should be out and be used, so we made these integrations in the mirrors so that they can be calibrated in a factory, and then they are shipped to a place where they can be installed. If one of the sensors would have a problem, or goes out of spec, or gets hit by another vehicle, we don’t need to do repairs in a shop. We can swap out the entire mirror pack in less time than it takes to change a tire.
ME: You’ve tested the system with human drivers sitting in the driver’s seat while operating autonomously. What is the workflow?
AW: We actually have human drivers who pick up a load from the customer and they bring the trailer to a truck port, a transfer hub that is close to the highway. We connect the trailer to the autonomous tractor and the autonomous driver goes many hours across the country. It comes to one of these ports again, and we swap the trailer to human-driven tractor, who then delivers it.
We’re really trying to solve a big problem that fleets have at the moment, which is a labor shortage. It is very hard to find people who want to do over-the-road transport. They’re away from their families for many hours.
Editor's Pick: Self-Driving Cars May Soon Have Their Own Special Memories
ME: How does the system account for accidents or malfunctions?
AW: We check for over 1,000 fault conditions 10 times per second. One of those is tire pressure, or a blowout. We have spent a lot of time on safety. When this happens, the truck really stays in its lane, the maximum deviation is about two or three inches or so from the center lane, and then it pulls over to the shoulder. This is not how humans handle them. Humans very often swerve across lanes and cause major accidents.
ME: How do the trucks navigate?
AW: We are talking about modularity. We have a computer that we can put into various trucks. We have three brands. But our mapping solution is different. Autonomous vehicles use high-definition maps that use lasers to create a model of the world, a very dense model. That works well in city environments. On long-haul transportation, the world changes very quickly We’ve built a different system to create a large map across the southern U.S., but scalable. It is fast to deploy and fast to update. Our control center in the truck does all the monitoring. All decisions are made by the onboard computer. Our trucks do not need any connectivity, they can completely run without a remote connection. The computer is the actuation computation engine. It is like an ECU that talks to the vehicle and is self-contained in the vehicle.
ME: Why did Kodiak choose trucks to apply this technology?
AW: Our founder, Dan Burnett, also was with Waymo before it was called Waymo. It was called Google self-driving cars, and there we worked on passenger vehicles. But it was hard to make this a great product because customers want to get exactly to a [defined] place. In the city, that is really hard to do. We thought about where the technology can be applied much sooner, and trucking is where that can happen. We can drive safely on the highways, and we can deliver goods. We can really push the technology in terms of safety. But we don’t need that comfort for how we bring someone to a certain location.
Become a Member: How to Join ASME
ME: How much of the system was developed inhouse?
AW: We started from scratch. We built up the software, and the hardware first on a small box truck because none of us had a Class 8 driver's license. We developed the perception system from the beginning. We focused a lot on safety. When our first semi-truck arrived, we had everything preplanned. We actually put in the actuation, the sensing, cameras, Lidar, radar, and the computer.
ME: The company is called Kodiak Robotics, not Kodiak Trucking. Why?
AW: The Kodiak Driver is our autonomy software. Say you’re a trucking company. You hire a driver. In our case, you would actually hire the Kodiak Driver and the code. The driver happens to be a package of technology, the software and the hardware that put into your truck, and we do all the driving for you. The business model right at the moment is that we do this in our own trucks. In the future, we can actually equip [another company’s] trucks with our technology and drive for you. This is why it is called Kodiak Robotics.
ME: What are the differences between autonomous highway operations and driving on city streets?
AW: In a highway environment it is just much more structured. We still have to deal with, of course, vehicles, but also pedestrians. We actually see pedestrians on the highway pretty regularly, but there are fewer cases where a pedestrian would just carelessly cross the highway. We see those as well, and when we do, we can react in a stronger fashion. We can actually break quite hard, or lane change, but the environment is quite a bit different.
More for You: Giving Autonomous Vehicles 3D Vision
ME: What does the autonomous system consist of; how does it work?
AW: What is unique about Kodiak is that we have our sensor packs mounted on the mirrors. That allows us to quickly swap them out. Whenever a truck is sitting somewhere to be repaired it is not making any money. The assets should be out and be used, so we made these integrations in the mirrors so that they can be calibrated in a factory, and then they are shipped to a place where they can be installed. If one of the sensors would have a problem, or goes out of spec, or gets hit by another vehicle, we don’t need to do repairs in a shop. We can swap out the entire mirror pack in less time than it takes to change a tire.
ME: You’ve tested the system with human drivers sitting in the driver’s seat while operating autonomously. What is the workflow?
AW: We actually have human drivers who pick up a load from the customer and they bring the trailer to a truck port, a transfer hub that is close to the highway. We connect the trailer to the autonomous tractor and the autonomous driver goes many hours across the country. It comes to one of these ports again, and we swap the trailer to human-driven tractor, who then delivers it.
We’re really trying to solve a big problem that fleets have at the moment, which is a labor shortage. It is very hard to find people who want to do over-the-road transport. They’re away from their families for many hours.
Editor's Pick: Self-Driving Cars May Soon Have Their Own Special Memories
ME: How does the system account for accidents or malfunctions?
AW: We check for over 1,000 fault conditions 10 times per second. One of those is tire pressure, or a blowout. We have spent a lot of time on safety. When this happens, the truck really stays in its lane, the maximum deviation is about two or three inches or so from the center lane, and then it pulls over to the shoulder. This is not how humans handle them. Humans very often swerve across lanes and cause major accidents.
ME: How do the trucks navigate?
AW: We are talking about modularity. We have a computer that we can put into various trucks. We have three brands. But our mapping solution is different. Autonomous vehicles use high-definition maps that use lasers to create a model of the world, a very dense model. That works well in city environments. On long-haul transportation, the world changes very quickly We’ve built a different system to create a large map across the southern U.S., but scalable. It is fast to deploy and fast to update. Our control center in the truck does all the monitoring. All decisions are made by the onboard computer. Our trucks do not need any connectivity, they can completely run without a remote connection. The computer is the actuation computation engine. It is like an ECU that talks to the vehicle and is self-contained in the vehicle.
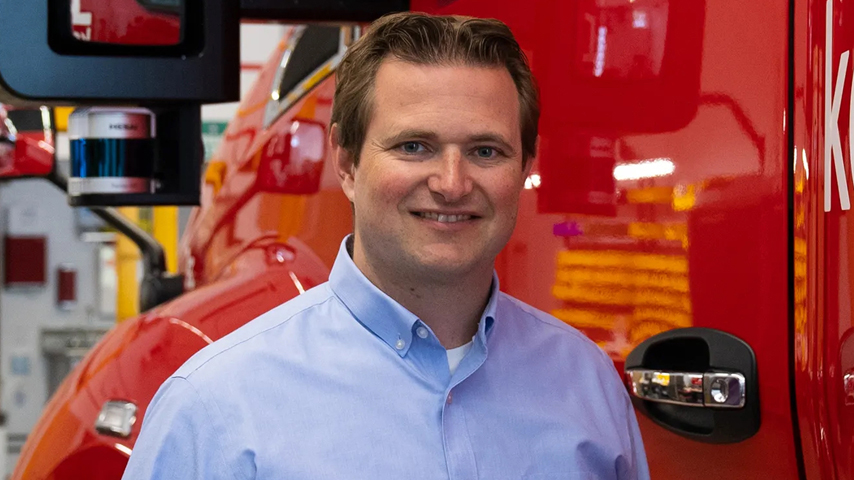
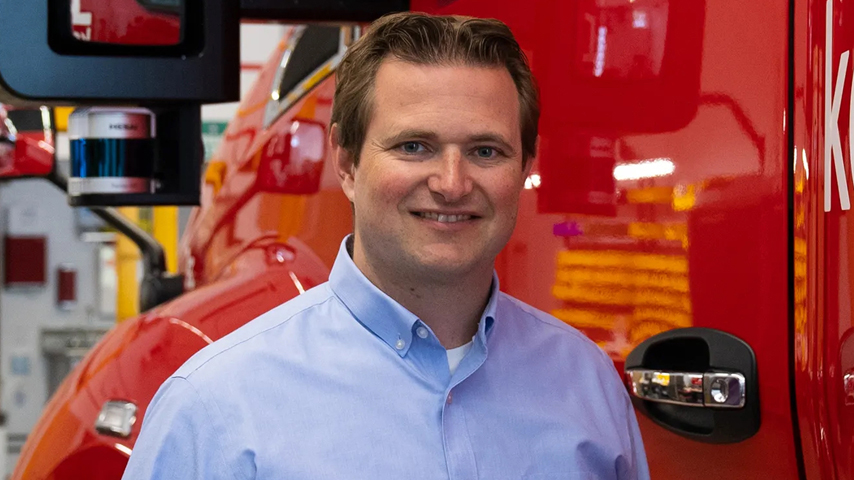