Wing Sails for Cargo Ships Pass First Test
Wing Sails for Cargo Ships Pass First Test
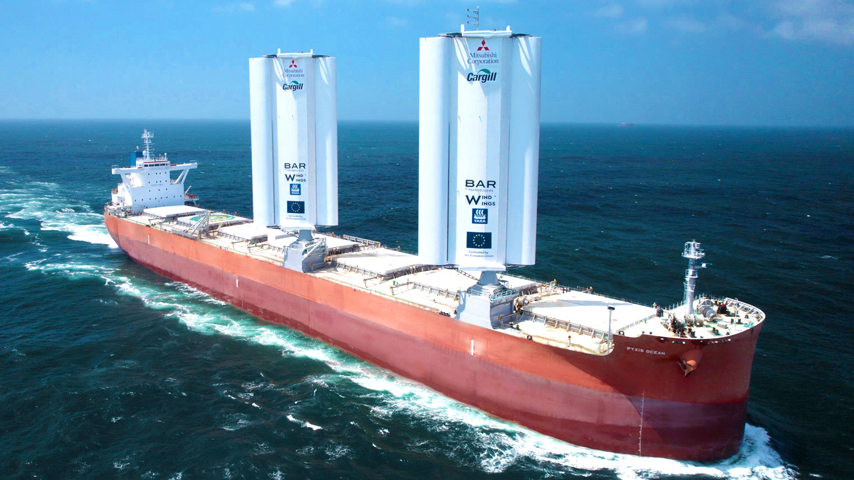
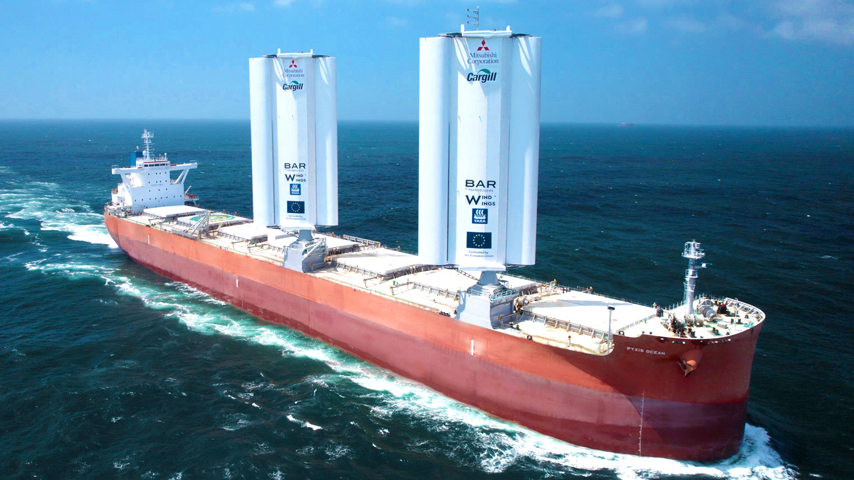
The shipping industry is set to save literally tons of fuel per day for any cargo ship outfitted with a new rigid sail.
International shipping accounts for around 5 percent of global petroleum demand—more than 300 million tons of fuel each year. That number is set to increase, since world trade reflects consumer demand for cheap goods manufactured in countries where costs are low. But a new piece of green engineering is poised to cut the fuel usage of any cargo ship by several tons a day.
The technology is new, but it’s also as old as seafaring: It’s a sail. But, unlike the billowing sheets of a schooner or clipper ship, this sail is rigid. And massive. And far better at using the wind than its cloth ancestors. For more than six months now, two vessels, Cargill’s Pyxis Ocean and Berge Bulk’s Berge Olympus, have been cruising the seas with the help of fixed wing sails.
BAR Technologies of Portsmouth, England, created the rigid sails, called WindWings. Each one is 37.5 meters tall and 20 meters wide and made of three elements that can move to produce a shape best suited to turning wind into forward motion.
“It’s like an airplane wing,” said Lauren Eatwell, the company’s head of engineering. “When it’s more cambered—when the slats come out for takeoff and landing—it gives a higher amount of thrust. And when it’s in flight it can retract those flaps, flatten out, and have less drag. And that’s the same way that we use our wings.”
Wing sails are familiar to anyone who watched recent America’s Cup competitions or other high-end sailing races. Rigid wings are more efficient than sails, as they do a better job at slicing through the air to create lift. In the case of wing sails, lift pulls the ship horizontally instead of the vertical lift produced by airplane wings.
BAR Technologies engineers tore through many iterations before settling on the final design of the WindWings, Eatwell said.
“If you look at a one element wing and say that’s level one of the coefficient of lift, then a two element wing has two times the thrust and two times the coefficient of lift, and a three element wing has two and a half times the coefficient of lift,” she said. “So, you get a really steep curve up to three elements.”
After that, there are diminishing returns: performance may increase with more elements, but the additional complexity and weight cancel out the benefits. And more wings eventually mean less space for cargo. “So that shaped the design,” Eatwell said.
To achieve the maximum amount of forward thrust, apparent wind direction and other data informs a software application that sets the configuration of the three wing elements automatically. BAR Technologies has also created routing software that provides optimized routes based on global weather forecasts. To minimize power consumption, the wings check their position against wind and other factors and adjust accordingly every 15 minutes. And when winds are too high—or when a vessel needs to duck under a bridge to get into port—the wings can fold down, flush with the upper deck.
Long before the WindWings had seen any real wind they had taken many a virtual journey. Using digital twins of vessels with WindWings, Eatwell and her colleagues put them through thousands of routes on the simulated seas based on 10 years’ worth of weather data. When the modeling was complete and the numbers crunched, they predicted that a cargo vessel could save 1.5 tons of fuel per wing per day.
“That’s kind of the key number that we lean on. And it’s averaged over different vessels, different routes, different weather, different seasons,” said Eatwell. When conditions are optimal that savings can go up as high as eight tons of fuel savings a day.
Discover the Benefits of ASME Membership
That’s the model, at least. How did the real-world trials of the WindWings compare to their digital twins?
“We’re seeing really great correlation between our simulated results and the measured independent analysis,” Eatwell said. “In fact, we are generally underpredicting the fuel savings from what we have actually seen.”
BAR Technologies designed the wings not as a prototype, but as a fully designed product that is ready to go once it has been tested. Now that that’s been done, the time has come to move goods with air.
“The next year is looking really bright for us,” Eatwell said. “We’re seeing exponential growth of interest and need in the market to get these. So essentially, we can’t produce them fast enough at the minute. But that's what we’re working on.”
Michael Abrams is a technology writer in Westfield, N.J.
The technology is new, but it’s also as old as seafaring: It’s a sail. But, unlike the billowing sheets of a schooner or clipper ship, this sail is rigid. And massive. And far better at using the wind than its cloth ancestors. For more than six months now, two vessels, Cargill’s Pyxis Ocean and Berge Bulk’s Berge Olympus, have been cruising the seas with the help of fixed wing sails.
BAR Technologies of Portsmouth, England, created the rigid sails, called WindWings. Each one is 37.5 meters tall and 20 meters wide and made of three elements that can move to produce a shape best suited to turning wind into forward motion.
“It’s like an airplane wing,” said Lauren Eatwell, the company’s head of engineering. “When it’s more cambered—when the slats come out for takeoff and landing—it gives a higher amount of thrust. And when it’s in flight it can retract those flaps, flatten out, and have less drag. And that’s the same way that we use our wings.”
Wing sails are familiar to anyone who watched recent America’s Cup competitions or other high-end sailing races. Rigid wings are more efficient than sails, as they do a better job at slicing through the air to create lift. In the case of wing sails, lift pulls the ship horizontally instead of the vertical lift produced by airplane wings.
BAR Technologies engineers tore through many iterations before settling on the final design of the WindWings, Eatwell said.
“If you look at a one element wing and say that’s level one of the coefficient of lift, then a two element wing has two times the thrust and two times the coefficient of lift, and a three element wing has two and a half times the coefficient of lift,” she said. “So, you get a really steep curve up to three elements.”
After that, there are diminishing returns: performance may increase with more elements, but the additional complexity and weight cancel out the benefits. And more wings eventually mean less space for cargo. “So that shaped the design,” Eatwell said.
To achieve the maximum amount of forward thrust, apparent wind direction and other data informs a software application that sets the configuration of the three wing elements automatically. BAR Technologies has also created routing software that provides optimized routes based on global weather forecasts. To minimize power consumption, the wings check their position against wind and other factors and adjust accordingly every 15 minutes. And when winds are too high—or when a vessel needs to duck under a bridge to get into port—the wings can fold down, flush with the upper deck.
Long before the WindWings had seen any real wind they had taken many a virtual journey. Using digital twins of vessels with WindWings, Eatwell and her colleagues put them through thousands of routes on the simulated seas based on 10 years’ worth of weather data. When the modeling was complete and the numbers crunched, they predicted that a cargo vessel could save 1.5 tons of fuel per wing per day.
“That’s kind of the key number that we lean on. And it’s averaged over different vessels, different routes, different weather, different seasons,” said Eatwell. When conditions are optimal that savings can go up as high as eight tons of fuel savings a day.
Discover the Benefits of ASME Membership
That’s the model, at least. How did the real-world trials of the WindWings compare to their digital twins?
“We’re seeing really great correlation between our simulated results and the measured independent analysis,” Eatwell said. “In fact, we are generally underpredicting the fuel savings from what we have actually seen.”
BAR Technologies designed the wings not as a prototype, but as a fully designed product that is ready to go once it has been tested. Now that that’s been done, the time has come to move goods with air.
“The next year is looking really bright for us,” Eatwell said. “We’re seeing exponential growth of interest and need in the market to get these. So essentially, we can’t produce them fast enough at the minute. But that's what we’re working on.”
Michael Abrams is a technology writer in Westfield, N.J.