7 Manufacturing Lessons from COVID-19
7 Manufacturing Lessons from COVID-19
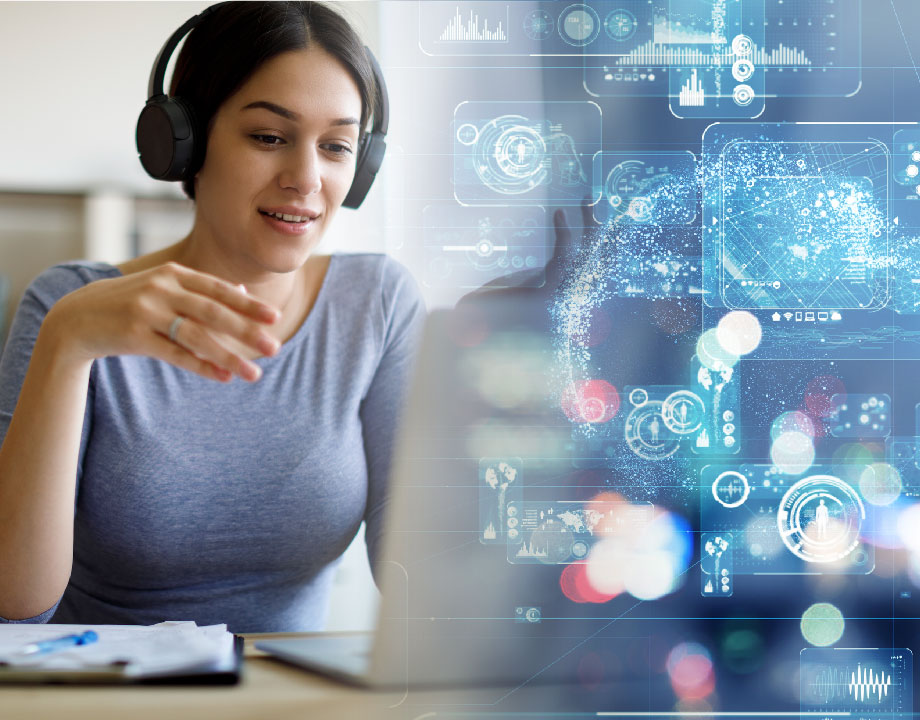
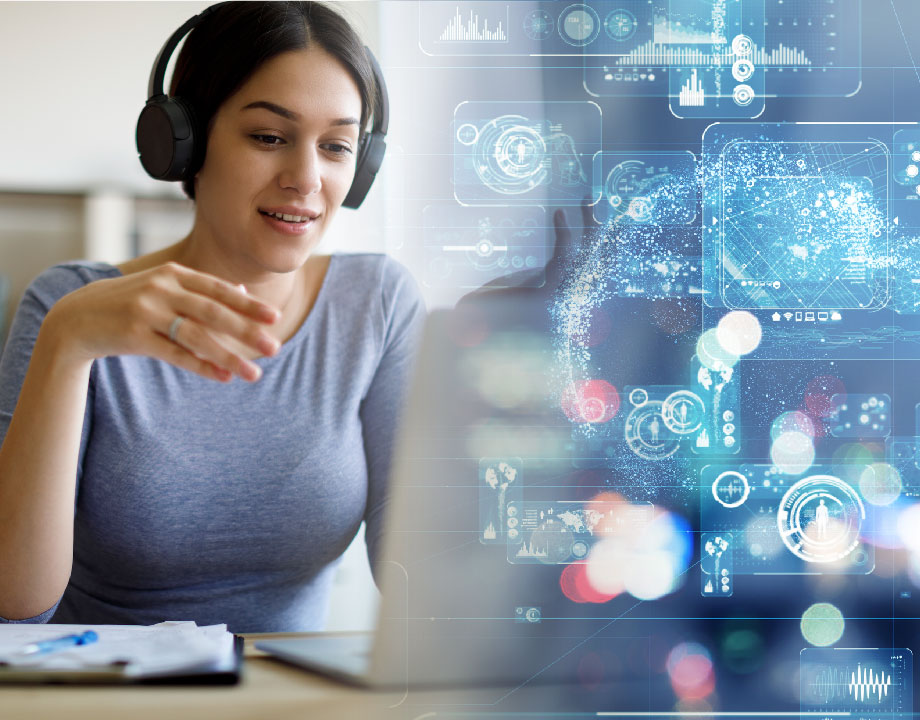
COVID-19 has disrupted manufacturing operations and their supply chains around the world. Here are seven lessons manufacturers have learned from dealing with COVID-19.
COVID-19 has disrupted manufacturing around the world on a huge scale, challenging manufacturers to find innovative new ways to continue their operations safely. This includes developing solutions to complex issues regarding workforce safety, supply chain maintenance, and deployment of new technologies.
Manufacturers realized early on that agility and resilience are key attributes to surviving, or even thriving, future disruptions, as well as simply taking advantage of changing consumer trends during normal times.
Below are seven lessons manufacturers have learned from dealing with COVID-19 that improve efficiency, productivity, and quality as well as reduce costs that will likely become part of daily operations:
To protect employees and meet social distancing protocols, many companies established remote working policies that enabled workers to work from home. This often proved to be an efficient and lower-cost approach that led to higher worker satisfaction. In fact, a recent Gartner survey of 317 CFOs and finance leaders revealed that nearly a quarter of respondents plan to move at least 20% of their on-site employees to permanent remote positions, primarily as a cost-saving measure.
On-site visits to customers are popular for building relationships and troubleshooting their issues, installing new equipment or upgrades, or training operators. Social distancing requirements made these visits impossible. However, various communication platforms are now being used to collaborate remotely in real-time. “We can show the customer the right tool, where it should touch, what to do next with it, and so on,” said Roel Rentmeesters, director of global customer service for Munters, an equipment manufacturer. “We use this for visual inspections, diagnosis, and even to provide direct solutions.”
Further Reading: Manufacturing Blog: Rebuilding the Medical Device Supply Chain
Many manufacturers had not developed relationships with back-up vendors and suppliers in the event of a major supply chain disruption when COVID 19 struck, creating huge delays with their primary vendors and suppliers. “Developing redundancy requires extra effort and cost, but the flexibility of digital manufacturing makes it easier to go to Plan B quickly in a way that is much, much more economical,” said Jennifer Pilat, vice president of strategy and engagement for MxD, a manufacturing support organization. And, when manufacturers embrace digital, they will find it is more practical to build products in “places that traditionally didn’t produce them,” she added—which can be geographically much closer, shortening the supply chain.
Cloud computing, data analytics, artificial intelligence, blockchain, and other emerging technologies are essential for quick innovation and product development. “Machine learning, coupled with big data, can rapidly identify promising links between manufacturing needs and solutions,” stated Georg von Krogh, professor of strategic management and innovation at ETH Zurich, in MIT Sloan Management Review. Virtual reality and augmented reality are also effective tools to reskill employees for new operations and job responsibilities.
Investing in automation and robotics was one way companies coped with the loss of workers. It helped improve worker safety, sped up operations, optimized product quality, and reduced operational costs. According to Forrester, many companies are planning to invest more in automation. “Robotics is key for repetitive work,” stated Mark Stevens, a manufacturing expert, and consultant with Wipfli. “Robots can complete quality control and auditing functions, taking note of dimensions and colors, and logging the information. Supply chain adjustments based on demand and production variability can also be automated.”
Forward-thinking companies will take these lessons and be ready to innovate quickly when market conditions change in the future. For example, Dyson, a household appliance manufacturer, rapidly adjusted its operations to produce ventilators using its air-compression technology. “The repurposing logic underlying these ultrafast innovation initiatives can be summarized in five principles: Grasp the innovation problem, map resources, use emerging technologies, encourage collaboration, and integrate end-users,” said von Krogh.
COVID-19 has already created positive changes for the future of manufacturing by forcing companies to invest in resources that build agility, responsiveness, and resilience into their manufacturing operations.
Editor’s Pick: Smarter Manufacturing after the COVID-19 Pandemic
“Manufacturers with digital platforms, accessible data, and advanced analytical capabilities will be able to respond more quickly, accurately, and successfully to COVID-19 disruptions,” according to Accenture, which provides business management and technology solutions for manufacturers. “All manufacturers need to look closely at their end-to-end operations to assess how well-positioned they are to respond to future disruptions with greater confidence and speed.”
Mark Crawford is a technology writer based in Corrales, N.M.
Manufacturers realized early on that agility and resilience are key attributes to surviving, or even thriving, future disruptions, as well as simply taking advantage of changing consumer trends during normal times.
Below are seven lessons manufacturers have learned from dealing with COVID-19 that improve efficiency, productivity, and quality as well as reduce costs that will likely become part of daily operations:
1. Remote Workforce
To protect employees and meet social distancing protocols, many companies established remote working policies that enabled workers to work from home. This often proved to be an efficient and lower-cost approach that led to higher worker satisfaction. In fact, a recent Gartner survey of 317 CFOs and finance leaders revealed that nearly a quarter of respondents plan to move at least 20% of their on-site employees to permanent remote positions, primarily as a cost-saving measure.
2. Remote Site Visits
On-site visits to customers are popular for building relationships and troubleshooting their issues, installing new equipment or upgrades, or training operators. Social distancing requirements made these visits impossible. However, various communication platforms are now being used to collaborate remotely in real-time. “We can show the customer the right tool, where it should touch, what to do next with it, and so on,” said Roel Rentmeesters, director of global customer service for Munters, an equipment manufacturer. “We use this for visual inspections, diagnosis, and even to provide direct solutions.”
Further Reading: Manufacturing Blog: Rebuilding the Medical Device Supply Chain
3. Build Redundancy into the Supply Chain
Many manufacturers had not developed relationships with back-up vendors and suppliers in the event of a major supply chain disruption when COVID 19 struck, creating huge delays with their primary vendors and suppliers. “Developing redundancy requires extra effort and cost, but the flexibility of digital manufacturing makes it easier to go to Plan B quickly in a way that is much, much more economical,” said Jennifer Pilat, vice president of strategy and engagement for MxD, a manufacturing support organization. And, when manufacturers embrace digital, they will find it is more practical to build products in “places that traditionally didn’t produce them,” she added—which can be geographically much closer, shortening the supply chain.
4. Create Transparency in the Supply Chain
Manufacturers typically lack complete visibility into all layers of their suppliers. By not being fully aware of their suppliers’ business practices, especially at the Tier-3 level, manufacturers can be caught by surprise during a major disruption when their supply chains malfunction and cannot correct themselves quickly. “By gaining visibility and transparency, manufacturers can begin to prioritize the automation of processes, including supply chain constraints, traceability, and quality management, that connects design and planning to production,” said Rene Wolf, senior vice president manufacturing operations management Software for Siemens.
5. Deploy Digital Technologies
Cloud computing, data analytics, artificial intelligence, blockchain, and other emerging technologies are essential for quick innovation and product development. “Machine learning, coupled with big data, can rapidly identify promising links between manufacturing needs and solutions,” stated Georg von Krogh, professor of strategic management and innovation at ETH Zurich, in MIT Sloan Management Review. Virtual reality and augmented reality are also effective tools to reskill employees for new operations and job responsibilities.
Recommended for You: Robotics Blog: Making Robots Ubiquitous Post-Pandemic
6. Increase Automation
Investing in automation and robotics was one way companies coped with the loss of workers. It helped improve worker safety, sped up operations, optimized product quality, and reduced operational costs. According to Forrester, many companies are planning to invest more in automation. “Robotics is key for repetitive work,” stated Mark Stevens, a manufacturing expert, and consultant with Wipfli. “Robots can complete quality control and auditing functions, taking note of dimensions and colors, and logging the information. Supply chain adjustments based on demand and production variability can also be automated.”
7. Be Ready to Innovate
Forward-thinking companies will take these lessons and be ready to innovate quickly when market conditions change in the future. For example, Dyson, a household appliance manufacturer, rapidly adjusted its operations to produce ventilators using its air-compression technology. “The repurposing logic underlying these ultrafast innovation initiatives can be summarized in five principles: Grasp the innovation problem, map resources, use emerging technologies, encourage collaboration, and integrate end-users,” said von Krogh.
Going Forward
COVID-19 has already created positive changes for the future of manufacturing by forcing companies to invest in resources that build agility, responsiveness, and resilience into their manufacturing operations.
Editor’s Pick: Smarter Manufacturing after the COVID-19 Pandemic
“Manufacturers with digital platforms, accessible data, and advanced analytical capabilities will be able to respond more quickly, accurately, and successfully to COVID-19 disruptions,” according to Accenture, which provides business management and technology solutions for manufacturers. “All manufacturers need to look closely at their end-to-end operations to assess how well-positioned they are to respond to future disruptions with greater confidence and speed.”
Mark Crawford is a technology writer based in Corrales, N.M.
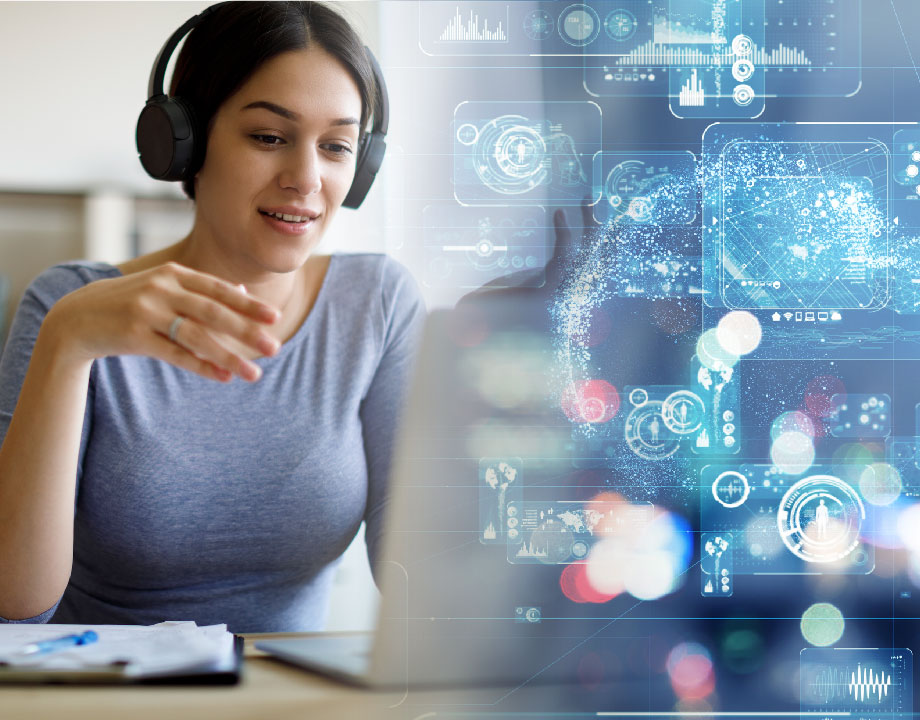
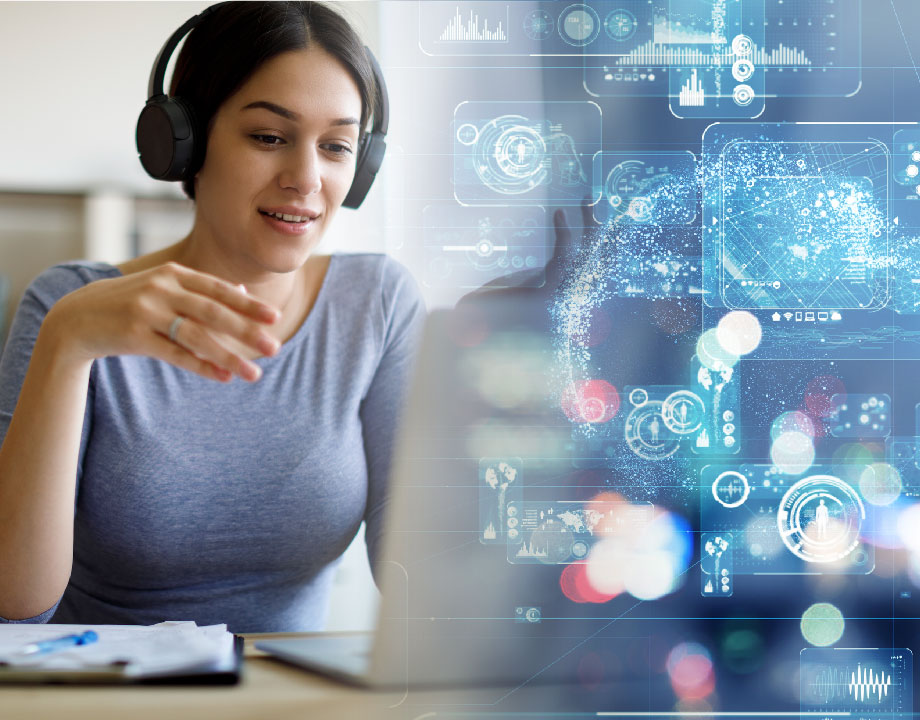