Fly the Climate-Friendly Skies
Fly the Climate-Friendly Skies
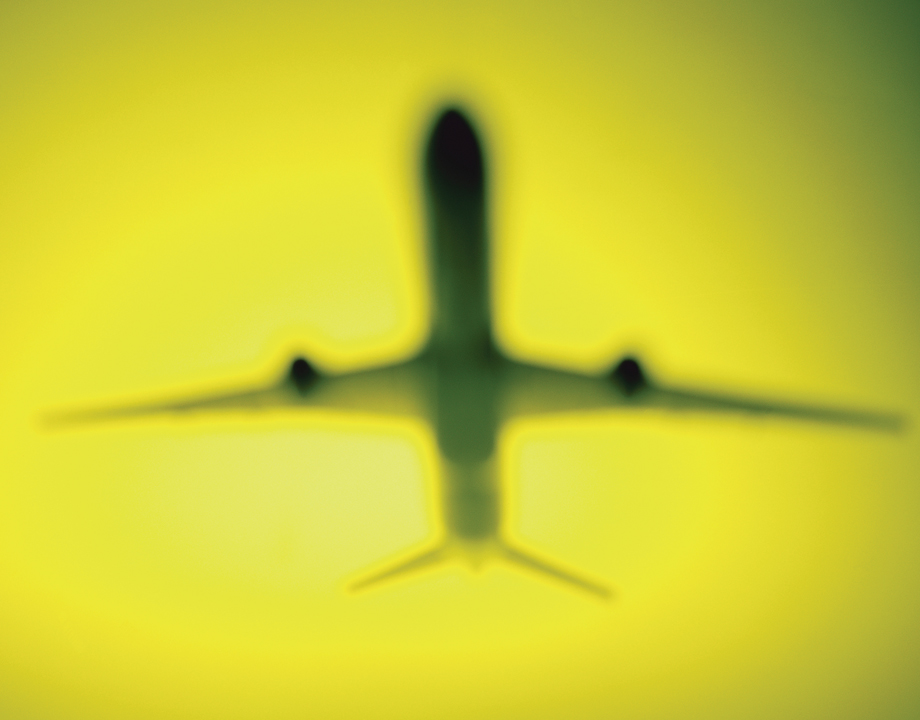
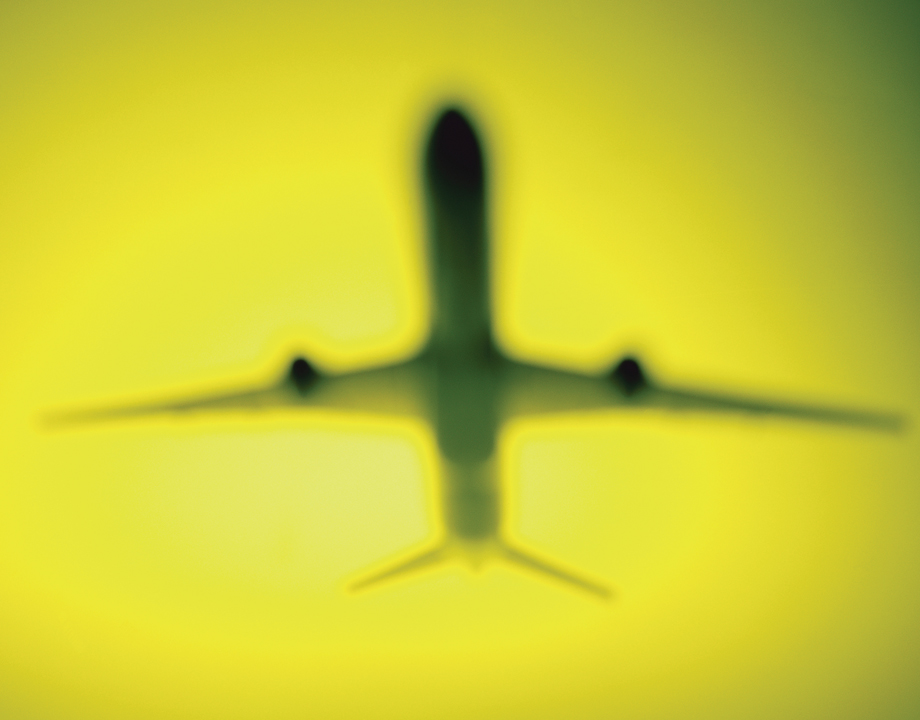
Scientists, engineers, and airlines agree that aviation carbon emissions are a problem. Several efforts aim at delivering a solution.
Almost every transcontinental traveler has sat in a jumbo Boeing or Airbus jetliner, waiting impatiently for a long-haul flight to (finally) take off. Next time, instead of checking the time again or thumbing through the in-flight magazine once more, look across the tarmac at the other planes in the queue for takeoff and appreciate the concentrated power that represents.
“It takes an enormous amount of energy and power to push half a million pounds across the planet at Mach 0.8,” said Alan Epstein, a professor of aeronautics and astronautics at the Massachusetts Institute of Technology. “If you are ever at a big airport and there are three 747s ahead of you, the power is a nuclear power plant.”
That power, while necessary to cross the Atlantic overnight, presents a problem. To run the two or four giant gas turbines hanging from each wing of a modern jetliner, aeronautical engineers have opted for a mixture of kerosene and other liquid hydrocarbons that provide the ideal combination of energy density by weight and volume. The engines burn that fuel so quickly that the carbon emissions are significant. To fly a family of four from New York to San Francisco and back produces 5.6 tons of carbon dioxide. Driving a typical American car for a year emits 4.6 tons, according to the Environmental Protection Agency. In fact, a full 10 percent of the carbon impact of transportation—now the largest sector of emissions—comes from aviation.
Eliminating that impact will require cutting fossil carbon from the aviation energy supply. Startups and established companies are scrambling to develop new energy technologies that would allow airlines and their passengers to fly the globe without contributing to its warming. There is, however, no consensus on the best way this can be accomplished.
The unexpectedly fast rise in electric vehicle adoption—EV sales in the United States jumped by an astonishing 66 percent in the second quarter of 2022, compared to the second quarter of 2021—has prompted a sudden interest in battery-powered aviation.
Some of that is due to recent advances in performance. In November 2021, Rolls-Royce’s Spirit of Innovation became the world’s fastest electric vehicle, hitting 345 miles per hour during a flight. And in May 2022, the battery-powered Alia from Beta Technologies made a 7-stop 1,403-mile jaunt. Those successes are enough to prompt United Airlines to buy 100 electric 19-seater planes from Swedish startup Heart Aerospace, with the intention of having them flying by 2026, and for Norway to announce plans to have electric planes flying domestically that same year.
Regardless, battery-powered flight has some major obstacles.
“The energy-to-weight ratio of batteries is the main bottleneck for electric flight,” said Gökçin Çınar, a professor of aerospace engineering at the University of Michigan, and principal investigator of the Integrated Design of Environmentally Friendly Aerospace Systems Lab. “It’s just so heavy to carry a battery—you fly for an hour and it’s only you on board, maybe just the pilot.”
Many short routes were once served by small, turboprop-powered planes before the advent of regional jets. But servicing those routes with small, electric aircraft would make only a tiny dent in aviation emissions. Around 96 percent of carbon emissions from aviation come from the large jet class of airplanes—those flying 100 or more passengers. For aircraft that size, it’s unlikely that a battery is going to make sense any time soon.
“It demands a Nobel Prize-worthy chemistry discovery, which could happen at any time—or never,” said Epstein, who co-authored “The Challenges and Opportunities of Battery-Powered Flight,” published in Nature in March 2022.
But even with that revolutionary battery in hand, the case for electrifying jumbo jets is hard to pencil out. The engines on a long-haul flight at cruising altitude are remarkably efficient, so the only way that electrifying that flight would cut carbon emissions is if the plane’s batteries were recharged with wind or solar power. That would push renewable electricity to the extreme.
“If you want to use solar to power flights out of JFK, you’ll have to cover 20 percent of Long Island with solar cells,” Epstein said. Planes that currently have a turnaround time of half an hour or so would have to sit around charging for half the day.
“Since there is a great demand for green power, if the world were rational, you would first use it to electrify ground transportation and buildings,” Epstein said. “The last thing you would electrify would be the most efficient use of fossil fuels: airplanes.”
“100 percent electric-powered aircraft, for bigger commercial planes—it’s not possible today,” Çınar said. “That’s why we’re looking at hybrids, where you use batteries as well as fossil fuel or any other fuel source. It’s viable today.” Indeed, companies such as Rolls-Royce (which demonstrated a megawatt-scale generator for aircraft use in December), Pipistrel, and Siemens have hybrid concepts in the works.
“According to my analysis, it’s possible to hybridize aircraft—around the 50-passenger size—for their original range without sacrificing range and payload,” Çınar said. A battery for such a plane could be smaller as it would assist only with take-off and climbing and could even charge during the cruise phase of a flight.
That kind of configuration would shave a good five to ten percent off fuel burn, but 50-seat aircraft are not the ones producing most of the aviation sectors carbon emissions, and batteries are still too heavy for hybrid-electric jumbo jets to make sense.
If the problem with batteries is that they are heavy, some companies believe the solution comes from the lightest element: hydrogen. In 2020, for example, Airbus introduced a suite of “ZEROe” hydrogen-fueled aircraft concepts, ranging from a turboprop design that would haul up to 100 passengers to a “blended wing body” with a fat fuselage capable of carrying plenty of hydrogen as well as 200 passengers. The company hopes to have one fly for demonstration by 2035.
“For now, there is no front runner. All of the studies are progressing well, and we are not in a position to communicate on which concept is the most promising,” said Stephane Azam, ZEROe H2 Combustion program manager at Airbus in Toulouse, France. “The main challenge will be to certify them for airworthiness.”
That certification is not nearly as difficult as the association of hydrogen with the Hindenburg disaster might imply. Hydrogen, as Azam points out, is “no more or less dangerous than other fuels, including gasoline and natural gas.” Lighter than air, hydrogen leaks dissipate quickly and have less time to burn. Hydrogen is also easy to detect—sensors will allow any area to be ventilated long before the gas reaches inflammable concentrations. The gas is now routinely handled without incident in oil refineries, in the production of ammonia, and as a part of rocket fuel.
“With the massive cross-industry experience of handling hydrogen, we see the safety targets as being fully achievable,” Azam said.
Demonstrating that a hydrogen-powered aircraft can fly safely might be the easiest part of creating a H2-burning fleet. Unlike electricity, which is supplied at every airport today, the hydrogen infrastructure would need to be built from scratch.
More about Green Hydrogen: What Color is Your Hydrogen?
“I’m willing to bet you lunch money that the societal costs associated with enabling hydrogen to be a primary power source on aircraft are even worse than simply being able to get an airplane to burn hydrogen in the first place,” said Steve Csonka, executive director of the Commercial Aviation Alternative Fuels Initiative.
To get a hydrogen-fueled aircraft fleet up and flying before the establishment of the needed pipelines and airport-based storage tanks, Hawthorne, Calif.-based Universal Hydrogen is developing a hydrogen delivery service. “Hydrogen can be produced near sources of renewable energy and then stored in capsules,” said Mark Cousin, the company’s chief technology officer. Those capsules would then be trucked to airports and loaded onto hydrogen-burning planes. The capsules are double jacketed with a vacuum chamber—the insulation prevents any venting and keeps liquid hydrogen cold for days without additional energy input.
Listen to Our Podcast: The Promise of Hydrogen
Universal Hydrogen is also producing a fuel cell powertrain to retrofit existing aircraft. “The cost of converting to hydrogen is a bit more expensive than overhauling the gas turbine, but significantly less expensive than a new airplane,” Cousin said.
The company plans to fly a prototype this year and have it certified by 2025. It already has signed letters of intent from several airlines for the conversion of more than 100 planes.
“We are really looking forward to demonstrating to airlines and customers that this is not science fiction,” Cousin said. “It’s feasible in this decade and doesn’t require us to invent something completely new to achieve decarbonization of the aviation industry.”
Csonka, though, is not convinced. Forget the logistics of truck-based delivery or the robustness aviation-grade fuel cells. “Just the liquification of the hydrogen—not even its production—is beyond anyone’s conception,” Csonka said. “The power required to liquefy the hydrogen needed to supplant the jet fuel usage at a major airport like Paris is greater than the output of the largest nuclear power plant in the world. These are extremely daunting challenges that extend beyond proof of concept.”
Csonka, it should be noted, is not a wholly disinterested party. He and his colleagues at the Commercial Aviation Alternative Fuels Initiative are working to meet the goals of the Sustainable Aviation Fuel Grand Challenge, an effort by the U.S. Departments of Energy, Transportation, and Agriculture to get the world’s fleet of airplanes running on 100 percent sustainable aviation fuels, or SAFs, by the year 2050. SAFs are made from a variety of biologically derived sources—agricultural waste, sewage, cooking oil.
Unlike battery- or hydrogen-powered airliners, which remain mostly on the drawing board for now, SAFs exist today. Dozens of airlines have used a mix of 50 percent SAF and 50 percent jet fuel to power some 370,000 flights. The top 10 airlines have made formal commitments to meeting the goal of running their fleets on SAFs.
Their seriousness is reflected in their purchasing power: all the extant SAF, and all SAF likely to be produced in the near future, has been sold.
“The next eight or nine facilities have their full production slate spoken for in offtake agreements, and they haven’t even started to move dirt yet,” Csonka said.
Watch the Video: Electric Aircraft
While making jet fuel from used French fry cooking oil is straightforward, it isn’t cheap. According to GlobalAir, an online aviation fuel tracker, SAFs averaged between $7 and $8.50 a gallon at the airports where it could be found in July 2022. That’s usually twice as much as jet fuel (early this summer a shortage caused jet fuel prices to soar past $7 a gallon), but the thinking is that as more SAF-producing facilities come online, as the use of renewable fuels becomes routine, and as governments add incentives to wean the aviation industry off fossil fuels, the cost of SAFs will come down and reach parity with petroleum-derived jet fuel.
At cost parity, there’s not much of a reason for an airline not to turn to SAFs. One of their chief attractions is that they can run in existing planes. At the moment, though, jet engines can’t handle more than the 50 percent blend. Elastomeric seals require chemical components in the kerosene to maintain their size. With some 100 percent SAF mixtures, those seals could shrink, and create fuel seeping issues. This could potentially be solved with an additive, however, and newer aircraft are produced using different seals.
Check Out Our Infographic: The Biofuel Belt
It sounds like a solution, but there’s no guarantee that SAFs will be able to scale fast enough. Simply meeting the short-term goal of the Grand Challenge—3 billion gallons of SAF by 2030—will require an order of magnitude more production than existing facilities are able to produce. While current waste streams could provide enough raw material to produce enough SAF to cover 70 percent of industry needs, going to 100 percent renewable fuel would require growing crops specifically to feed the fuel factories. In a world of food scarcity, are SAFs that require their own crops actually sustainable?
Learn More about ASME Membership
So, renewable jet fuel can be made. As Epstein quipped, “Chemical engineers can make almost anything from anything else. The question is, How much energy does it take? And how much capital?” But if SAFs or batteries or hydrogen can’t provide the energy large aircraft need—on a global scale, at a reasonable cost, and without unintended consequences—then they won’t be able to displace the petroleum-derived fuel that the aviation industry relies on.
As much as the fight against climate change depends on reducing aviation emissions, none of the potential solutions have been cleared for takeoff.
Michael Abrams is a science and technology writer in Westfield, N.J.
“It takes an enormous amount of energy and power to push half a million pounds across the planet at Mach 0.8,” said Alan Epstein, a professor of aeronautics and astronautics at the Massachusetts Institute of Technology. “If you are ever at a big airport and there are three 747s ahead of you, the power is a nuclear power plant.”
That power, while necessary to cross the Atlantic overnight, presents a problem. To run the two or four giant gas turbines hanging from each wing of a modern jetliner, aeronautical engineers have opted for a mixture of kerosene and other liquid hydrocarbons that provide the ideal combination of energy density by weight and volume. The engines burn that fuel so quickly that the carbon emissions are significant. To fly a family of four from New York to San Francisco and back produces 5.6 tons of carbon dioxide. Driving a typical American car for a year emits 4.6 tons, according to the Environmental Protection Agency. In fact, a full 10 percent of the carbon impact of transportation—now the largest sector of emissions—comes from aviation.
Eliminating that impact will require cutting fossil carbon from the aviation energy supply. Startups and established companies are scrambling to develop new energy technologies that would allow airlines and their passengers to fly the globe without contributing to its warming. There is, however, no consensus on the best way this can be accomplished.
Electric Flights
The unexpectedly fast rise in electric vehicle adoption—EV sales in the United States jumped by an astonishing 66 percent in the second quarter of 2022, compared to the second quarter of 2021—has prompted a sudden interest in battery-powered aviation.
Some of that is due to recent advances in performance. In November 2021, Rolls-Royce’s Spirit of Innovation became the world’s fastest electric vehicle, hitting 345 miles per hour during a flight. And in May 2022, the battery-powered Alia from Beta Technologies made a 7-stop 1,403-mile jaunt. Those successes are enough to prompt United Airlines to buy 100 electric 19-seater planes from Swedish startup Heart Aerospace, with the intention of having them flying by 2026, and for Norway to announce plans to have electric planes flying domestically that same year.
Regardless, battery-powered flight has some major obstacles.
“The energy-to-weight ratio of batteries is the main bottleneck for electric flight,” said Gökçin Çınar, a professor of aerospace engineering at the University of Michigan, and principal investigator of the Integrated Design of Environmentally Friendly Aerospace Systems Lab. “It’s just so heavy to carry a battery—you fly for an hour and it’s only you on board, maybe just the pilot.”
Many short routes were once served by small, turboprop-powered planes before the advent of regional jets. But servicing those routes with small, electric aircraft would make only a tiny dent in aviation emissions. Around 96 percent of carbon emissions from aviation come from the large jet class of airplanes—those flying 100 or more passengers. For aircraft that size, it’s unlikely that a battery is going to make sense any time soon.
“It demands a Nobel Prize-worthy chemistry discovery, which could happen at any time—or never,” said Epstein, who co-authored “The Challenges and Opportunities of Battery-Powered Flight,” published in Nature in March 2022.
But even with that revolutionary battery in hand, the case for electrifying jumbo jets is hard to pencil out. The engines on a long-haul flight at cruising altitude are remarkably efficient, so the only way that electrifying that flight would cut carbon emissions is if the plane’s batteries were recharged with wind or solar power. That would push renewable electricity to the extreme.
“If you want to use solar to power flights out of JFK, you’ll have to cover 20 percent of Long Island with solar cells,” Epstein said. Planes that currently have a turnaround time of half an hour or so would have to sit around charging for half the day.
“Since there is a great demand for green power, if the world were rational, you would first use it to electrify ground transportation and buildings,” Epstein said. “The last thing you would electrify would be the most efficient use of fossil fuels: airplanes.”
“100 percent electric-powered aircraft, for bigger commercial planes—it’s not possible today,” Çınar said. “That’s why we’re looking at hybrids, where you use batteries as well as fossil fuel or any other fuel source. It’s viable today.” Indeed, companies such as Rolls-Royce (which demonstrated a megawatt-scale generator for aircraft use in December), Pipistrel, and Siemens have hybrid concepts in the works.
“According to my analysis, it’s possible to hybridize aircraft—around the 50-passenger size—for their original range without sacrificing range and payload,” Çınar said. A battery for such a plane could be smaller as it would assist only with take-off and climbing and could even charge during the cruise phase of a flight.
That kind of configuration would shave a good five to ten percent off fuel burn, but 50-seat aircraft are not the ones producing most of the aviation sectors carbon emissions, and batteries are still too heavy for hybrid-electric jumbo jets to make sense.
Hy Hopes
If the problem with batteries is that they are heavy, some companies believe the solution comes from the lightest element: hydrogen. In 2020, for example, Airbus introduced a suite of “ZEROe” hydrogen-fueled aircraft concepts, ranging from a turboprop design that would haul up to 100 passengers to a “blended wing body” with a fat fuselage capable of carrying plenty of hydrogen as well as 200 passengers. The company hopes to have one fly for demonstration by 2035.
“For now, there is no front runner. All of the studies are progressing well, and we are not in a position to communicate on which concept is the most promising,” said Stephane Azam, ZEROe H2 Combustion program manager at Airbus in Toulouse, France. “The main challenge will be to certify them for airworthiness.”
That certification is not nearly as difficult as the association of hydrogen with the Hindenburg disaster might imply. Hydrogen, as Azam points out, is “no more or less dangerous than other fuels, including gasoline and natural gas.” Lighter than air, hydrogen leaks dissipate quickly and have less time to burn. Hydrogen is also easy to detect—sensors will allow any area to be ventilated long before the gas reaches inflammable concentrations. The gas is now routinely handled without incident in oil refineries, in the production of ammonia, and as a part of rocket fuel.
“With the massive cross-industry experience of handling hydrogen, we see the safety targets as being fully achievable,” Azam said.
Demonstrating that a hydrogen-powered aircraft can fly safely might be the easiest part of creating a H2-burning fleet. Unlike electricity, which is supplied at every airport today, the hydrogen infrastructure would need to be built from scratch.
More about Green Hydrogen: What Color is Your Hydrogen?
“I’m willing to bet you lunch money that the societal costs associated with enabling hydrogen to be a primary power source on aircraft are even worse than simply being able to get an airplane to burn hydrogen in the first place,” said Steve Csonka, executive director of the Commercial Aviation Alternative Fuels Initiative.
To get a hydrogen-fueled aircraft fleet up and flying before the establishment of the needed pipelines and airport-based storage tanks, Hawthorne, Calif.-based Universal Hydrogen is developing a hydrogen delivery service. “Hydrogen can be produced near sources of renewable energy and then stored in capsules,” said Mark Cousin, the company’s chief technology officer. Those capsules would then be trucked to airports and loaded onto hydrogen-burning planes. The capsules are double jacketed with a vacuum chamber—the insulation prevents any venting and keeps liquid hydrogen cold for days without additional energy input.
Listen to Our Podcast: The Promise of Hydrogen
Universal Hydrogen is also producing a fuel cell powertrain to retrofit existing aircraft. “The cost of converting to hydrogen is a bit more expensive than overhauling the gas turbine, but significantly less expensive than a new airplane,” Cousin said.
The company plans to fly a prototype this year and have it certified by 2025. It already has signed letters of intent from several airlines for the conversion of more than 100 planes.
“We are really looking forward to demonstrating to airlines and customers that this is not science fiction,” Cousin said. “It’s feasible in this decade and doesn’t require us to invent something completely new to achieve decarbonization of the aviation industry.”
Csonka, though, is not convinced. Forget the logistics of truck-based delivery or the robustness aviation-grade fuel cells. “Just the liquification of the hydrogen—not even its production—is beyond anyone’s conception,” Csonka said. “The power required to liquefy the hydrogen needed to supplant the jet fuel usage at a major airport like Paris is greater than the output of the largest nuclear power plant in the world. These are extremely daunting challenges that extend beyond proof of concept.”
Glide Path
Csonka, it should be noted, is not a wholly disinterested party. He and his colleagues at the Commercial Aviation Alternative Fuels Initiative are working to meet the goals of the Sustainable Aviation Fuel Grand Challenge, an effort by the U.S. Departments of Energy, Transportation, and Agriculture to get the world’s fleet of airplanes running on 100 percent sustainable aviation fuels, or SAFs, by the year 2050. SAFs are made from a variety of biologically derived sources—agricultural waste, sewage, cooking oil.
Unlike battery- or hydrogen-powered airliners, which remain mostly on the drawing board for now, SAFs exist today. Dozens of airlines have used a mix of 50 percent SAF and 50 percent jet fuel to power some 370,000 flights. The top 10 airlines have made formal commitments to meeting the goal of running their fleets on SAFs.
Their seriousness is reflected in their purchasing power: all the extant SAF, and all SAF likely to be produced in the near future, has been sold.
“The next eight or nine facilities have their full production slate spoken for in offtake agreements, and they haven’t even started to move dirt yet,” Csonka said.
Watch the Video: Electric Aircraft
While making jet fuel from used French fry cooking oil is straightforward, it isn’t cheap. According to GlobalAir, an online aviation fuel tracker, SAFs averaged between $7 and $8.50 a gallon at the airports where it could be found in July 2022. That’s usually twice as much as jet fuel (early this summer a shortage caused jet fuel prices to soar past $7 a gallon), but the thinking is that as more SAF-producing facilities come online, as the use of renewable fuels becomes routine, and as governments add incentives to wean the aviation industry off fossil fuels, the cost of SAFs will come down and reach parity with petroleum-derived jet fuel.
At cost parity, there’s not much of a reason for an airline not to turn to SAFs. One of their chief attractions is that they can run in existing planes. At the moment, though, jet engines can’t handle more than the 50 percent blend. Elastomeric seals require chemical components in the kerosene to maintain their size. With some 100 percent SAF mixtures, those seals could shrink, and create fuel seeping issues. This could potentially be solved with an additive, however, and newer aircraft are produced using different seals.
Check Out Our Infographic: The Biofuel Belt
It sounds like a solution, but there’s no guarantee that SAFs will be able to scale fast enough. Simply meeting the short-term goal of the Grand Challenge—3 billion gallons of SAF by 2030—will require an order of magnitude more production than existing facilities are able to produce. While current waste streams could provide enough raw material to produce enough SAF to cover 70 percent of industry needs, going to 100 percent renewable fuel would require growing crops specifically to feed the fuel factories. In a world of food scarcity, are SAFs that require their own crops actually sustainable?
Learn More about ASME Membership
So, renewable jet fuel can be made. As Epstein quipped, “Chemical engineers can make almost anything from anything else. The question is, How much energy does it take? And how much capital?” But if SAFs or batteries or hydrogen can’t provide the energy large aircraft need—on a global scale, at a reasonable cost, and without unintended consequences—then they won’t be able to displace the petroleum-derived fuel that the aviation industry relies on.
As much as the fight against climate change depends on reducing aviation emissions, none of the potential solutions have been cleared for takeoff.
Michael Abrams is a science and technology writer in Westfield, N.J.
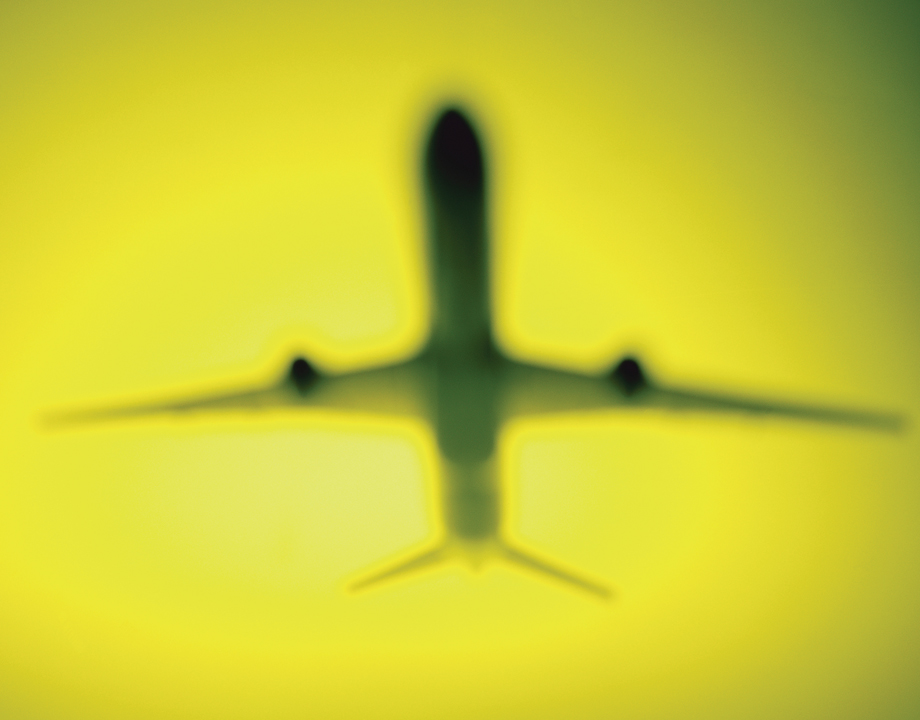
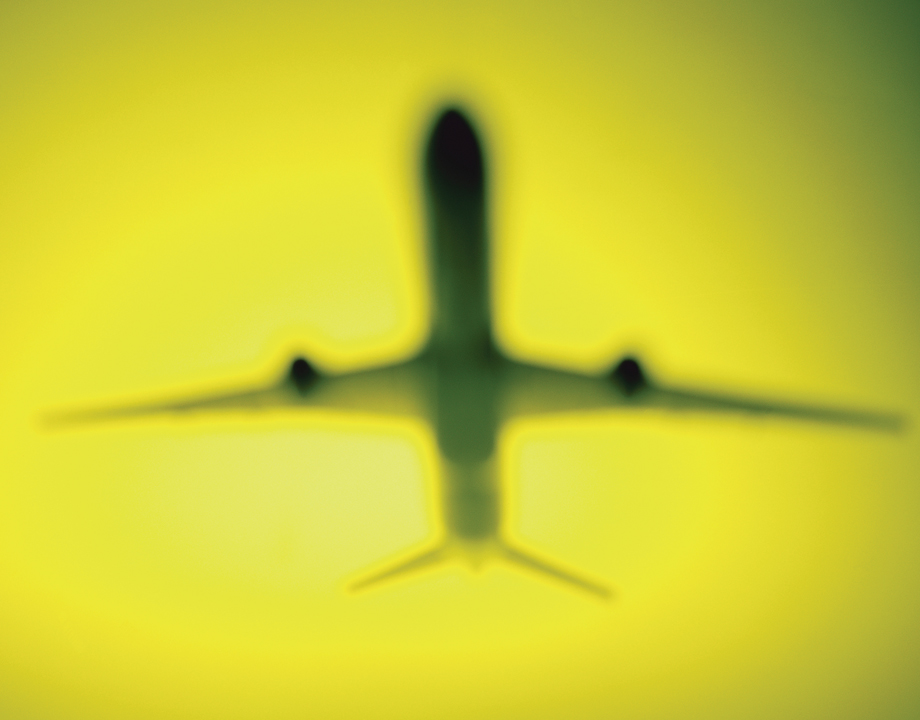