How Industry 4.0 Impacts Engineering Design
How Industry 4.0 Impacts Engineering Design
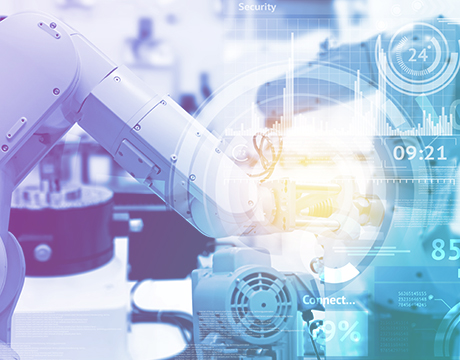
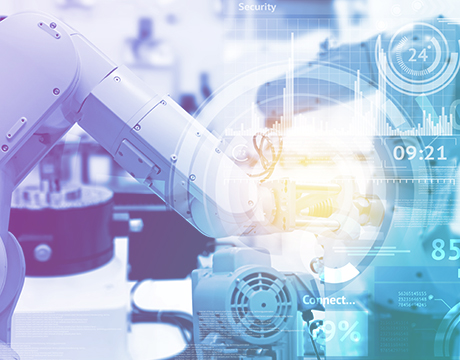
Industry 4.0—the combination of digital processes such as the Internet of Things, automation, robotics, and additive manufacturing—has a disruptive impact on mechanical engineering design. Not only do engineers need to redesign processes and operations to accommodate these new advances, Industry 4.0 impacts how they design products for increasingly smart manufacturing facilities.
As Industry 4.0 takes hold, forward-thinking engineers will embrace these digital tools and technologies. This allows them to make higher-quality products more efficiently and react more quickly to shifting consumer demands, building customer loyalty and gaining market share. Millennials, for example, are a rapidly growing population that expects tailored products that match their personal preferences.
Brands that offer personalized products typically enjoy a 50 percent higher loyalty rate. Unfortunately, traditional manufacturing methods are designed for mass production, not customization. Companies that can rapidly adapt production lines to exploit consumer trends are more likely to have implemented Industry 4.0. This is confirmed by a 2016 McKinsey and Company study that showed Industry 4.0 factories are better at designing and manufacturing individualized products than traditional factories.
What Drives Industry 4.0
The following technologies are typically considered key components of Industry 4.0:
- Internet of Things—uses sensor technology to connect the entire manufacturing ecosystem with real-time communication and data from interconnected machines and devices, tracking operational performance
- Big data and analytics—utilizes the Internet of Things to capture, analyze, and store data on every stage of production, from design through production
- Engineering simulation—relies on virtual reality and augmented reality to create realistic, perfectly scaled, three-dimensional images or holograms that speed up product design, reduce iterations, and shorten time to market
- Additive manufacturing, including 3D and 4D printing—these rapidly-advancing technologies allow engineers to design and manufacture products that often cannot be made using traditional manufacturing methods
Each of these Industry 4.0 components has big impacts on engineering design.
For You: Filling the Talent Gap
For example, with the Internet of Things, data can be used to optimize manufacturing processes, often through engineering adjustments. Robotics and automation, also key Industry 4.0 technologies, need to be integrated into manufacturing equipment, often in the form of added material-handling features. Data-collection features such as RFID can also be designed into parts and products.
“There will be more consideration for automation and modularity, both for parts and assemblies, and for the machines making and handling them,” says mechanical engineer Betsy Megas on Quara.com. “Manufacturing capabilities, and the rules around design for manufacture and design for assembly, will continue to evolve.”
Prototyping
Quick, production-ready prototypes are essential for efficient manufacturing and speed to market. Modeling/simulation scenarios early in the design process help determine the best possible design for prototyping. Virtual reality and augmented reality programs are rapidly becoming potent visualization and design tools, especially in medical R&D. For example, Stryker, an orthopedic implant manufacturer, is using Microsoft’s HaloLens holographic technology to design the operating room of the future, along with the necessary tools and instruments.
3D printing and other additive manufacturing (AM) technologies can prototype production-ready parts within a matter of hours, giving engineers a part they can hold and examine and even reiterate in the same day. An increasing number of complex products can only be made through additive manufacturing. Therefore it is essential for engineers to fully understand the capabilities these machines provide, which also continually evolve.
For example, Caterpillar trains its engineers in its own “AM Factory,” which is stocked with the latest AM equipment. Engineering teams learn how to apply 3D printing to new products, the supply chain, and even operations (for example, making parts and fixtures for their manufacturing equipment). Much of their product research and development is carried out in this facility.
“Designing for AM is where we will see huge advances in manufacturing technology,” says Stacey DelVecchio, additive manufacturing product manager for Caterpillar in Mossville, Ill. “Manufacturing companies have spent years training people to design for manufacturability. That means we have parts that are limited by how we traditionally manufacture them. At Caterpillar, we are removing these boundaries from our engineers. Having the capability to design what could never be made before, with features we didn’t think were feasible, is tremendously exciting.”
Data-Driven
When companies embrace Industry 4.0, they must also embrace big data and analytics. This sometimes requires hiring their own data-management scientists. Big data is essential for optimizing performance at every stage of development, from design through production. Performance data from the end-use environment can also lead to engineering design changes for future versions. Big data is also needed to identify and analyze consumer trends, which can directly impact what engineers make, and how they make them.
Smaller companies can buy data studies; larger companies can use the Internet of Things to collect their own data and identify trends to deliver better customer experiences. “Internet of Things data by itself, however, is not always useful,” comments Jesper Grode, director of product strategy with Stibo Systems, a provider of customer management solutions. “Only when combined with other data, such as product master data, customer master data, or location master data, will a better understanding of how products are being used ascend—thereby paving the way for improvements.”
Mark Crawford is an independent writer.
Read More:
Artificial Intelligence Transforms Manufacturing
Ultrasound Patch Monitors Critical Components
The Blockchain Gang
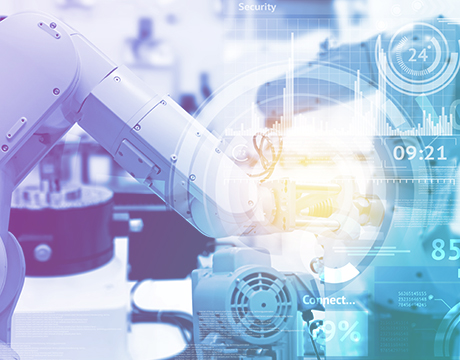
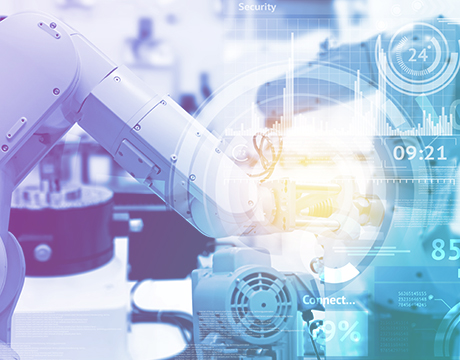