Origami Inspires Bendable 3D-Printed Ceramics
Origami Inspires Bendable 3D-Printed Ceramics
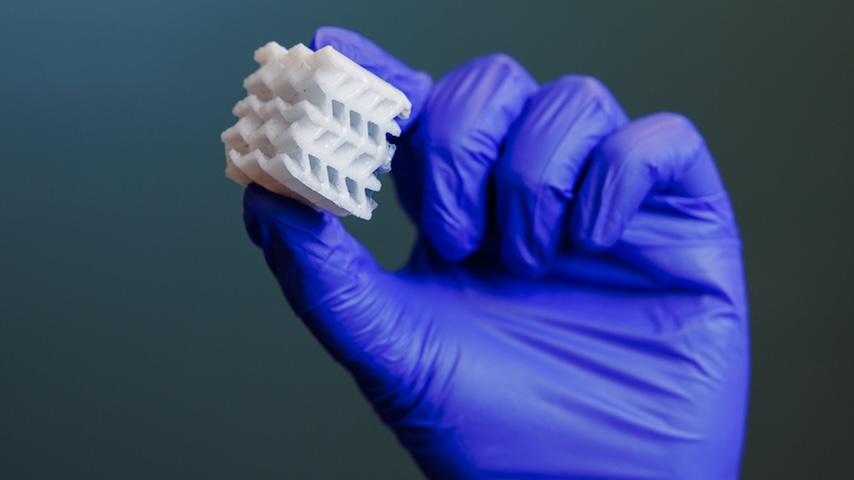
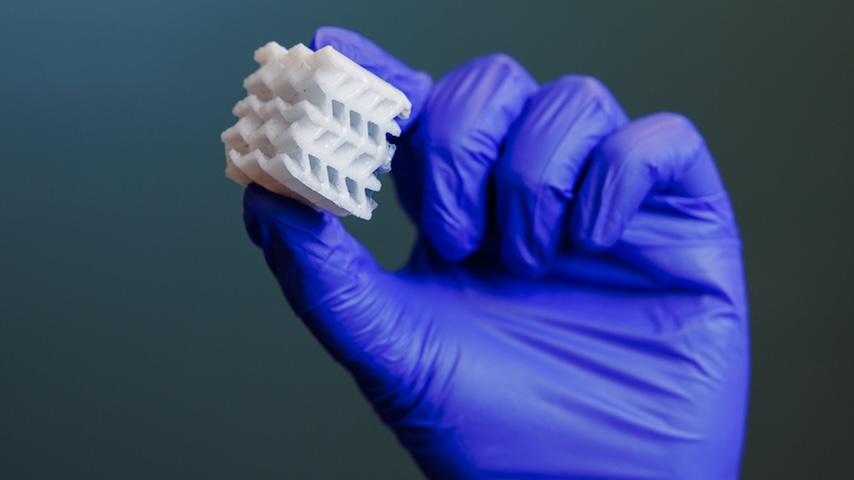
Multidisciplinary research brought together origami, materials science, and 3D printing to yield flexible ceramic structures.
Think about ceramic materials and chances are that the trait “bendable” isn’t something that comes to mind. But a team of researchers at the University of Houston (UH) has developed a new type of ceramic structure that is capable of bending, thanks to some inspiration from origami and the help of 3D printing.
“We chose ceramics because, although they’re incredibly strong, biocompatible, used in many prosthetics and aerospace applications, they’re also notoriously brittle—once they crack, they fail catastrophically,” explained Maksud Rahman, assistant professor of mechanical and aerospace engineering at UH. “That made us wonder: is there a way to make ceramics more damage-tolerant? That’s where origami came in.”
Back in 1970, Japanese astrophysicist Koryo Miura invented the Miura-ori—a specific pattern of folding a sheet of paper into a tessellation of parallelograms that allows the sheet to fold and unfold from opposing corners in one seamless movement. It’s one of the most well-known folds in origami and has even been applied in space with solar panels.
The UH team set out to 3D print a ceramic structure based on the Miura-ori, then coated the material with a biocompatible polymer. This completely changed the failure mode of the ceramic structures and made them damage-tolerant, Rahman said. Instead of breaking, the structure could now be compressed or flexed and then return to its original shape.
You Might Also Enjoy: 3D-Printed Fabric Hardens and Softens on Command
“Ceramics are extremely brittle by nature. Since origami structures rely on some degree of bending or flexibility, we faced a key question: How do you make a brittle material like ceramic accommodate that?” Rahman said. “Our solution was to apply a flexible coating that could enable controlled deformation without compromising structural integrity. There was also another challenge in making this coating reach all the corners of a structure as complicated as origami. We managed that by using a vacuum during dip coating to ensure that the polymer reached all crevices.”
Going from concept to its first finished prototype took the team about five months.
Although past work on origami engineering has demonstrated that folding patterns can result in structures that absorb energy and distribute stress, nearly all that research utilized flexible materials, Rahman added, noting that this is the first demonstration of origami design on a brittle material.
“The most difficult challenge was 3D printing a highly complex structure like the 3D Miura-ori using ceramic," Rahman explained. “Especially when the pre-ceramic resin itself was still experimental, it presented a whole new level of difficulty. We had to go through many iterations to figure out the smallest possible features that could still be accurately printed in such a complex architecture with this experimental resin.”
Tests under static and cyclic compression, supplemented with computer simulations, all showed that the 3D-printed and biopolymer-coated structure was far tougher than traditional ceramic.
Discover the Benefits of ASME Membership
“At a high level, the magic comes from the combination of architecture, material, and coating. The ceramic itself gives the structure strength; however, it is extremely brittle,” he continued. “The origami-inspired geometry spreads and redirects stress, which helps prevent cracks from concentrating in one place. However, stress concentration still occurs at the crevices for the uncoated ceramic origami structure. So finally, the coating redirects those stresses away from the crevices and thus stop crack propagations.”
The team’s findings were detailed in “Macroscale ceramic origami structures with hyper-elastic coating,” recently published in Advanced Composites and Hybrid Materials.
Looking ahead, the team hopes to achieve better 2D and 3D bendability in brittle materials, which will require modifying the design to make ceramic structure more flexible for specific uses, Rahman said.
“We’re also excited in using AI-based algorithms to optimize the designs to resolve one of the big challenges: low bending toughness of ceramic. Ultimately the goal is to create customized, lightweight ceramic structures that can handle stress better, which could be useful in everything from protective gear to aerospace components,” he added.
Rahman emphasized that this interdisciplinary research, combining origami, materials science, and 3D printing, led to a surprising breakthrough and an entirely new way to work with ceramics that wasn’t previously possible.
“Origami is more than an art—it’s a powerful design tool that can reshape how we approach challenges in both biomedical and engineering fields,” Rahman said. “This work demonstrates how folding patterns can unlock new functionalities in even the most fragile materials.”
Louise Poirier is senior editor.
“We chose ceramics because, although they’re incredibly strong, biocompatible, used in many prosthetics and aerospace applications, they’re also notoriously brittle—once they crack, they fail catastrophically,” explained Maksud Rahman, assistant professor of mechanical and aerospace engineering at UH. “That made us wonder: is there a way to make ceramics more damage-tolerant? That’s where origami came in.”
Back in 1970, Japanese astrophysicist Koryo Miura invented the Miura-ori—a specific pattern of folding a sheet of paper into a tessellation of parallelograms that allows the sheet to fold and unfold from opposing corners in one seamless movement. It’s one of the most well-known folds in origami and has even been applied in space with solar panels.
The UH team set out to 3D print a ceramic structure based on the Miura-ori, then coated the material with a biocompatible polymer. This completely changed the failure mode of the ceramic structures and made them damage-tolerant, Rahman said. Instead of breaking, the structure could now be compressed or flexed and then return to its original shape.
You Might Also Enjoy: 3D-Printed Fabric Hardens and Softens on Command
“Ceramics are extremely brittle by nature. Since origami structures rely on some degree of bending or flexibility, we faced a key question: How do you make a brittle material like ceramic accommodate that?” Rahman said. “Our solution was to apply a flexible coating that could enable controlled deformation without compromising structural integrity. There was also another challenge in making this coating reach all the corners of a structure as complicated as origami. We managed that by using a vacuum during dip coating to ensure that the polymer reached all crevices.”
Going from concept to its first finished prototype took the team about five months.
Although past work on origami engineering has demonstrated that folding patterns can result in structures that absorb energy and distribute stress, nearly all that research utilized flexible materials, Rahman added, noting that this is the first demonstration of origami design on a brittle material.
“The most difficult challenge was 3D printing a highly complex structure like the 3D Miura-ori using ceramic," Rahman explained. “Especially when the pre-ceramic resin itself was still experimental, it presented a whole new level of difficulty. We had to go through many iterations to figure out the smallest possible features that could still be accurately printed in such a complex architecture with this experimental resin.”
Tests under static and cyclic compression, supplemented with computer simulations, all showed that the 3D-printed and biopolymer-coated structure was far tougher than traditional ceramic.
Discover the Benefits of ASME Membership
“At a high level, the magic comes from the combination of architecture, material, and coating. The ceramic itself gives the structure strength; however, it is extremely brittle,” he continued. “The origami-inspired geometry spreads and redirects stress, which helps prevent cracks from concentrating in one place. However, stress concentration still occurs at the crevices for the uncoated ceramic origami structure. So finally, the coating redirects those stresses away from the crevices and thus stop crack propagations.”
The team’s findings were detailed in “Macroscale ceramic origami structures with hyper-elastic coating,” recently published in Advanced Composites and Hybrid Materials.
Looking ahead, the team hopes to achieve better 2D and 3D bendability in brittle materials, which will require modifying the design to make ceramic structure more flexible for specific uses, Rahman said.
“We’re also excited in using AI-based algorithms to optimize the designs to resolve one of the big challenges: low bending toughness of ceramic. Ultimately the goal is to create customized, lightweight ceramic structures that can handle stress better, which could be useful in everything from protective gear to aerospace components,” he added.
Rahman emphasized that this interdisciplinary research, combining origami, materials science, and 3D printing, led to a surprising breakthrough and an entirely new way to work with ceramics that wasn’t previously possible.
“Origami is more than an art—it’s a powerful design tool that can reshape how we approach challenges in both biomedical and engineering fields,” Rahman said. “This work demonstrates how folding patterns can unlock new functionalities in even the most fragile materials.”
Louise Poirier is senior editor.
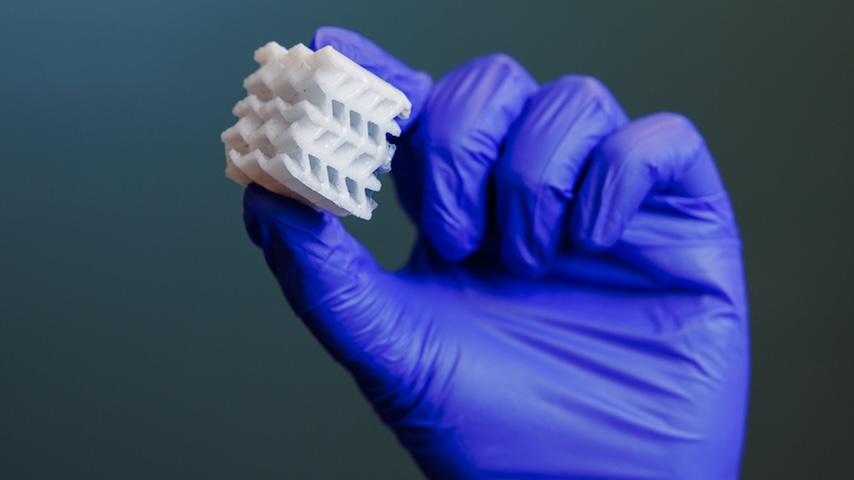
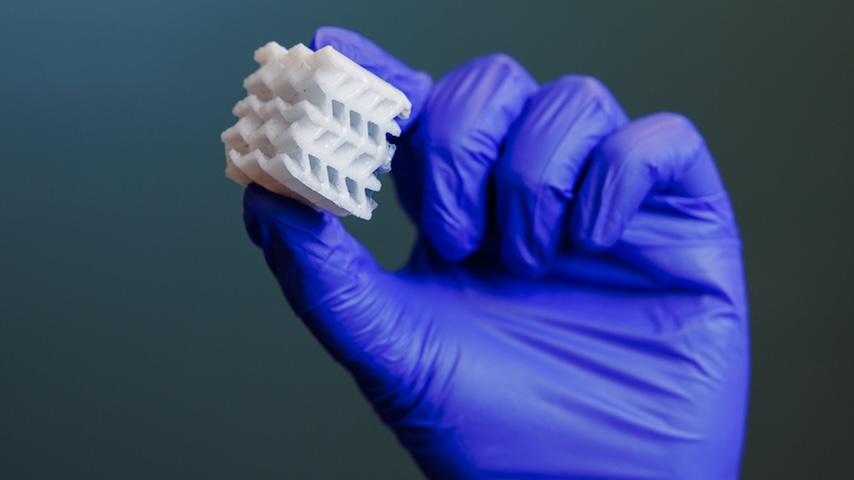